Can 304 stainless steel be heat treated?
Are you trying to increase the hardness of your 304 stainless steel components, assuming a simple heat treatment will do the trick? This common misconception can lead to wasted time, ruined materials, and project delays when the steel fails to harden as expected.
Unlike carbon steels, 304 stainless steel hardening cannot be achieved by traditional heat treatment methods like quenching and tempering. Its austenitic crystal structure does not undergo the phase transformation required for hardening, though it can be hardened significantly through cold working.
This distinction is fundamental to working with austenitic stainless steels and is a frequent topic of conversation I have with clients. In my work at MFY, guiding partners from initial design to final application, clarifying this point is crucial for successful outcomes. Let's explore the metallurgy behind this behavior and the proper methods to achieve the strength you need.
Understanding this principle is about more than just metallurgy; it's about efficient manufacturing and resource allocation. The global steel market operates on clear specifications, and attempting to force a material to behave outside its intrinsic properties is a recipe for inefficiency. Data shows that fabrication errors, including incorrect heat treatment attempts, are a significant source of waste in the metalworking industry. By appreciating почему 304 responds to cold work rather than heat treatment, our clients—from equipment integrators to construction contractors—can optimize their processes, avoid costly trial-and-error, and select the right material for the job from the outset.
What are the intrinsic properties of 304 stainless steel regarding heat treatment?
Are you puzzled why your attempts to heat-treat 304 stainless steel aren't yielding a harder material? Applying the wrong process based on assumptions about steel can compromise the integrity of your components. It's essential to understand the material's fundamental nature before processing it.
The intrinsic properties of 304 stainless steel properties are defined by its stable austenitic crystal structure. This face-centered cubic structure is non-magnetic and remains stable from cryogenic temperatures up to its melting point, preventing the phase change necessary for quench hardening.
This austenitic nature is the key. It's what gives 304 its celebrated toughness and formability, but it's also precisely why it doesn't respond to hardening heat treatments in the same way as other steels. I often explain this to clients who are more familiar with carbon steels. For example, a manufacturing partner in India was developing a new line of high-pressure valves and was accustomed to tempering carbon steel components. They were surprised when their initial tests on 304 showed no increase in hardness. This led to a crucial discussion about the material's metallurgy, shifting their strategy from heat treatment to leveraging the effects of cold working in their manufacturing process. This understanding is foundational; it prevents misapplication of resources and ensures the material is used in a way that leverages its inherent strengths, like its exceptional formability and corrosion resistance, rather than fighting against its basic properties.
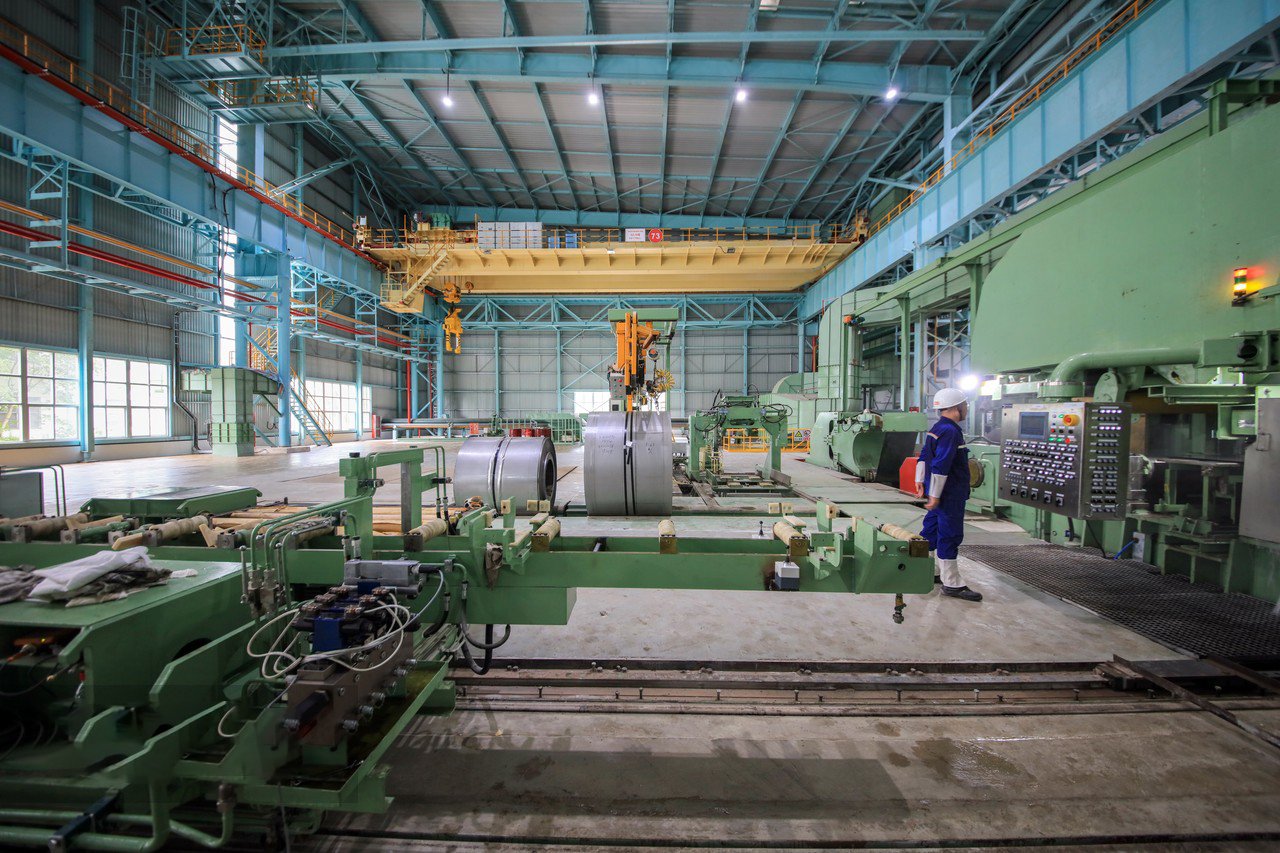
The properties of any steel are dictated by its microstructure—the specific arrangement of its atoms. For 304 stainless steel, this structure is known as austenite, and its stability is the source of both its greatest strengths and its key limitations regarding heat treatment. At MFY, our role extends beyond simply supplying steel; we act as partners in innovation, ensuring our clients have the metallurgical knowledge to succeed. When a client understands that 304's austenitic structure is the reason for its excellent ductility and corrosion resistance, they can design their products and processes to capitalize on these features. Conversely, knowing that this same structure prevents traditional hardening allows them to avoid costly and ineffective processing steps. This deeper, collaborative understanding of material science is what enables the creation of efficient, resilient, and competitive products in a global market. It’s a dialogue we foster with every client, from distributors to large-scale engineering contractors.
The Stable World of Austenite
The defining characteristic of 304 stainless steel is its austenitic microstructure. This is a face-centered cubic (FCC) crystal lattice, a specific, stable arrangement of iron, chromium, and nickel atoms. The high nickel content (typically 8-10.5%) in 304 is the primary "austenite stabilizer." It ensures that this FCC structure remains stable across a very wide temperature range, from deep cryogenic levels all the way up to its melting point of around 1400°C (2550°F). This is fundamentally different from plain carbon and low-alloy steels, whose crystal structures transform from austenite to ferrite or other phases as they cool.
This structural stability is a major asset. It's the reason 304 retains excellent toughness and ductility even at extremely low temperatures, making it suitable for cryogenic applications where other steels would become brittle. I recall a project with an equipment integrator building components for a liquefied natural gas (LNG) facility. They required a material that would not fracture at -162°C (-260°F), and 304 was the ideal choice precisely because its austenitic structure doesn't undergo a ductile-to-brittle transition. This property is directly linked to its inability to be hardened by heat treatment.
Hardening via quenching relies on a phase transformation—specifically, trapping the steel in a hard, brittle martensitic phase. Since 304's austenite is stable upon cooling, no matter how rapidly it is quenched from a high temperature, it simply remains austenite. The atoms don't rearrange into the body-centered tetragonal structure of martensite. Therefore, attempting to quench-harden 304 is a futile exercise; the material remains relatively soft and ductile. Understanding this core principle is the first step in mastering the application of 304 stainless steel.
The Role of Alloying Elements
The specific recipe of alloying elements in 304 stainless steel is finely tuned to create and maintain its austenitic structure and other key properties. Chromium, at 18-20%, is the primary ingredient for corrosion resistance, forming the passive oxide layer that protects the steel. However, chromium is technically a "ferrite stabilizer," meaning on its own, it would encourage a different crystal structure. This is where nickel becomes critical. As a potent austenite stabilizer, nickel counteracts the ferritic tendency of chromium, ensuring the desirable austenitic structure is maintained at room temperature.
This balance of elements is crucial. If the nickel content were significantly lower, the steel might become duplex (a mix of austenite and ferrite) or fully ferritic, completely changing its mechanical properties and response to heat. Other elements play minor but important roles. Manganese, also an austenite stabilizer, is present and allows for a slight reduction in the required nickel content. Carbon, while kept low (typically below 0.08%), is also an austenite stabilizer, but its primary role in this context relates to the potential for sensitization during welding, which is why the low-carbon "L" grade (304L) exists.
When we at MFY consult with clients, we often discuss the "Schaeffler Diagram," a tool metallurgists use to predict the microstructure of stainless steel based on its "nickel equivalents" and "chromium equivalents." This allows us to explain visually why 304, with its specific alloy content, falls squarely in the austenitic field. This technical insight helps clients appreciate that their material isn't just a commodity but a carefully engineered alloy, and its properties are a direct result of this precise chemical composition.
What is Solution Annealing?
While 304 cannot be hardened by heat treatment, it is very commonly subjected to a heat treatment process called отжиг or, more accurately, solution annealing. The purpose of annealing is the exact opposite of hardening: it is used to soften the steel, relieve internal stresses from fabrication, and re-dissolve chromium carbides back into the solution, thereby restoring maximum corrosion resistance. The process involves heating the steel to a high temperature, typically 1010-1120°C (1850-2050°F), holding it long enough for the structure to become uniform and for any carbides to dissolve, and then cooling it rapidly (usually by water quenching).
This rapid quench is critical. Unlike with carbon steels where a rapid quench induces hardness, in 304 it serves to "lock in" the softened, stress-free, and corrosion-resistant austenitic state by preventing chromium carbides from precipitating as the steel cools through the sensitization range (425-860°C). This is a vital process after heavy forming or welding. A client of ours who manufactures complex pipe fittings for the chemical industry in the Middle East anneals every part after fabrication. This ensures that any stresses induced during bending and any potential sensitization from welding are completely eliminated, resulting in a product with uniform properties and maximum durability.
Therefore, when we say 304 cannot be "heat treated," we specifically mean it cannot be hardened. It is, in fact, frequently heat treated via annealing to optimize its properties for service. This is a crucial distinction that prevents confusion and ensures proper manufacturing protocols are followed. It's a key piece of practical knowledge we share to help our partners get the most out of our materials.
304L has lower carbon than 304Правда
The "L" grade's reduced carbon content (≤0.03%) minimizes sensitization risks during welding.
Quenching 304 improves corrosion resistanceЛожь
Quenching after solution annealing prevents carbide precipitation, but doesn't harden the material.
Why is traditional heat treatment not applicable to 304 stainless steel?
Frustrated that your standard heat treatment process isn't working on 304 stainless steel? Applying hardening techniques designed for carbon steel will not only fail but could also negatively impact the material's inherent corrosion resistance. A different approach is required.
Traditional hardening, which involves quenching to form a hard martensitic phase, is not applicable to 304 stainless steel. Its stable austenitic structure does not transform upon cooling, so the fundamental mechanism of quench-hardening is absent in this alloy.
This is a point of divergence from the world of carbon and alloy steels, and understanding it is key to effective design and fabrication. When a new client, especially one with a background in heavy machinery or tool making, asks us to supply "hardened 304," it opens up a vital conversation. I explain that unlike a 4140 alloy steel, which transforms its crystal structure when quenched, 304's structure is stable. We then pivot the discussion to the correct method for increasing its strength: strain hardening1. This shift in perspective is crucial. Instead of fighting the material’s nature, we can harness its unique properties. This knowledge prevents our partners from investing in useless and potentially detrimental heating processes and guides them toward manufacturing strategies that are both effective and efficient, ultimately leading to a better and more reliable final product.
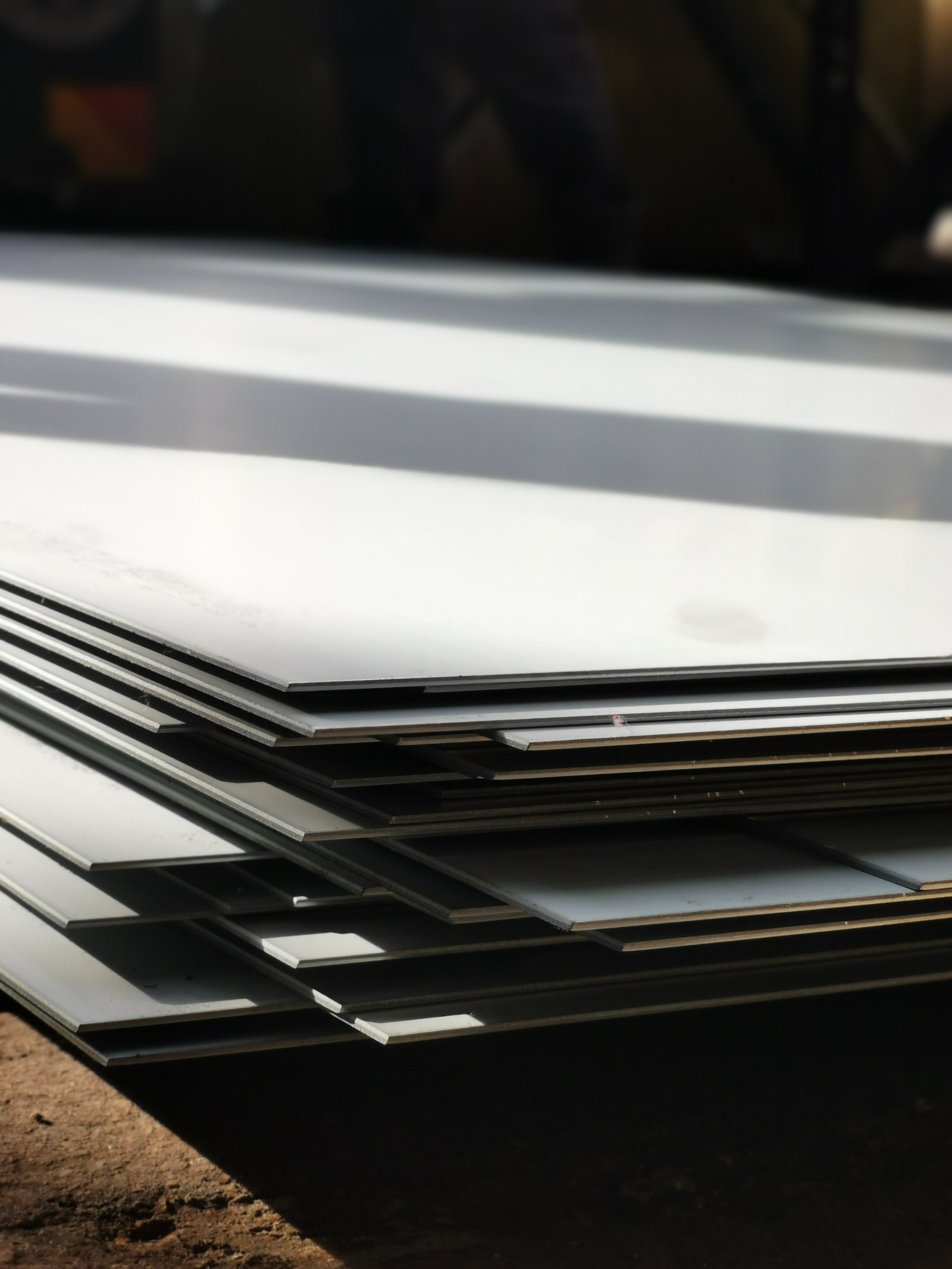
To truly grasp why traditional heat treatment fails, we must compare the metallurgical journey of 304 stainless steel with that of a hardenable carbon steel. The difference is not trivial; it's a fundamental divergence in crystallographic behavior. For our clients in manufacturing and engineering, this isn't just an academic detail—it has direct implications for process design, equipment selection, and cost management. At MFY, we emphasize this because a misunderstanding here can lead to significant operational inefficiencies. A furnace cycle dedicated to a futile hardening attempt on 304 is a waste of energy, time, and money. By providing clear, practical explanations of the underlying science, we empower our clients to streamline their operations, avoid common pitfalls, and invest their resources in processes, like cold working, that yield tangible results. This is a cornerstone of our role as a value-adding partner in the global steel supply chain.
The Martensitic Transformation: What 304 Lacks
The textbook method for hardening steel is inducing a martensitic transformation. In a typical carbon steel, when it's heated to a high temperature, it forms an austenitic (FCC) structure, just like 304. However, because its austenite is not stabilized by high nickel content, it is unstable at lower temperatures. When the steel is rapidly quenched in water or oil, the carbon atoms don't have time to diffuse out and form carbides. Instead, the crystal lattice is forced to shear into a new, highly strained, and distorted structure called martensite. This body-centered tetragonal (BCT) structure is extremely hard and brittle, and it is the key to high-strength steel. This hardened steel is then "tempered" (reheated to a lower temperature) to relieve some of the brittleness and achieve a desired balance of hardness and toughness.
This entire process is predicated on the austenite being unstable at room temperature. For 304 stainless steel, this condition is never met. Its high nickel and chromium content ensures the austenitic structure is perfectly stable and happy to exist at room temperature and below. When 304 is quenched from 1050°C, it cools so rapidly that there is no time for carbides to form, but instead of transforming to martensite, it simply remains as soft, ductile austenite. The fundamental trigger for the hardening reaction—the instability of the austenite phase—is completely absent.
I once walked a client, a tool and die maker, through this process. He was trying to create a forming die from 304 for a corrosive application and was frustrated by his inability to harden the surface. By explaining the absence of the martensitic transformation and showing him photomicrographs of quenched 304 versus quenched tool steel, the concept became clear. The solution was not to heat treat the 304 but to select an entirely different grade—a martensitic stainless steel (like 440C) or a precipitation-hardening grade—that was designed for this purpose.
Contrasting with Hardenable Stainless Steels
It is crucial to note that many other types of stainless steel can be hardened by heat treatment. The key is that they are not austenitic. Martensitic stainless steels, such as grades 410, 420, and 440C, are a prime example. These alloys have high chromium but very low nickel content, so their structure at room temperature is not austenitic. They are formulated specifically to undergo the martensitic transformation, just like carbon steels. They are widely used for applications requiring a combination of good corrosion resistance and high hardness, such as cutlery, surgical instruments, and valve components.
Another category is precipitation-hardening (PH) stainless steels, like 17-4 PH. These are sophisticated alloys that get their strength from a different mechanism. They are first solution-annealed (similar to 304) and then subjected to a lower-temperature aging heat treatment. During this aging process, microscopic particles of copper or other elements precipitate within the steel's matrix, acting as obstacles to dislocation movement and dramatically increasing the material's strength and hardness.
We often guide clients to these alternative grades when their application requirements cannot be met by 304. For instance, an engineering contractor for an aerospace application needed a high-strength, corrosion-resistant fastener. Cold-worked 304 could provide some strength, but not enough. The clear solution was a precipitation-hardening grade. By having this broader conversation about the different families of stainless steel, we ensure the client gets the optimal material, even if it isn't the common 304 grade. This demonstrates our commitment to providing solutions, not just selling a specific product.
The Negative Effects of Improper Heating
Attempting to heat treat 304 as if it were a carbon steel is not just ineffective; it can be actively harmful to the material. The most significant risk is "sensitization." If 304 stainless steel is heated or slowly cooled through the temperature range of approximately 425°C to 860°C (800°F to 1580°F), the carbon in the steel will combine with the chromium at the grain boundaries to form chromium carbides. This process locks up the chromium, depleting it from the area immediately adjacent to the grain boundaries.
This chromium-depleted zone no longer has the 10.5% minimum chromium required for passivity. The result is that the material becomes highly susceptible to intergranular corrosion, where corrosive attack occurs preferentially along these weakened grain boundaries. A component that has been sensitized can fail catastrophically in a corrosive environment, even though it may look perfectly fine on the surface. This is why post-weld heat treatment, a common practice for some alloys, is generally not performed on 304 unless it is a full solution anneal with a rapid quench.
This is a critical quality control point we stress to all fabricators. A client once reported that some 304 tanks were showing premature corrosion near fittings that had been stress-relieved at a mid-range temperature by a subcontractor. An analysis quickly revealed sensitization. The "heat treatment" intended to improve the part had actually destroyed its corrosion resistance. This is why we almost always recommend using the 304L grade2 for welded structures, as its very low carbon content (0.03% max) severely restricts carbide formation, providing a much larger margin of safety against sensitization.
304 stainless steel cannot be hardened by quenchingПравда
304's stable austenitic structure doesn't transform to martensite when quenched, unlike carbon steels.
All stainless steels can be hardened by heat treatmentЛожь
Only martensitic and precipitation-hardening stainless steels respond to heat treatment; austenitic grades like 304 do not.
How does cold working impact the hardness of 304 stainless steel?
Are you looking for a practical way to increase the strength and hardness of 304 stainless steel for your application? Since conventional heat treatment is off the table, understanding the power of mechanical processing is your key to unlocking the material's full potential.
Cold working, such as rolling, drawing, or bending at ambient temperature, is the primary method for hardening 304 stainless steel. This process deforms the crystal structure, significantly increasing its tensile strength, yield strength, and hardness, albeit at the expense of ductility.
This phenomenon, known as work hardening or strain hardening, is something we leverage daily at MFY to serve our clients. For example, a manufacturer of high-strength industrial strapping needs material that is both corrosion-resistant and incredibly strong. We supply them with 304 stainless steel that has been cold-rolled to a specific "temper," or hardness level, to meet their precise tensile strength requirements. This controlled deformation process transforms the soft, ductile annealed steel into a high-performance product. Grasping the mechanics of cold working is essential for any engineer or fabricator looking to utilize 304 in applications that demand more than just its baseline strength. It allows for a level of customization in mechanical properties that makes this versatile alloy even more valuable across a wider range of demanding industrial uses.
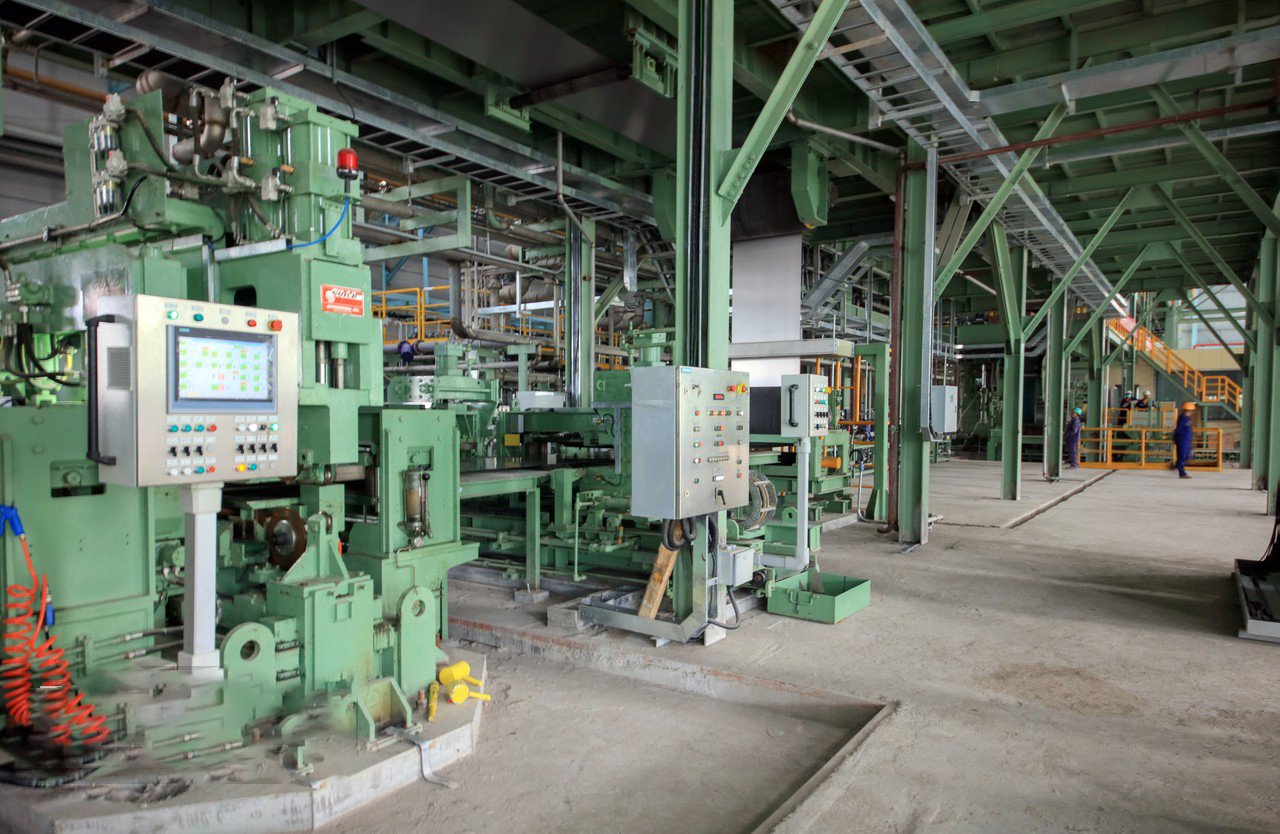
The transformation of soft, annealed 304 нержавеющая сталь3 into a high-strength material through cold working is a remarkable and highly controllable process. It’s a perfect example of using mechanical energy to fundamentally alter a material's properties at a microscopic level. For our clients in demanding sectors like automotive, spring manufacturing, and construction, this isn't just a side effect; it's a targeted manufacturing strategy. We don't just sell them a coil of steel; we provide a material with a specific set of mechanical properties—a "temper"—achieved through precise rolling reductions. This level of control is vital. It allows an engineer to design a component that is lightweight yet strong, durable yet corrosion-resistant. Understanding the relationship between the degree of cold work and the resulting mechanical properties is critical for product innovation and optimization, a journey on which we are proud to guide our partners.
The Mechanism of Strain Hardening
Strain hardening is a strengthening process that results from the plastic deformation of a metal. Within the crystalline structure of 304 stainless steel are imperfections called dislocations. When the material is in its soft, annealed state, these dislocations can move relatively easily, which is what allows the material to be ductile and easily formed. However, as the steel is cold-worked—for example, by being passed through rollers that reduce its thickness—new dislocations are created and they begin to tangle and pile up. This growing tangle of dislocations acts as a barrier, impeding further dislocation movement. More and more force (stress) is required to cause additional deformation, which manifests on a macroscopic level as an increase in the material's hardness and strength.
This process is highly effective in austenitic stainless steels like 304 due to their specific crystal structure. The rate of work hardening is significantly higher in 304 than in many other metals. A relatively small amount of cold reduction can lead to a substantial increase in strength. For example, a typical annealed 304 might have a tensile strength of around 515 MPa (75 ksi). After being cold-rolled to a "full hard" temper, that tensile strength can skyrocket to over 1280 MPa (185 ksi).
We work closely with clients to specify the correct level of cold work for their needs. A spring manufacturer, for instance, requires a very high tensile strength to ensure the spring has the necessary elastic properties. We provide them with cold-rolled strip manufactured to a precise thickness reduction that guarantees the required mechanical properties. This is a science, not guesswork, and it allows for the engineering of high-performance components from a standard alloy.
The Trade-Off: Strength vs. Ductility
The benefits of increased strength from cold working come with an important trade-off: a reduction in ductility. Ductility is the material's ability to deform plastically without fracturing, often measured as "percent elongation" in a tensile test. An annealed 304 sheet might have an elongation of over 60%, allowing it to be deep-drawn into a kitchen sink. However, a full-hard, cold-worked strip of 304 might have an elongation of less than 5%. This means it is very strong but will crack if someone tries to bend it to a sharp radius.
This inverse relationship between strength and ductility is a fundamental principle that must be respected in design and manufacturing. A part that requires significant forming must be made from annealed or lightly cold-worked material. If high strength is also needed in the final part, the design must leverage the fact that the forming process itself will induce work hardening. A classic example is in automotive body panels, where the stamping process that forms the panel's shape also strategically hardens the material in critical areas.
We recently assisted a client who was manufacturing a complex stamped bracket. They were trying to use a half-hard temper to meet final strength requirements, but the material kept cracking during the stamping process. Our recommendation was to switch to an annealed 304. The stamping process provided enough localized work hardening to meet their strength targets in the critical areas, while the initial high ductility of the annealed material eliminated the cracking issue. This kind of process optimization saves time, reduces scrap rates, and is a key part of the value we add.
Specifying Cold-Worked Tempers
To standardize the properties of cold-worked stainless steel, the industry uses a system of "tempers." These tempers, such as 1/4 Hard, 1/2 Hard, 3/4 Hard, and Full Hard, correspond to specific ranges of mechanical properties achieved through controlled amounts of cold reduction. This allows engineers and designers to specify a material with predictable performance characteristics. When a client orders "1/2 Hard 304 sheet" from MFY, they are not just ordering a thickness; they are ordering a guaranteed range of tensile strength, yield strength, and hardness.
This system is vital for ensuring consistency in manufacturing. For a client producing thousands of identical metal clips, the spring-back characteristics of the material must be the same from the first part to the last. This consistency is only possible if the material is supplied to a specific temper. We use precise rolling mills and tension controls to produce cold-rolled coils that meet these exacting standards for our clients worldwide.
The table below illustrates the typical evolution of mechanical properties in 304 stainless steel as it is cold-worked from the annealed state to full hard. This data is essential for any designer choosing the right starting material for their process.
Temper | Tensile Strength (MPa) | Yield Strength (MPa) | Elongation (% in 50mm) | Hardness (Rockwell) |
---|---|---|---|---|
Annealed | 515 - 690 | 205 - 310 | 40 - 60 | B80 |
1/4 Hard | 860 - 1030 | 515 - 760 | 10 - 25 | C25 |
1/2 Hard | 1030 - 1210 | 760 - 1000 | 5 - 15 | C32 |
Full Hard | 1280+ | 1000+ | < 5 | C41 |
Note: These values are typical and can vary based on exact specifications and material thickness.
This ability to tailor the mechanical properties of 304 through cold work transforms it from a general-purpose steel into a high-performance engineering material.
Cold working increases 304 steel hardnessПравда
Plastic deformation creates dislocation tangles that impede movement, resulting in higher hardness.
Cold working improves both strength and ductilityЛожь
While strength increases, ductility decreases significantly due to dislocation accumulation.
What alternative methods are available to enhance 304 stainless steel performance?
Are you pushing the limits of what standard or cold-worked 304 can do? When your application demands hardness or wear resistance beyond its inherent capabilities, it's time to look at advanced alternatives, either by modifying the surface or selecting a different alloy altogether.
Besides cold working, the performance of 304 can be enhanced through surface treatments like nitriding or PVD coating to increase surface hardness and wear resistance. For superior bulk properties, selecting a more appropriate grade, like a martensitic or PH stainless steel, is the best alternative.
Choosing the right path requires a clear understanding of your primary performance requirement—is it surface wear, or is it through-thickness strength? I often have this strategic discussion with clients in high-tech industries. For a client making medical instruments, a PVD coating on a 304 body provides a hard, biocompatible cutting edge without altering the bulk material's toughness. For another client designing high-pressure actuators, the only viable solution was to transition away from 304 to a 17-4 PH alloy4 that could be heat-treated to achieve the necessary yield strength. At MFY, our vision is to facilitate the global expansion of China's stainless steel supply chain, which means guiding our partners to the most effective solution, whether it's an advanced treatment for a familiar grade or a strategic shift to a high-performance alloy from our extensive network.
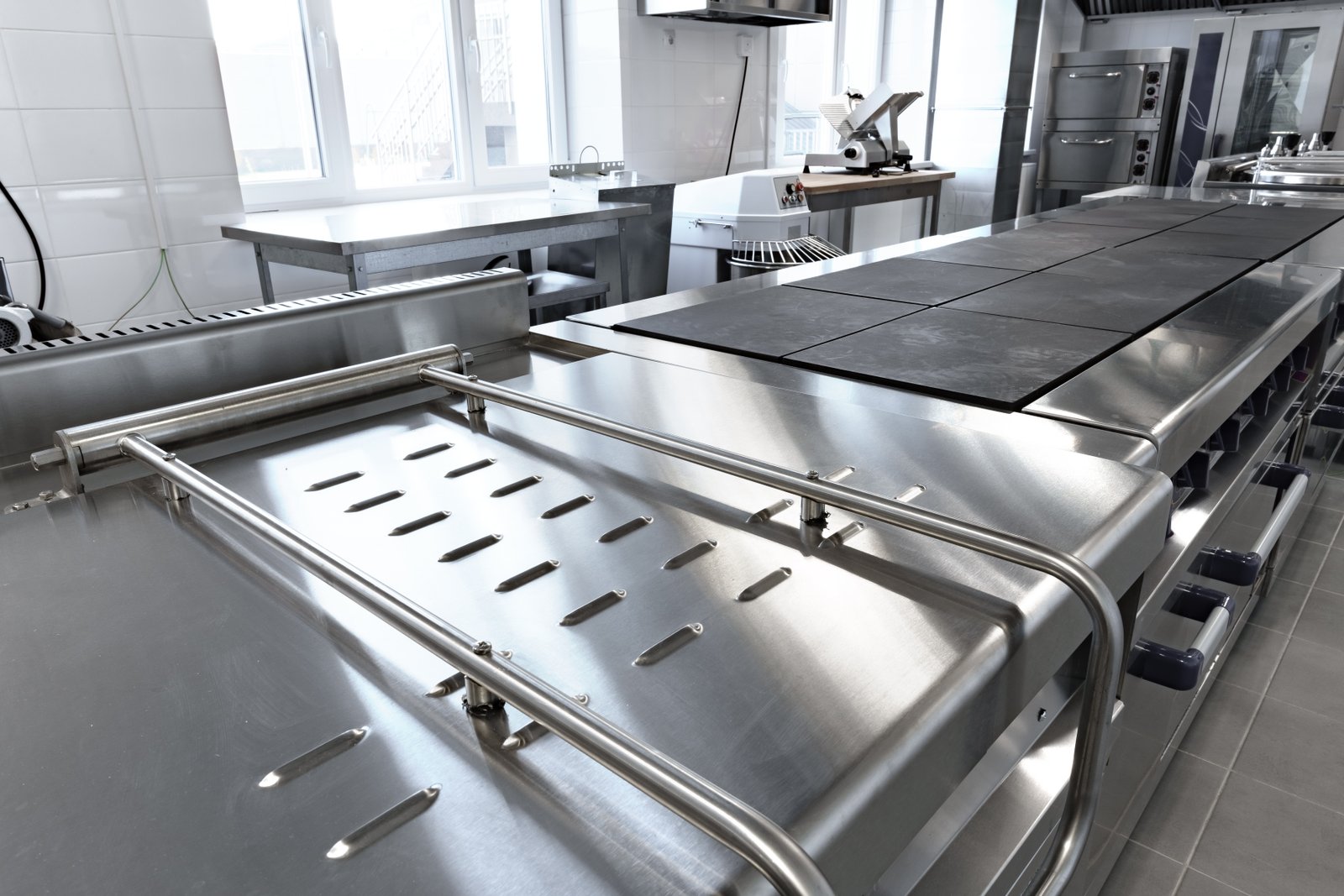
When an application's demands exceed the inherent capabilities of 304 stainless steel, even in a cold-worked state, a more advanced solution is required. This is where a true supply chain partner proves its value, moving beyond a single product to offer a spectrum of solutions. At MFY, our integrated model, combining production, trade, and innovation, allows us to have these advanced conversations. We don't just see a request for "stronger 304"; we see an engineering challenge. The solution might lie in sophisticated surface engineering to create a composite-like material with a hard surface and a tough core, or it may involve leveraging our global network to source a specialty alloy designed specifically for that level of stress. This holistic approach ensures our clients aren't trying to force a square peg into a round hole. Instead, they are equipped with the best possible material or process, enabling them to innovate and compete at the highest level.
Surface Engineering: Nitriding and Carburizing
For applications where surface hardness and wear resistance are the primary concerns, modifying the surface of the 304 component can be an effective strategy. Processes like nitriding, carburizing, or nitrocarburizing introduce nitrogen and/or carbon into the surface of the steel at elevated temperatures. These elements form extremely hard nitride and carbide compounds, creating a "case" or hardened layer that can be many times harder than the base material. This case-hardening significantly improves resistance to adhesive wear, galling, and erosion, while the underlying core of the material remains tough and ductile 304 austenite.
This approach is particularly valuable for components that experience sliding contact. We consulted for an equipment integrator that was designing a new food processing machine with several moving parts made from 304 for corrosion resistance. However, they were experiencing galling—a form of severe adhesive wear—between the stainless components. Heat treating for hardness was not an option. We connected them with a specialist in low-temperature colossal supersaturation (LTCS) nitriding. This advanced process is performed at temperatures low enough to avoid sensitizing the stainless steel, while still creating a very hard, wear-resistant surface. The treated parts performed flawlessly, solving the galling issue without compromising corrosion resistance.
While effective, these processes add complexity and cost. They are specialized treatments that require sophisticated equipment and control. The decision to use a surface treatment is a cost-benefit analysis. Is the performance gain worth the additional processing expense? For high-value components where wear is a primary failure mode, the answer is often yes. It's a targeted solution for a specific problem, enhancing 304 beyond its natural capabilities.
Advanced Coatings: PVD and Plating
Another powerful method for enhancing surface performance is the application of advanced coatings. Physical Vapor Deposition (PVD) is a process where a thin film of a very hard ceramic material, such as titanium nitride (TiN) or chromium nitride (CrN), is deposited onto the surface of the 304 component in a vacuum chamber. These coatings are extremely hard, inert, and have a low coefficient of friction. They are commonly used on cutting tools, medical instruments, and decorative hardware. A PVD coating can give a 304 substrate a surface hardness that rivals hardened tool steels, along with a distinctive color (TiN is gold, for example).
Plating is another option. While chrome plating is common for aesthetics on other materials, hard chromium or electroless nickel plating can be applied to 304 to improve wear and corrosion resistance in specific environments. Electroless nickel coatings, particularly those co-deposited with particles like silicon carbide, can provide a very hard and uniformly thick protective layer, even on complex shapes.
I worked with a manufacturer of high-end marine hardware. While 316 is often the choice for marine environments, they preferred the formability of 304 for their complex designs. To enhance both the wear resistance on moving parts and the corrosion resistance in the harsh saltwater environment, they opted for a specialized duplex coating. This combination of an electroless nickel base coat and a PVD top coat provided a multi-layered defense, giving them the aesthetic and performance characteristics they desired. These coating technologies essentially allow a designer to create a composite material, combining the cost-effectiveness and toughness of a 304 core with the superior surface properties of an advanced ceramic or plated layer.
Strategic Grade Selection: The Ultimate Alternative
Often, the most effective and economical alternative is not to enhance 304, but to select a different grade of steel that is inherently better suited for the job. If high strength and hardness throughout the entire component are required, no surface treatment will suffice. This is where the other families of stainless steel become the clear choice. As mentioned earlier, martensitic grades like 440C can be heat-treated to very high hardness levels and are a go-to for cutting applications. For the ultimate combination of high strength, toughness, and corrosion resistance, precipitation-hardening (PH) grades like 17-4 PH are unmatched.
This is a strategic decision we help our clients make every day. A distributor came to us with a request from their customer, a construction contractor, who needed high-strength, corrosion-resistant anchor bolts. They had been using heavily cold-worked 304, but were reaching the limits of its strength and were concerned about stress corrosion cracking. After reviewing the load requirements and the service environment, we recommended they transition to a duplex stainless steel, such as 2205. Duplex steels have a mixed austenite-ferrite structure and offer significantly higher strength than 304, along with superior resistance to chloride stress corrosion cracking.
While the upfront cost per kilogram for the duplex grade was higher, the ability to use smaller diameter bolts due to the higher strength actually made the final installation more cost-effective. More importantly, it provided a much greater margin of safety. This is the essence of our vision at MFY: to use our deep industry knowledge to drive the global expansion of China's entire stainless steel supply chain, guiding clients to the optimal material, whether it's a common grade like 304 or a specialized alloy that delivers superior performance and long-term value.
Nitriding enhances 304 surface hardnessПравда
Nitriding introduces nitrogen to form hard surface compounds while maintaining the base material's toughness.
PVD coatings alter bulk propertiesЛожь
PVD only modifies surface characteristics; the core material retains its original properties.
What are the best practices for working with 304 stainless steel in industrial applications?
Are you confident your fabrication and design processes are truly optimized for 304 stainless steel? Simply knowing that 304 can't be heat-hardened isn't enough; you must proactively design around its unique properties to avoid costly rework and ensure component reliability.
Best practices for 304 stainless steel involve designing for work hardening, using low-carbon 304L for welded sections to prevent sensitization, and performing solution annealing after heavy forming to restore ductility and corrosion resistance. Proper material specification is paramount.
Adopting these practices transforms material knowledge into a competitive advantage. I have seen this firsthand with our most successful clients. A manufacturing company that produces deep-drawn components, for instance, works with us to select 304 with a specific grain size and low residual stress to maximize formability. They also plan for intermediate annealing on very complex parts. This proactive, science-based approach minimizes their scrap rate and maximizes their production efficiency. By treating the material not as a passive commodity but as an active participant in the manufacturing process, you can unlock new levels of performance and reliability in your final products.
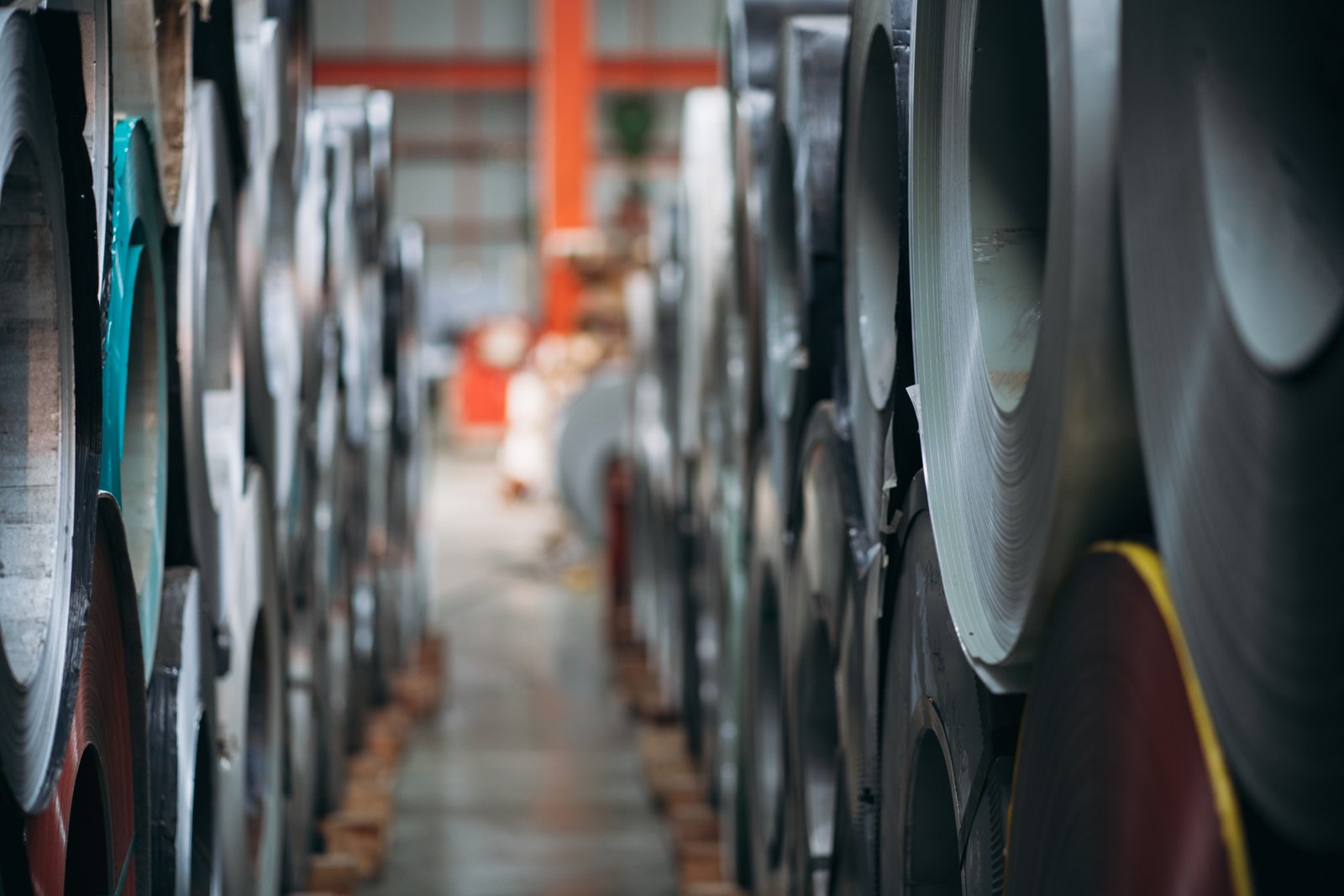
The successful application of 304 stainless steel in an industrial setting5 is a testament to meticulous planning and a deep respect for the material's properties. It’s a synthesis of smart design, precise fabrication, and strategic material selection. At MFY, we champion this integrated approach because it leads to superior outcomes for our clients, whether they are building massive chemical tanks or fabricating intricate automotive components. The best practices are not just rules to follow; they are a mindset. This mindset acknowledges that 304's inability to be quench-hardened is not a weakness, but a characteristic that must be accounted for in the engineering phase. By embracing this, our partners can avoid common pitfalls and instead harness the material's other outstanding qualities—its formability, toughness, and weldability—to their full extent, creating products that are both robust and cost-effective.
Designing for Work Hardening
Since cold working is the only way to harden 304, it should be treated as an integral part of the design and manufacturing process, not as an afterthought. Engineers can intentionally design components where the forming process itself imparts the required final strength. For example, in the design of a structural panel, the location of bends and radii can be planned not just for shape, but to create stiffening ribs that are work-hardened and stronger than the flat sections of the panel. This allows for the use of thinner, lighter starting material, saving both cost and weight.
This requires a sophisticated understanding of material flow and strain. We partner with equipment integrators who use finite element analysis (FEA) software to simulate their forming processes. They can predict how much work hardening will occur in different areas of the part and adjust their tooling and process parameters accordingly. For a client making frames for processing equipment, this meant they could use annealed 304 sheet, which is easy to form, and rely on the press braking operation to achieve the final required stiffness in the corners, where strength is most critical.
Conversely, designers must also be wary of excessive or uncontrolled work hardening. In a multi-stage drawing operation, the material can become so hard after the first few stages that it loses all its ductility, leading to fractures in subsequent steps. The best practice here is to incorporate an in-process solution annealing step. By heating the part between stages, the ductility is restored, allowing for further forming. This is a common practice in the manufacturing of complex hollowware or ammunition casings.
The Critical Choice: 304 vs. 304L
For any application involving welding, the choice between standard 304 and low-carbon 304L is a critical decision. As discussed, welding exposes the material to the sensitization temperature range, risking the precipitation of chromium carbides and leading to intergranular corrosion at the weld. While a full solution anneal after welding can fix this, it is often impractical or impossible for large structures or field repairs. This is where 304L becomes the default best practice. With a maximum carbon content of just 0.03%, 304L has insufficient carbon to form a significant amount of harmful carbides, thereby preserving the corrosion resistance of the heat-affected zone.
I consistently advise clients fabricating welded assemblies—from tanks and pressure vessels to architectural structures and piping systems—to specify 304L. A clear case was a construction contractor building a large, welded stainless steel water feature. They initially quoted standard 304 to save on material cost. We strongly advised them to switch to 304L, explaining that without a post-weld anneal (which was impossible for the huge structure), the welds would be highly vulnerable to corrosion from the treated water. The minor increase in upfront material cost for 304L was negligible compared to the cost of a potential failure and the associated reputational damage.
The rule of thumb is simple: if the component is thicker than a light gauge sheet and will be welded and not subsequently annealed, use 304L. For non-welded applications or those that will be fully annealed after welding, standard 304 is perfectly acceptable. This simple choice is one of the most important best practices in the industry.
Specifying the Right Starting Condition
ly, a crucial best practice is to specify the correct starting condition, or "temper," of the raw material. Ordering "304 stainless steel" is not enough. The purchase order should specify the grade (304 or 304L), the desired finish (e.g., 2B, #4, BA), and, most importantly for mechanical applications, the condition: annealed or a specific cold-worked temper (e.g., 1/2 Hard). This ensures you receive a material that is fit for your purpose.
If you are performing extensive deep drawing, you must start with annealed material that has maximum ductility. If you are machining parts, starting with a lightly cold-worked material can sometimes be beneficial as it can produce a better chip and a cleaner surface finish than a very soft annealed product. If you are making springs or clips, you must order material that has been cold-worked to a specific high-strength temper. A client in the electronics industry who manufactures EMI shielding clips orders 3/4 hard 304 strips from us. The material must be strong enough to provide good clamping force but have just enough residual ductility to be formed into the clip shape without cracking.
Collaborating with your supplier is key. At MFY, we don't just take orders; we review them. We ask our clients about their application and their fabrication processes. This dialogue allows us to ensure they are ordering the optimal material for their job. This collaborative approach to specification is the ultimate best practice; it aligns the material's properties with the manufacturing process and the final product's performance requirements, ensuring success from start to finish.
304L prevents weld sensitizationПравда
304L's low carbon content (≤0.03%) minimizes chromium carbide formation during welding, preserving corrosion resistance in heat-affected zones.
304 can be quench-hardenedЛожь
Unlike some steels, 304 stainless cannot be hardened through heat treatment; its strength increases only through cold working (work hardening).
Заключение
Ultimately, 304 stainless steel's strength cannot be enhanced by heat treatment due to its stable austenitic structure. Instead, its hardness is effectively increased through cold working. Understanding this, and applying best practices like using 304L for welding, is key to its successful application.
-
Learn how strain hardening effectively increases the strength of 304 stainless steel ↩
-
Find out how 304L reduces the risk of sensitization in welded structures ↩
-
Learn about diverse industrial applications of 304 stainless steel beyond general-purpose uses. ↩
-
Discover the benefits of 17-4 PH stainless steel, including higher yield strength. ↩
-
Understand 304 stainless steel applications in industry for better design strategies ↩
У вас есть вопросы или нужна дополнительная информация?
Свяжитесь с нами, чтобы получить индивидуальную помощь и квалифицированный совет.