What is the difference between stainless steel sheet and coil?
Are you struggling to decide between stainless steel sheets and coils for your production line? This critical choice directly impacts your operational efficiency, material costs, and final product quality. Making the wrong decision can lead to increased scrap, logistical challenges, and ultimately, a less competitive business.
The primary difference between stainless steel sheet and coil lies in their physical form. A coil is a long, continuous strip of steel wound into a roll, ideal for automated processes. A sheet is a piece of steel that has been cut from a coil to a specific, finite length.
This distinction may seem simple, but its implications for your manufacturing process, inventory management, and overall cost structure are vast. As someone who has guided numerous clients through this decision at MFY, I’ve seen how a well-informed choice can transform a production line. Let’s explore these differences so you can make the best decision for your business.
The choice between sheet and coil is a pivotal one for any business in the manufacturing, construction, or distribution sectors. It’s far more than a simple procurement detail; it's a strategic decision that reverberates throughout your entire supply chain. At MFY, we frequently consult with clients looking to scale their operations. I recall a growing equipment manufacturer in India that initially relied on sheets for their simplicity. However, as their volume increased, they faced production bottlenecks from handling individual pieces. After analyzing their workflow, we helped them transition to coils and invest in basic decoiling equipment. The result was a shift to continuous production, a significant reduction in scrap material, and a lower cost per unit. This illustrates that the decision requires a dialectical view, balancing upfront capital investment against long-term operational savings and efficiency gains.
What are the fundamental differences between stainless steel sheet and coil?
Struggling to see past the obvious shape difference between stainless steel sheet and coil? This surface-level view can lead to expensive procurement errors and inefficient production planning. Without a firm grasp of the fundamental distinctions, you risk overpaying or choosing a format that handicaps your operational workflow.
Fundamentally, a stainless steel coil is a continuous roll of metal, offering maximum material for high-volume, automated manufacturing. In contrast, a stainless steel sheet is pre-cut from a coil to a standard or custom length, providing convenience and precision for smaller-scale or project-based work.
This core difference branches out into critical considerations for any procurement manager or engineer. The choice is not arbitrary but a calculated one based on production scale, available machinery, and specific project demands. A coil provides unmatched efficiency for processes like roll-forming or progressive stamping, where a continuous feed minimizes downtime and material handling. For a large-scale tube manufacturer in our Russian market, using individual sheets would be unthinkable due to the constant reloading and resulting scrap. Conversely, a custom fabrication shop in the Middle East building bespoke kitchen backsplashes finds sheets far more practical. They can order the exact dimensions needed without investing in the heavy-duty decoiling and cutting machinery that would sit idle most of the time. My experience has consistently shown that the "best" format is entirely contextual. It's a strategic conversation we have daily at MFY with clients, from massive distributors to specialized contractors, to align their material form with their business model.
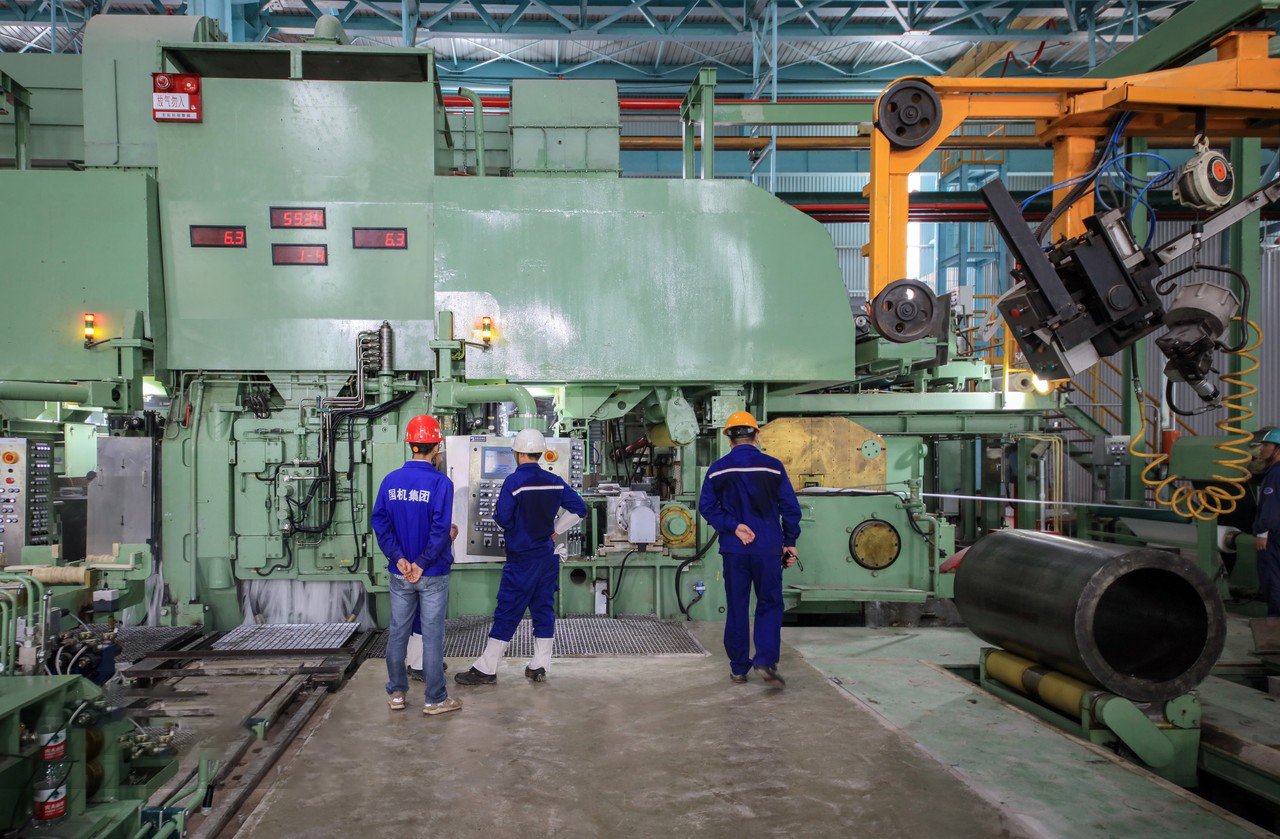
The decision between coil and sheet is one of the most fundamental in steel procurement, impacting everything from cost to final product quality. To make an informed choice, it's essential to analyze the differences through three critical lenses: their physical form and dimensions, their processing and edge condition, and their inherent cost structure and impact on inventory. Each aspect presents trade-offs that can either streamline your operations or create unforeseen bottlenecks. As we delve deeper, I'll share insights from my years in the industry, helping you see how these factors play out in real-world manufacturing and construction scenarios. This is about moving beyond a simple definition to a strategic understanding of the material you are sourcing.
Form Factor and Dimensional Constraints
The most apparent difference is the form factor. A stainless steel coil is a continuous product, with its length limited only by the weight the handling equipment and the customer's uncoiling machinery can manage. Standard coil weights can range from 3 to 10 metric tons or more. While the length is variable, the width is typically standardized by the rolling mill, with common widths including 1000mm, 1219mm (4 feet), and 1500mm. This continuous nature is the source of its efficiency in automated production, allowing for long, uninterrupted runs.
In contrast, a stainless steel sheet is a discrete, finite product. It is created by unrolling a coil and cutting it to specific lengths, a process known as cut-to-length (CTL). This results in standard-sized sheets, such as 4' x 8' or 5' x 10', or custom dimensions specified by the client. I remember working with a construction contractor in Southeast Asia on a major architectural facade project. They required thousands of panels of a non-standard size. By ordering custom-cut sheets directly from our MFY service center, they eliminated the need for on-site cutting, which saved them hundreds of labor hours and dramatically reduced material waste. This convenience is the primary advantage of sheets.
Between these two primary forms exists the "slit coil." This is a master coil that has been cut longitudinally into several narrower coils. For instance, a 1219mm wide master coil can be slit into three 406mm wide coils. This intermediate product offers a degree of customization in width while retaining the continuous form factor of a coil. This is a crucial value-added service MFY provides for clients like tube manufacturers or stamping companies who need specific widths for their tooling but still want the benefits of a continuous feed.
Processing and Edge Condition
The journey from raw material to usable product also dictates the condition of the material's edges. Coils typically come with what is known as a "mill edge." This is the natural edge resulting from the hot or cold rolling process and can be somewhat rougher and less dimensionally precise. For many applications, such as roll-forming or where the edge will be subsequently trimmed or hidden, a mill edge is perfectly acceptable and more cost-effective.
Sheets, on the other hand, undergo additional processing. As the coil is uncoiled and cut, the sides are often trimmed by rotary knives in a process called slitting. This produces a "slit edge" or "sheared edge," which is much more precise, smooth, and square. A client of ours who manufactures high-end commercial kitchen equipment relies exclusively on our sheets with a slit edge. For them, the clean, consistent edge is critical for both the final product's aesthetics and for ensuring perfect welds and fits during assembly, saving them valuable time in post-processing.
This additional processing—uncoiling, leveling to ensure flatness, and shearing to size—is what transforms a coil into a sheet. It's a value-added service that adds to the material's cost but delivers a product that is flat, dimensionally accurate, and ready for immediate use in many applications. At MFY, our integrated supply chain means we control these processes meticulously, ensuring the flatness and edge quality meet the stringent requirements of our diverse clients.
Cost Structure and Inventory Implications
From a purely financial perspective, stainless steel coils generally have a lower cost per kilogram than sheets. This is because they involve fewer processing steps at the mill or service center. The buyer essentially purchases the raw, continuous material and assumes the responsibility—and cost—of the equipment, labor, and scrap associated with processing it into final parts. This is an economical choice for high-volume users who can justify the capital investment in decoiling and cutting lines.
Sheets, due to the additional labor, machine time, and scrap generated during the cut-to-length process, have a higher cost per kilogram. However, this higher price includes the value of convenience and reduced capital expenditure for the buyer. For a small to medium-sized enterprise (SME) or a company handling custom, low-volume projects, buying sheets is almost always more cost-effective than investing in expensive processing machinery that would be underutilized.
The choice also significantly impacts inventory strategy. A distributor can hold a few master coils of common grades and thicknesses and cut them to various sheet sizes on demand, offering great flexibility and minimizing the risk of dead stock. Conversely, stocking pre-cut sheets requires more warehouse space to accommodate different dimensions and carries the risk that certain sizes may become obsolete if market demand shifts. We often advise our distributor clients to maintain a hybrid inventory—stocking high-turnover standard sheet sizes while using our coil processing services for custom orders.
Характеристика | Рулон нержавеющей стали | Лист из нержавеющей стали |
---|---|---|
Form | Continuous roll | Discrete, flat piece |
Cost per Kg | Нижний | Выше |
Processing | Requires buyer's decoiling & cutting equipment | Pre-cut, processed, and ready for many applications |
Лучшее для | High-volume, automated production (e.g., stamping) | Low-volume, custom projects, or no processing equipment |
Scrap Rate | Potentially lower with optimized nesting/cutting | Can be higher from off-cuts of standard sizes |
Обработка | Requires heavy equipment (cranes, coil cars) | Easier to handle with standard forklifts |
Coils are continuous rollsПравда
Stainless steel coils are indeed long, continuous strips wound into rolls, making them ideal for automated manufacturing processes.
Sheets require no processingЛожь
Sheets undergo significant processing including uncoiling, leveling and shearing before they're ready for use, which contributes to their higher cost.
How does the manufacturing process vary between stainless steel sheet and coil?
Have you ever pictured the journey from a massive, glowing slab of steel to the precise, finished material that arrives at your facility? This manufacturing path can seem like a black box. Not understanding this process means you can't fully appreciate the factors that dictate your material's quality, consistency, and lead time, leaving you less informed when making critical procurement decisions. I'll illuminate the manufacturing journey, pinpointing the exact stages where the paths for coil and sheet diverge, giving you a powerful understanding of the product you are sourcing.
The manufacturing process for both begins identically: hot-rolling a slab into a long strip, which is then coiled. The divergence occurs after the final cold-rolling and finishing. To produce a finished coil, the process ends there. To create sheets, the coil undergoes additional steps: decoiling, leveling, and cutting-to-length.
This critical divergence point is where much of the final value—and cost—is added to the product. While the initial creation of the master coil is a feat of large-scale metallurgy, the subsequent steps are what customize the material for its specific end-use. At MFY, our fully integrated facilities allow us to manage this entire journey from start to finish. I've walked our production floors countless times, from the immense pressure of the cold-rolling mills to the precise, swift action of the shear that cuts a final sheet. This firsthand perspective is vital when explaining to a client, for instance, why the lead time for custom-cut 316L sheets is longer than for a standard 304 coil. It's not merely a matter of cutting; it involves scheduling the entire cut-to-length line, calibrating the leveler for a specific thickness to ensure perfect flatness, and programming the shear for exact dimensions. This is a carefully orchestrated process, and understanding it is key to effective project planning and building a resilient supply chain.
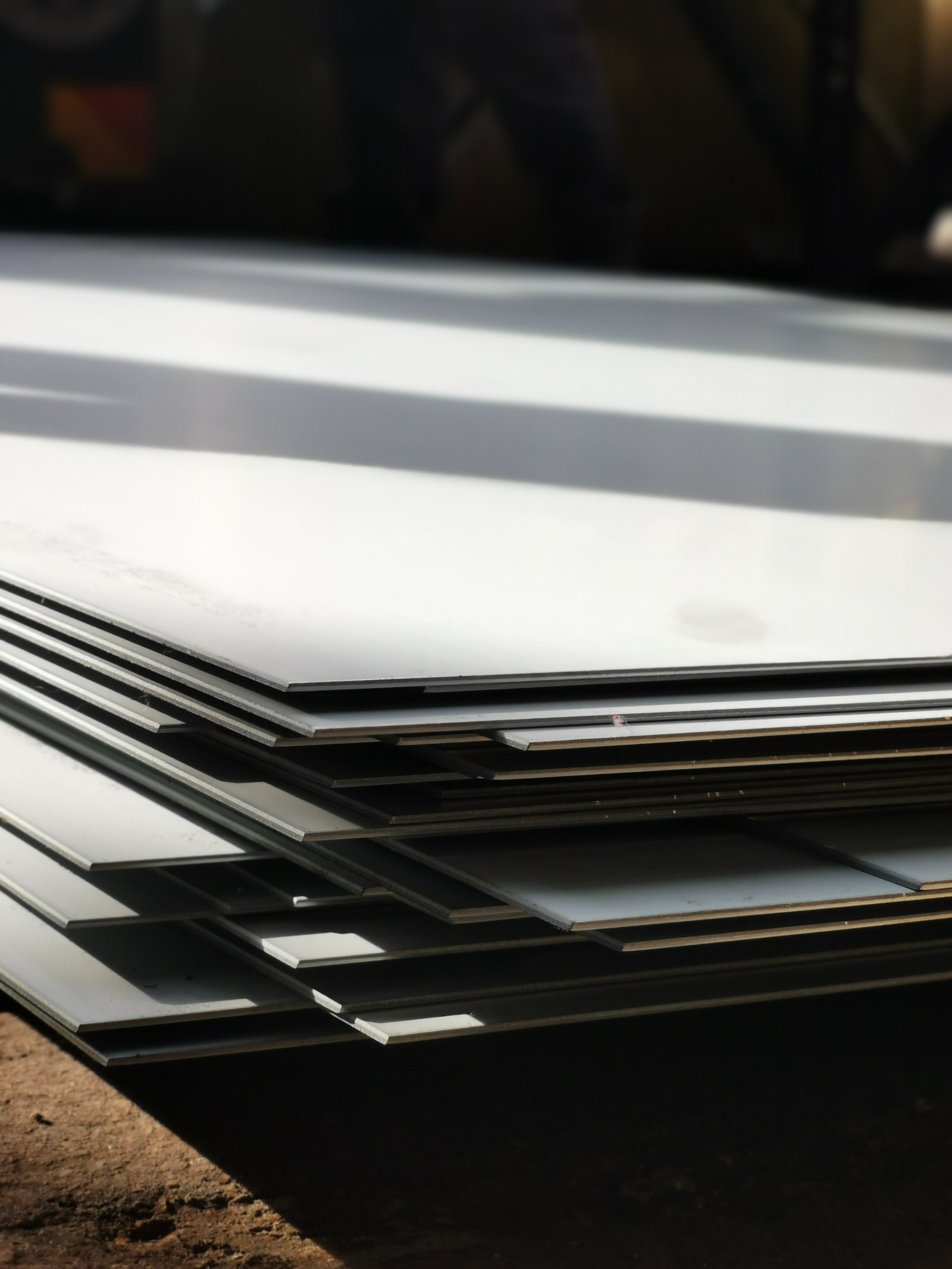
To truly appreciate the material you're working with, it's beneficial to understand its creation story. The manufacturing process of stainless steel is a blend of immense force and fine control. We will trace this path from its molten beginnings to the common foundation of a master coil. Then, we'll explore the two distinct finishing paths: one that concludes with a tightly wound coil ready for high-volume production, and the other that continues on to be transformed into flat, ready-to-use sheets. This journey reveals why quality control at each stage is paramount and how each step contributes to the final properties and cost of the material you receive.
From Slab to Master Coil: The Common Foundation
The journey for both sheet and coil begins in the same place: the melt shop. Here, raw materials like scrap steel and ferroalloys1 are melted in an Electric Arc Furnace (EAF). The molten steel is then refined in an Argon Oxygen Decarburization (AOD) vessel to precisely adjust the chemical composition, removing impurities and ensuring the correct percentages of chromium, nickel, and other elements. This chemistry is the DNA of the stainless steel, determining its grade and properties like corrosion resistance and strength. The molten steel is then cast into thick, rectangular slabs.
These slabs are then reheated to over 1,100°C and sent to the hot-rolling mill. Here, the glowing slab is passed through a series of massive rollers, which progressively squeeze it thinner and longer, transforming it into a long strip of steel that is several hundred meters long. At the end of the hot-rolling line, this strip is coiled up, forming what is known as a "hot-rolled coil" or "black coil." It has a dark, scaled surface and is the raw feedstock for all further flat-rolled products.
To prepare it for further processing, this hot-rolled coil must undergo annealing and pickling. It is first uncoiled and passed through a continuous annealing furnace, which heats the steel to soften it and refine its grain structure. Immediately after, it passes through a series of acid baths in a process called pickling, which chemically removes the black oxide scale from the surface. The result is a clean, matte-grey surface. This combined process, often performed on a HAP (Hot Annealing and Pickling) line, is critical for ensuring the material's final corrosion resistance and preparing it for the next stage.
The Cold-Rolling and Finishing Path for Coils
The next critical phase is cold rolling. The cleaned, hot-rolled coil is processed at room temperature through a series of rollers under immense pressure. This process reduces the steel's thickness to its final specified gauge with very high precision. Cold rolling also significantly changes the material's properties: it work-hardens the steel, increasing its tensile strength and hardness, and it produces a much smoother, more reflective surface. For instance, cold rolling can increase the tensile strength of a 304-grade stainless steel from around 515 MPa to over 800 MPa.
After cold rolling, the steel is hard and less ductile, so it usually undergoes a final annealing process to restore its formability. Following this, it may be given a light "skin pass" or "temper pass" through rollers to improve flatness, prevent stretcher strains from forming during subsequent customer processing, and impart the final surface finish. This is the stage where well-known finishes like the standard dull 2B finish or the bright, reflective BA (Bright Annealed) finish are created.
At this point, the product destined to be sold as a coil reaches the end of its manufacturing journey. The continuous strip is trimmed to its final specified width, carefully rewound onto a mandrel with consistent tension to prevent collapsing, and securely packaged for shipment. For our export clients at MFY, the quality of this final winding and packaging is paramount. We learned early on that improper tensioning could lead to coil breaks and edge damage during long sea voyages, so our quality control at this stage is exceptionally strict to ensure the material arrives at our client's facility in perfect condition.
The Divergent Path: Creating Sheets from Coils
For stainless steel sheets, the journey continues where the coil's journey ends. A finished coil is transported from the mill to a processing facility or service center, which houses a cut-to-length (CTL) line. The first step on this line is mounting the coil onto an uncoiler or decoiler, which carefully unwinds the steel strip under controlled tension.
The unwound strip then immediately passes through a leveler. This essential piece of equipment consists of a series of staggered rollers that bend the material back and forth. This action removes "coil set"—the natural tendency of the steel to want to stay curved—and relieves internal stresses, ensuring the final product is exceptionally flat. The degree of flatness is a critical quality parameter, especially for architectural panels, appliance casings, and high-end tabletops. I recall a client manufacturing commercial freezers who was experiencing issues with their door panels warping after assembly. We traced the problem to insufficient leveling. By adjusting the settings on our CTL line, we were able to deliver sheets with superior flatness, which completely resolved their production issue.
The final step is shearing. Once the strip is flat, it moves along a conveyor to a high-speed shear. This powerful guillotine is programmed to cut the strip into precise, predetermined lengths. The freshly cut sheets are then automatically stacked, often with a layer of paper or PVC film interleaved to protect the surface finish. Finally, the stack is placed on a pallet, securely strapped, and wrapped for transport. This entire sequence—decoiling, leveling, shearing, and packaging—is the value-added process that transforms a bulk industrial coil into a convenient, ready-to-use sheet.
Process Stage | Coil Production Path | Sheet Production Path |
---|---|---|
1. Melting & Casting | Common foundation for both products | Common foundation for both products |
2. Hot Rolling | Common foundation for both products | Common foundation for both products |
3. Anneal & Pickle | Common foundation for both products | Common foundation for both products |
4. Cold Rolling | Final thickness-reduction step | Intermediate step before cutting |
5. Finishing | Final surface finish applied (e.g., 2B, BA), then recoiled | Final surface finish applied to the entire coil |
6. Decoiling & Leveling | N/A - Shipped as a coil | Key divergent step: Coil is unwound and made flat |
7. Cutting to Length | N/A - Shipped as a continuous strip | Key divergent step: Leveled strip is cut into sheets |
8. Packaging | Packaged as a single, heavy industrial coil | Packaged as stacked sheets on a pallet, often with PVC film |
Coils and sheets share initial manufacturing stepsПравда
Both stainless steel coils and sheets begin with identical processes: melting, casting, hot rolling, and annealing/pickling before diverging at the cold-rolling stage.
Cold rolling increases steel hardnessЛожь
Cold rolling actually work-hardens stainless steel, significantly increasing its tensile strength and hardness while reducing ductility, requiring subsequent annealing to restore formability.
What are the distinct applications for stainless steel sheets versus coils?
Are you choosing your steel format based on habit rather than application? Using sheets where a coil would be more efficient, or vice-versa, can inflate production time and costs. This mismatch between material form and end-use leads to unnecessary waste, process bottlenecks, and missed opportunities for optimization, directly impacting your competitiveness in the market. I will outline the specific applications where each format excels, providing clear examples from various industries. This will empower you to align your procurement strategy with your production needs, ensuring you use the most effective and economical format for every job.
Stainless steel coils are predominantly used in high-volume, automated manufacturing processes like automotive component stamping, tube and pipe production, and appliance manufacturing. Sheets are favored for custom fabrication, architectural work, construction, and lower-volume production where specific dimensions and ease of handling are paramount.
The choice is driven by the logic of the manufacturing process itself. Think of a major automotive supplier. They need to produce tens of thousands of identical brackets or exhaust components. Feeding a continuous coil into an automated stamping press allows for uninterrupted production at high speed, maximizing output and minimizing labor. It would be incredibly inefficient for them to load individual sheets for each part. On the other hand, consider a company specializing in bespoke stainless steel range hoods for luxury homes. Each project is unique. Ordering pre-cut sheets to the exact size they need simplifies their workflow, eliminates the need for expensive cutting equipment, and minimizes scrap from a one-off job. As Global Business Director at MFY, I’ve worked with both types of clients, from massive tube mills in Russia to boutique architectural firms in the Middle East. The common thread for success is always the same: a deep understanding of how the material form integrates with their specific application and operational scale.
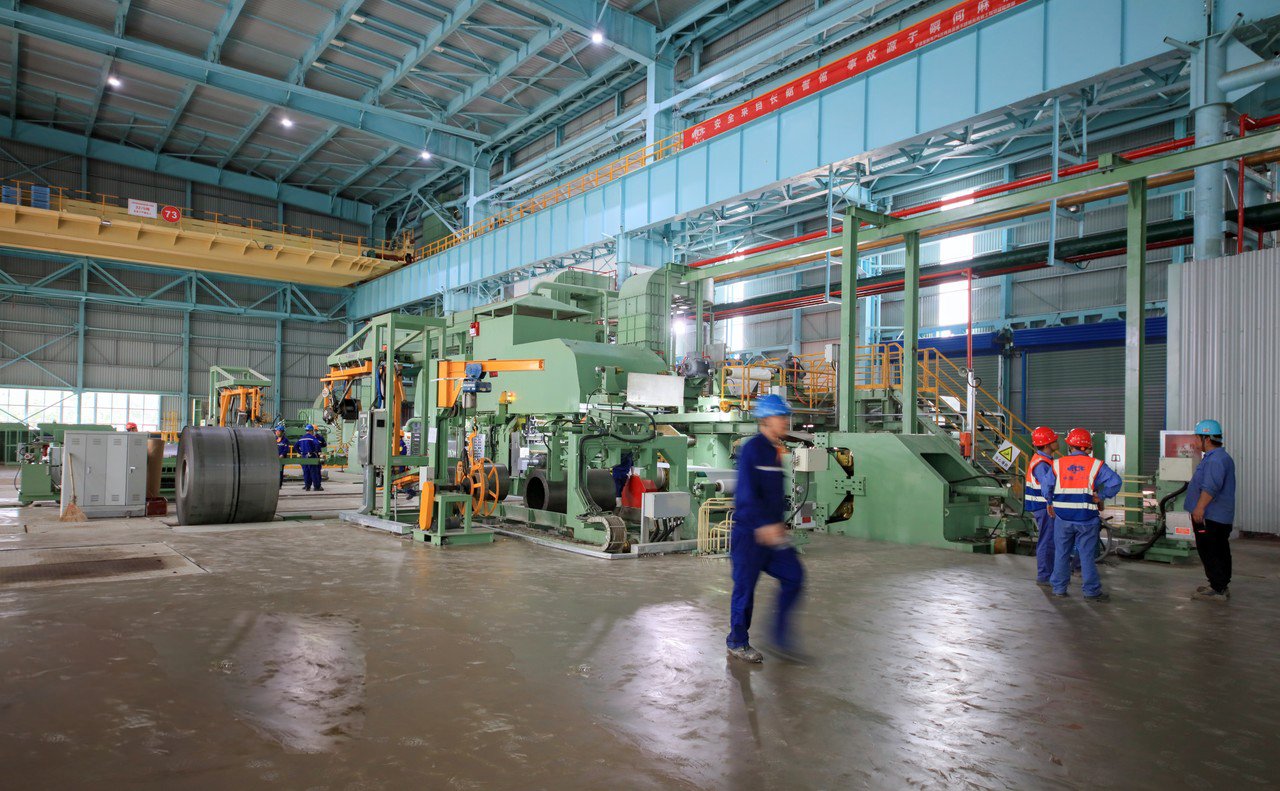
The "best" format is defined by the job it needs to do. An application-driven approach to selecting between stainless steel sheet and coil is fundamental to achieving operational excellence. We will explore the world of high-volume manufacturing, where the continuous nature of coils is indispensable. Then, we will shift our focus to the domains of precision and customization2, where the convenience and ready-to-use nature of sheets make them the superior choice. Finally, through specific industry case studies, we’ll see how these principles apply in the real world, providing a practical framework for your own decision-making process.
High-Volume Manufacturing: The Realm of Coils
Stainless steel coils are the lifeblood of industries built on scale and automation. Their continuous form is perfectly suited for processes that run for hours or even days with minimal interruption. The automotive industry is a prime example. Stamping plants feed coils of specific grades and widths directly into massive progressive stamping dies that can produce thousands of parts per hour, from small brackets to larger body panel reinforcements. The ability to avoid constantly loading new material is a massive driver of efficiency.
Similarly, the tube and pipe manufacturing industry is almost exclusively dependent on coils. In a tube mill, a coil is unrolled and fed continuously through a series of rollers that gradually form it into a circular shape before the seam is welded shut. The length of the final pipes is limited only by handling and transport logistics, not by the input material. I've visited MFY clients in India whose entire business model is built around the high-speed conversion of our stainless steel coils into pipes for the construction and water treatment industries. For them, a coil is not just a material; it's the raw fuel for their continuous production engine.
The appliance manufacturing sector also heavily relies on coils for producing components like washing machine drums, refrigerator casings, and dishwasher interiors. Automated lines uncoil, stamp, bend, and assemble these parts with remarkable speed. According to industry reports, leveraging coil-fed production can reduce material handling costs by up to 30% compared to using sheets in high-volume settings. This efficiency is critical in a competitive market where every cent per unit matters.
Precision and Customization: Where Sheets Shine
While coils dominate in scale, stainless steel sheets excel in applications requiring flexibility, customization, and precision on a smaller scale. The world of architectural metalwork and construction is a key domain for sheets. When creating decorative facades, custom cladding, or intricate interior elements, fabricators work with unique, project-specific dimensions. Ordering pre-cut or standard-sized sheets allows them to get exactly the material they need without investing in a full decoiling line.
Custom fabrication shops are another prime user of sheets. These businesses build everything from commercial kitchen equipment and food service counters to bespoke furniture and sculptures. Each job is different. A fabricator building a single, large stainless steel countertop for a restaurant needs a perfectly flat, blemish-free piece of a specific size. A standard 4' x 10' sheet with a protective PVC film is the ideal starting point. It's easy to handle with a forklift, can be moved around the workshop, and requires only final cutting and finishing. Using a coil for such a one-off project would be impractical and uneconomical.
Even in some areas of equipment manufacturing, sheets are preferred. For example, when building complex machinery with many different-sized panels and brackets in low volumes, it's often more efficient to work from a bill of materials that specifies various sheet sizes. A client of ours who builds specialized processing equipment for the pharmaceutical industry uses sheets exclusively. The high value of their final product and the need for pristine, traceable materials make the convenience and quality control of pre-cut sheets a worthwhile investment over the raw efficiency of coils.
Industry-Specific Choices: A Comparative Look
Let's compare two common applications to see this logic in action. First, consider the production of HVAC ductwork. For large commercial projects, ducting is often fabricated on-site or in large workshops using coil-fed machines. A roll-forming machine takes a slit coil and continuously forms it into rectangular or spiral ducting, cutting it to length as needed. This is a high-volume, standardized process where coils are the clear winner. However, for a small residential job or a complex fitting, a technician might use a standard sheet of stainless steel and a hand brake to form the required piece.
Now, let's look at the food and beverage industry. A massive brewery building large fermentation tanks would likely use large plates or sheets, as the tank's structural integrity and weld quality are paramount, and the curvature is created through plate rolling, a process suited to discrete pieces. In contrast, the same company might use stainless steel coil to manufacture the miles of piping needed to transport liquids throughout the facility. In the same plant, the commercial kitchen that serves its employees would be outfitted with counters, backsplashes, and equipment all made from sheets, prized for their aesthetic finish and ease of custom fabrication.
This demonstrates that even within a single industry, the choice between sheet and coil is not absolute. It is a nuanced decision based on the specific part being made, the volume required, and the manufacturing technology available.
Application Category | Primary Format | Key Industries | Rationale |
---|---|---|---|
High-Volume/Automated | Coil | Automotive, Tube & Pipe, Appliance Manufacturing | Continuous feed maximizes uptime and production speed. |
Custom/Low-Volume | Sheet | Custom Fabrication, Architectural Metalwork, Job Shops | Convenience, specific sizes, and no need for heavy equipment. |
Construction | Both | Structural (Sheet/Plate), Ductwork (Coil) | Choice depends on the component and scale of production. |
Equipment/Machinery | Both | Casings (Coil), Custom Panels (Sheet) | Depends on production volume and part standardization. |
Coils suit high-volume productionПравда
Stainless steel coils are ideal for automated processes like automotive stamping where continuous material feed maximizes efficiency.
Sheets are only for small projectsЛожь
Sheets are used in large-scale applications too, like construction of fermentation tanks where structural integrity is critical.
How do the storage and transportation requirements differ for stainless steel sheet and coil?
Do you consider the logistical impact when ordering your stainless steel? The physical form of sheet versus coil dictates entirely different requirements for handling, storage, and transport. Overlooking these differences can lead to damaged material, inefficient use of warehouse space, and even safety hazards, creating unexpected costs and delays that disrupt your operations. I will detail the distinct logistical needs for each format, from the equipment required for handling to best practices for storage and protection. This will help you prepare your facility and team, ensuring you can manage your steel inventory safely and efficiently from the moment it arrives.
The logistics for stainless steel coils and sheets differ dramatically. Coils are heavy, dense, and require specialized equipment like cranes or C-hooks for handling, and secure cradles for transport. Sheets are palletized, easier to handle with standard forklifts, but consume more warehouse floor space for the same weight.
This is a practical reality I discuss with new clients every day. A business accustomed to receiving pallets of sheets can be caught completely off guard by the arrival of a 20-ton truck carrying three massive coils. They may lack the overhead crane to unload it or the designated, reinforced floor space to store it safely. A coil stored improperly on a flat floor can become a dangerous rolling hazard. Conversely, a company that transitions from coils to sheets to support a new, custom-product line might underestimate the sheer footprint required to store dozens of pallets of different sizes. At MFY, our logistics team works closely with clients to ensure they understand these requirements до the material ships, preventing costly surprises. This foresight is a key part of our service, especially for clients in our export markets who face long transit times.
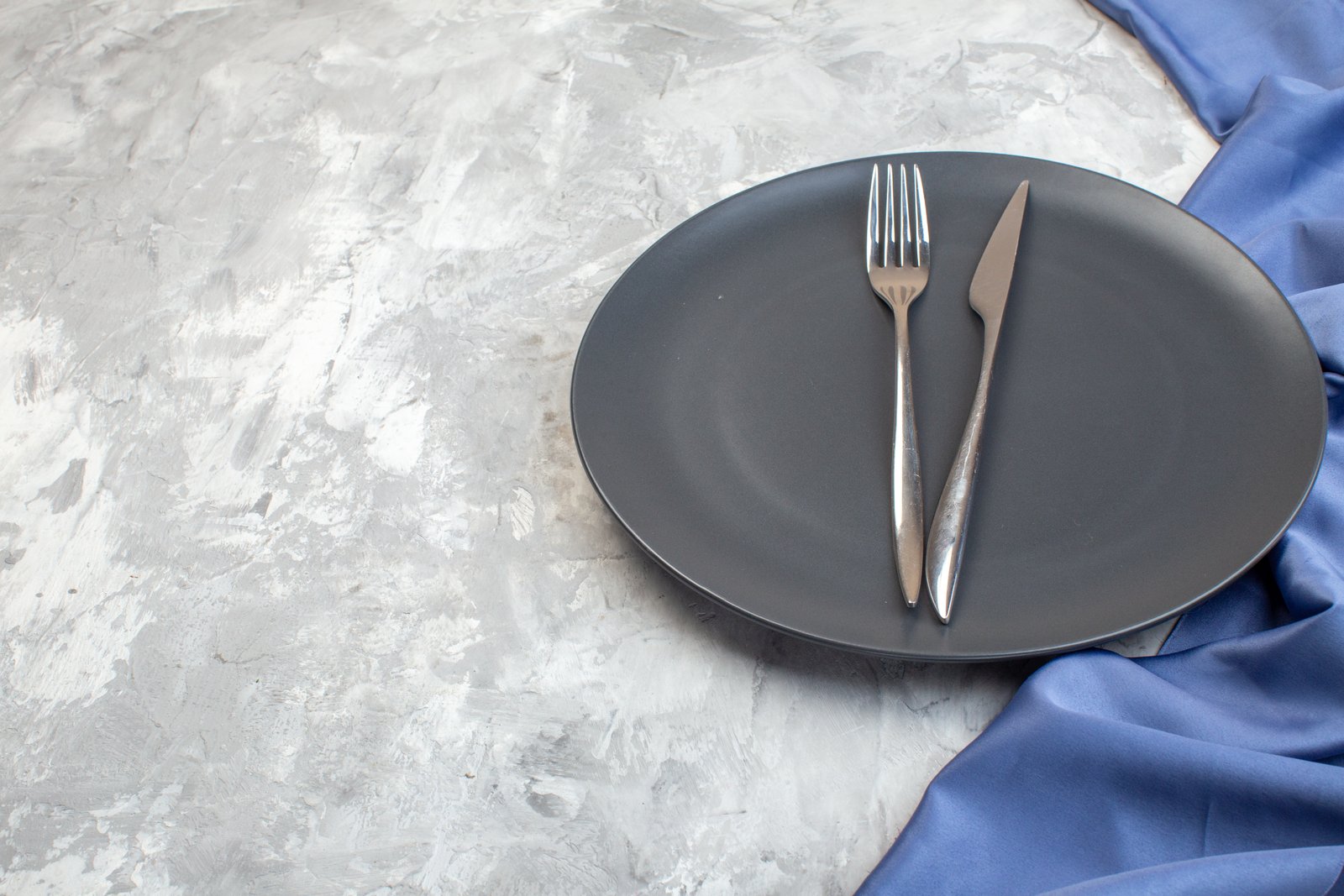
The journey of your stainless steel doesn't end when the manufacturing is complete; it continues all the way to your factory floor. The logistics of handling, storing, and transporting the material are just as critical as its metallurgical properties. We will first examine the specific challenges and requirements associated with managing heavy, dense coils3, a game of heavy lifting and specialized equipment. Next, we will explore the world of sheet management, a matter of optimizing space and ensuring accessibility. Finally, we’ll discuss the crucial role of packaging and protection in mitigating the risks that both formats face during transit, drawing on real-world lessons to protect your investment.
The Logistics of Coils: Heavy Lifting and Specialized Handling
Transporting and storing stainless steel coils is a specialized task defined by their immense weight and concentrated mass. A single coil can weigh anywhere from 3 to over 20 metric tons. Unloading a coil from a flatbed truck or shipping container cannot be done with a standard forklift. It requires either a high-capacity overhead crane equipped with a C-hook or a specialized forklift4 with a boom attachment designed to pass through the coil's "eye" (the center hole). This specialized equipment represents a significant capital investment and requires trained operators.
Once unloaded, storage presents another set of challenges. Coils must never be stored on their round side on a flat floor, as they can easily roll, creating a severe safety hazard. They should be stored in designated areas, either in sturdy steel cradles or on reinforced concrete floors with built-in V-shaped grooves that prevent movement. Coils can be stored with their eye to the sky (vertically) or eye to the side (horizontally). "Eye to the sky" storage is more space-efficient but increases the risk of moisture collecting in the wraps, which can lead to crevice corrosion, especially in humid climates like those in much of Southeast Asia.
I learned a valuable lesson about this early in my career. We shipped several coils to a client in a coastal region. They were stored eye-to-the-sky outdoors under a tarp. Condensation formed between the wraps, and by the time they were uncoiled weeks later, the surface was stained. Now, we always advise clients in humid environments to store coils eye-to-the-side in a dry, climate-controlled warehouse to allow for air circulation and prevent moisture entrapment.
Sheet Management: Space, Stacking, and Accessibility
Stainless steel sheets, in contrast, are far easier to handle. They arrive neatly stacked on wooden or steel pallets and can be easily unloaded and moved with a standard forklift. This accessibility is a major logistical advantage for smaller companies or facilities without heavy crane capacity. The primary challenge with sheets is not handling, but space management.
While a single pallet of sheets is manageable, storing a large inventory of various grades, thicknesses, and dimensions can consume a vast amount of floor space. Unlike coils, which store a large amount of material in a dense footprint, sheets spread that same weight over a much larger area. For a distributor or a large fabricator, this necessitates a well-organized warehouse with robust racking systems to take advantage of vertical space. Cantilever racks are often used for storing pallets of sheets, allowing for easy access to any specific pallet without having to move others.
Proper stacking is also crucial. Heavy-gauge sheets should always be at the bottom of a stack to prevent thinner, more delicate sheets from being damaged. Interleaving paper or PVC film between sheets is standard practice to protect the surface finish from scratches during handling and storage. We work with our clients to develop smart inventory systems, ensuring that the most frequently used sheet sizes are the most accessible, minimizing handling time and the risk of damage to other stock.
Packaging and Protection: Mitigating Risks in Transit
The final logistical consideration is packaging, which is the first line of defense against damage during transportation. Coils are typically wrapped in layers of water-resistant paper and then encased in a protective layer of steel or durable plastic sheeting. They are securely strapped with steel bands to prevent the coil from unwinding. The eye of the coil is often protected with plastic or metal rings. This robust packaging is essential to protect against moisture, salt spray during ocean freight, and physical damage from shifting during transit.
Sheets require a different but equally important packaging strategy. They are stacked on a sturdy pallet, often with a moisture barrier sheet on the bottom. The entire stack is then wrapped and securely strapped to the pallet. For high-value finishes, such as a No. 8 mirror or a patterned surface, a protective PVC film is applied to each individual sheet. This film guards against scratches and scuffs during handling and fabrication and is peeled off only after the final product is assembled.
We had a case with an equipment integrator where a shipment of sheets arrived with edge damage because the pallet had shifted and hit the side of the container. After that incident, we reinforced our standard operating procedure to include corner protectors and additional bracing for all palletized sheet exports. It's a small detail, but it ensures that the millions of dollars worth of material MFY ships globally arrives in the pristine condition our clients expect.
Logistical Aspect | Рулон нержавеющей стали | Лист из нержавеющей стали |
---|---|---|
Погрузочно-разгрузочное оборудование | Overhead crane with C-hook; high-capacity coil forklift | Standard forklift |
Storage Method | In cradles or V-grooves; eye-to-sky or eye-to-side | Stacked on pallets, often in cantilever racking |
Space Efficiency | High (dense mass in a small footprint) | Low (consumes significant floor space) |
Safety Concern | Rolling hazard if not secured properly | Safe when properly stacked and stored on racks |
Packaging | Wrapped in paper/plastic, steel-banded | Stacked on pallet, strapped, often with interleaved paper/PVC |
Accessibility | Requires heavy equipment to move and access | Easy access to individual pallets with a forklift |
Coils require specialized handling equipmentПравда
Stainless steel coils need cranes with C-hooks or specialized forklifts due to their heavy weight and dense mass.
Sheets can be stored without palletsЛожь
Sheets must be stacked on pallets for proper handling and storage to prevent damage and ensure safety.
What recommendations can be made for choosing between stainless steel sheet and coil?
Are you confident your choice between sheet and coil is truly optimizing your business? Selecting the wrong format based on incomplete analysis can lock you into an inefficient production model. This leads to higher per-unit costs, unnecessary capital expenditure, or logistical burdens that could have been avoided, ultimately eroding your competitive advantage. I will provide a clear, strategic framework for making this critical decision. By evaluating your production volume, material needs, and total costs, you can confidently choose the format that best aligns with your business goals and operational capabilities.
The recommendation hinges on a holistic analysis of your operations. Choose stainless steel coils if you have high-volume, automated production and the capital for handling equipment. Opt for stainless steel sheets for lower-volume, custom work, or if you want to avoid investment in processing machinery and prioritize convenience.
This is the core of the consultation I provide to MFY clients. It’s not about pushing one product over another; it’s about finding the right fit. I recently worked with a mid-sized engineering contractor who was considering investing in a decoiling line. They believed it would lower their material costs. However, after we analyzed their project data together, we found that their job sizes were highly variable and often required different grades of steel. The downtime from changing coils and the cost of holding multiple coil inventories would have outweighed the per-kilogram savings. We concluded that continuing to source pre-cut sheets from our service center was the more profitable and flexible strategy for their business model. This kind of analysis, looking beyond the sticker price to the total cost of ownership, is essential.
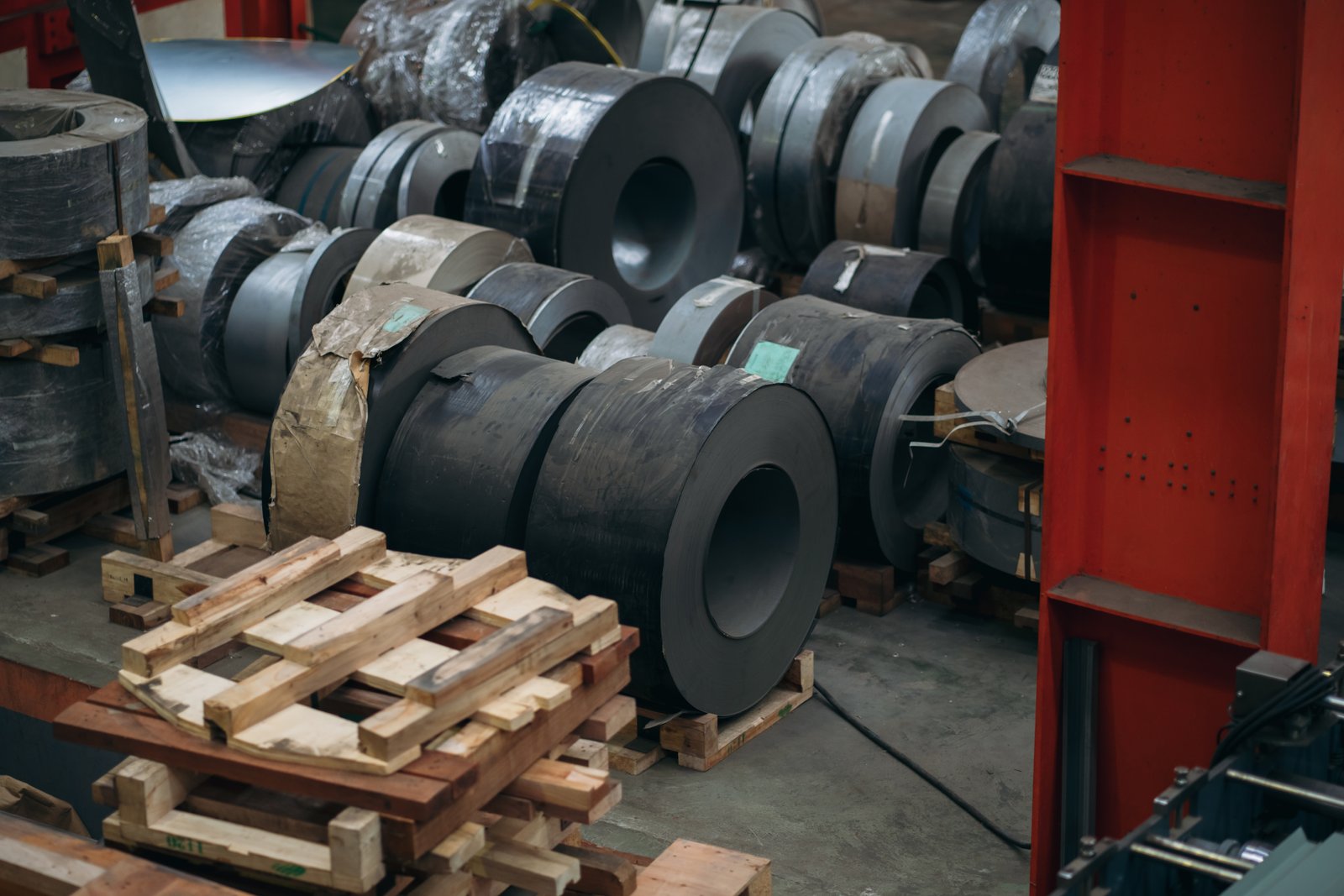
Making the right choice between stainless steel sheet and coil is a strategic business decision, not just a technical one. It requires a thoughtful evaluation of your company's unique circumstances. To guide you through this process, we will focus on three essential pillars of analysis. First, we’ll assess your production volume and in-house capabilities to see if you can leverage the efficiencies of coils. Second, we will analyze your specific material requirements to determine if the flexibility of sheets is a better fit. Finally, we’ll conduct a strategic cost-benefit analysis that looks beyond the initial price to uncover the true, total cost associated with each option.
Assessing Your Production Volume and Capabilities
The first and most important question to ask is: what is my production volume? If your business involves long, continuous runs of the same product, the argument for coils becomes very strong. A high-volume operation can amortize the significant capital investment in decoiling, leveling, and handling equipment (like overhead cranes) over thousands of tons of steel, making the lower per-kilogram cost of coils highly advantageous. If you are a tube mill, an automotive stamper, or a large appliance manufacturer, your business model is likely already built around the efficiency of a coil-fed process.
Conversely, if your production is characterized by short runs, frequent changeovers between different material grades or thicknesses, or project-based work, sheets are almost always the more logical choice. The time and material wasted in changing a heavy coil for a small job would negate any cost savings. You must honestly assess your facility's capabilities. Do you have the physical space for a decoiling line? Do you have the capital for the equipment and the trained personnel to operate it safely and efficiently? If the answer to any of these is no, then the convenience and ready-to-use nature of sheets provide a much lower barrier to entry and a more flexible operational model.
A typical threshold we see in the industry is around 500-1000 tons per year of a specific grade and thickness. Below this volume, it becomes difficult to justify the investment in a dedicated decoiling line. However, this is just a rule of thumb, and a more detailed analysis is always required.
Analyzing Your Project's Material Requirements
Beyond pure volume, you must analyze the nature of the materials you use. Do your projects require a wide variety of stainless steel grades (e.g., 304, 316L, 430 stainless steel5), thicknesses, and finishes? If so, managing an inventory of coils for each variation can be a logistical and financial nightmare. Each coil represents a significant capital outlay tied up in inventory. It's often far more strategic to rely on a service center like MFY, which holds a massive master inventory of coils and can provide you with just-in-time delivery of the specific sheets you need for each job.
Consider the scrap rate. If your parts can be efficiently "nested" (arranged) on a wide coil to minimize waste, a coil might be more efficient. However, if you need many different, smaller rectangular parts, ordering them as custom-cut sheets might result in less overall scrap than cutting them yourself from a standard-sized coil or sheet. I worked with a client who manufactures electronic enclosures. They used to buy standard 4'x8' sheets and had a significant scrap rate. We helped them program their parts into our CTL software, and now they order a mix of custom-sized sheets that closely match their parts, which has reduced their material waste by over 15%.
Also, consider quality requirements. For applications demanding extreme flatness or perfect, blemish-free surfaces for aesthetic reasons, sourcing high-quality, PVC-protected sheets from a reputable service center is often the safest bet. You are leveraging the provider's specialized leveling equipment and clean-handling procedures without having to invest in them yourself.
A Strategic Cost-Benefit Analysis
Finally, the decision must be grounded in a comprehensive cost-benefit analysis that goes beyond the price per kilogram. For coils, the analysis must include the purchase price of the steel, plus the amortized cost of the decoiling equipment, maintenance, energy consumption, operator labor, and the cost of the scrap generated. This gives you a "true cost per part" from a coil.
For sheets, the calculation is the purchase price of the sheets plus the cost of handling and any scrap generated from cutting them to final size. While the initial purchase price is higher, the downstream costs are significantly lower. For many businesses, the total cost of ownership for sheets is lower, especially when you factor in the financial benefits of inventory flexibility and reduced capital expenditure.
A distributor client in the Middle East provides a perfect case study. They serve hundreds of small fabrication shops. They made the strategic decision not to invest in their own cut-to-length line. Instead, they leverage MFY's processing capabilities. They place large bulk orders for master coils, which we store for them. As they receive orders from their customers, they send us cutting instructions, and we deliver the required sheets directly to them or their clients. This "virtual processing" model allows them to offer a huge variety of sizes with zero capital investment in equipment and minimal inventory risk, a clear win-win strategy.
Фактор решения | Favorable for Stainless Steel Coil | Favorable for Stainless Steel Sheet |
---|---|---|
Production Volume | High; long, continuous runs of the same product. | Low to medium; short runs, job-shop environment. |
Equipment Capability | In-house decoiling, leveling lines, and heavy cranes are available. | No specialized processing equipment; standard forklifts available. |
Material Variety | Low; focus on a few standard grades and thicknesses. | High; frequent need for different grades, finishes, and sizes. |
Capital Investment | Willing to invest in processing machinery for long-term savings. | Prefer to minimize capital expenditure and operational complexity. |
Inventory Strategy | Can manage and afford to hold heavy coil inventory. | Prefer flexible, just-in-time inventory of various sizes. |
Total Cost Focus | Focused on lowest per-kg raw material cost. | Focused on lowest total cost of ownership per finished part. |
Coils suit high-volume productionПравда
Coils are cost-effective for continuous runs of the same product due to economies of scale.
Sheets always cost more than coilsЛожь
When factoring in equipment costs and scrap rates, sheets may have lower total ownership costs for certain operations.
Заключение
The choice between stainless steel sheet and coil is a strategic decision, not just a logistical one. It hinges on your production volume, equipment capabilities, and project-specific needs. By carefully aligning your material format with your operational strategy, you can unlock significant efficiencies and gain a competitive edge.
-
Discover how raw materials influence the properties of stainless steel. ↩
-
Discover the benefits of using sheets in precision-based industries ↩
-
Learn about the storage and safety issues when dealing with dense steel coils ↩
-
Discover the specialized forklifts necessary for safe coil handling ↩
-
Explore the varying properties and uses of different stainless steel grades ↩
У вас есть вопросы или нужна дополнительная информация?
Свяжитесь с нами, чтобы получить индивидуальную помощь и квалифицированный совет.