What's the 304 Stainless Steel Sheet?
Are you struggling to choose the right material for your project, worried that a wrong choice could lead to costly failures and delays? The world of stainless steel is vast, and picking an unsuitable grade can compromise your entire operation. At MFY, we believe understanding the fundamentals is key to success.
304 stainless steel sheet is an austenitic alloy renowned for its excellent corrosion resistance, formability, and versatility. Composed primarily of iron, chromium (18-20%), and nickel (8-10.5%), it is the most widely used stainless steel grade globally, offering a balanced combination of performance and cost-effectiveness.
Throughout my career as Global Business Director at MFY, I've seen firsthand how crucial material selection is. It's not just about technical specifications; it’s about aligning the material's properties with the specific demands of your industry and application. This decision can impact everything from your product's lifespan to your company's bottom line.
In this guide, I'll share my experiences and insights to demystify 304 stainless steel. We will move beyond the technical data sheets to explore its real-world applications, its distinct advantages over other grades, and the practical considerations for selecting the right sheet for your needs. We'll examine why this grade has become the "workhorse" of the industry and how you can leverage its strengths to build a more resilient and efficient supply chain for your business. Let's dive deeper into what makes 304 stainless steel the go-to choice for so many.
What are the key characteristics of 304 stainless steel sheets?
Feeling uncertain about whether a material can withstand your operational environment? This doubt can lead to over-engineering and unnecessary costs. The key is to select a material whose inherent characteristics perfectly match your application's demands, ensuring both longevity and budget efficiency.
The key characteristics of 304 stainless steel sheets are superior corrosion resistance in most environments, excellent formability and weldability, and a non-magnetic nature in its annealed state. Its hygienic properties and aesthetic appeal also make it a highly versatile and widely specified material.
When I work with clients, especially those in the manufacturing and engineering sectors, the conversation almost always starts with these fundamental properties. Understanding them isn't just an academic exercise; it's the foundation for making sound commercial and technical decisions. I recall a client in Southeast Asia, a burgeoning food and beverage manufacturer, who was on the verge of investing heavily in a more expensive grade. They were concerned about acidic food products and rigorous cleaning cycles. We sat down and walked through the specific chemical exposures and mechanical stresses involved in their process. By demonstrating the proven resilience of 304 stainless steel in similar applications—backed by years of industry data—we showed them that it was more than capable of meeting their needs. This not only saved them significant capital expenditure but also streamlined their supply chain, as 304 is more readily available. This experience solidified my belief that a deep, practical understanding of a material’s core traits empowers our clients to make smarter, more confident choices, avoiding unnecessary expenses while guaranteeing the integrity and safety of their end products.
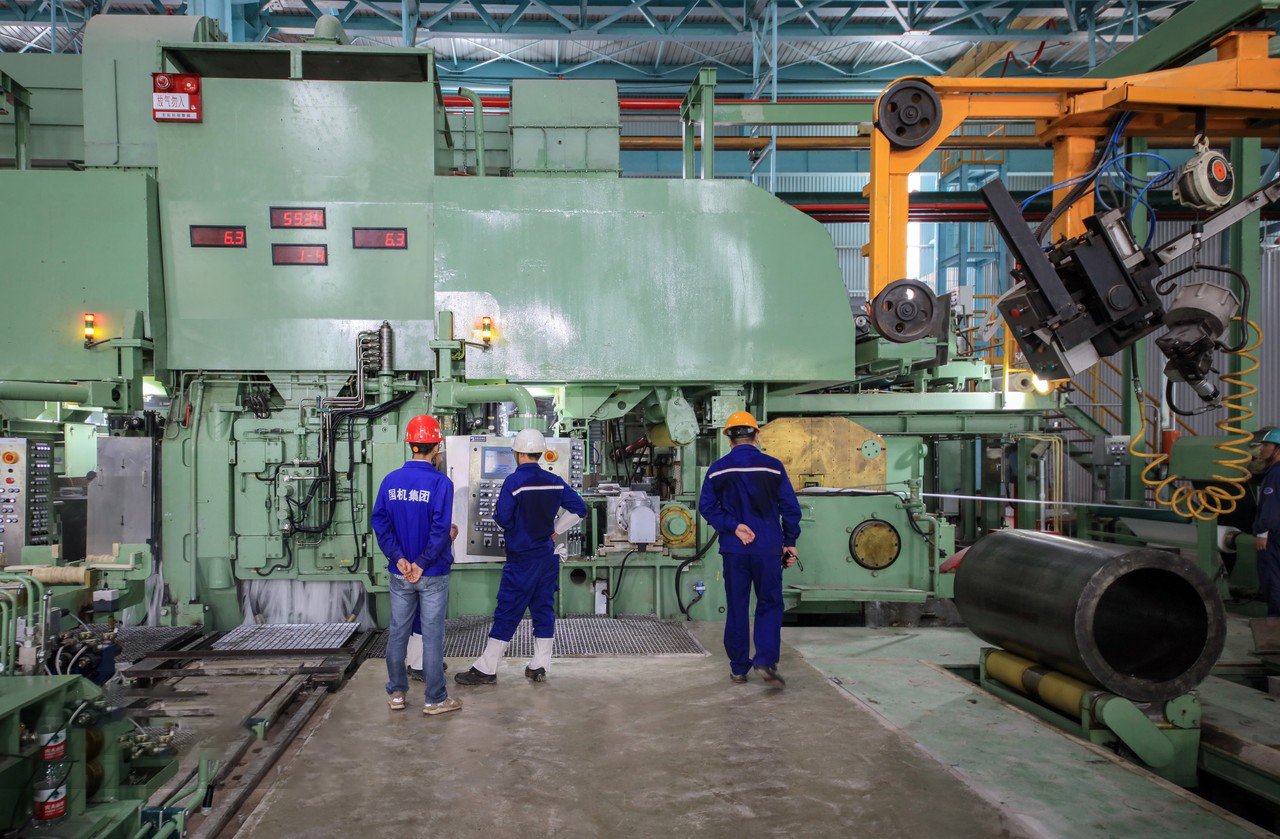
How Corrosion Resistance Defines Application Suitability
Corrosion resistance1 is arguably the most celebrated characteristic of 304 stainless steel. This property is primarily derived from its significant chromium content, which typically ranges from 18% to 20%. When exposed to oxygen, the chromium forms a thin, passive, and invisible layer of chromium oxide on the surface of the steel. This passive layer is self-healing; if it's scratched or damaged, it instantly reforms in the presence of oxygen, providing continuous protection against a wide variety of corrosive agents. This makes it an ideal choice for applications exposed to atmospheric conditions, fresh water, and most food and beverage products.
However, it's crucial to understand the limits of this resistance. While 304 performs exceptionally well against most oxidizing acids, it can be susceptible to corrosion from chloride solutions, such as seawater or de-icing salts. I remember a case with a new equipment integrator in India who was designing processing tanks. Their initial specification was 304 stainless steel for all components. During our consultation, we discovered that one part of their process involved a saline solution with a moderate chloride concentration. Had they proceeded, they would have faced pitting and crevice corrosion within months. By identifying this specific environmental challenge, we were able to recommend 316 stainless steel for that single component, while using the more cost-effective 304 for the rest of the assembly. This hybrid approach optimized both cost and performance, preventing a costly operational failure.
This self-healing passive layer is what makes 304 stainless steel a staple in hygienic applications like commercial kitchens, dairy processing, and pharmaceutical manufacturing. The smooth, non-porous surface is easy to clean and sanitize, preventing the buildup of bacteria and contaminants. The material's ability to withstand common cleaning agents and sterilizing processes without degrading ensures long-term safety and compliance with stringent health regulations. Its reliability in these settings is a testament to how a material's fundamental chemistry directly translates into critical real-world benefits.
The Critical Role of Formability and Weldability in Manufacturing
Beyond its resilience, the workability of 304 stainless steel is a primary reason for its widespread adoption. Its austenitic crystal structure gives it outstanding ductility, allowing it to be deep drawn, bent, stamped, and formed into complex shapes without cracking or losing its structural integrity. This is a massive advantage for manufacturers producing everything from intricate automotive components to large-scale architectural panels. The ability to form the material easily translates into lower tooling costs, faster production cycles, and greater design freedom.
A client of ours, a contractor specializing in custom architectural metalwork in the Middle East, relies almost exclusively on our 304 sheets. They create stunning facades and decorative interior elements that require precise and often complex bending and shaping. For them, the predictability and consistency of the material's formability are paramount. Any inconsistency could lead to wasted material and significant project delays. Their feedback has consistently highlighted that the superior ductility of MFY’s 304 sheets allows their craftsmen to push creative boundaries while maintaining manufacturing efficiency, a balance that is critical to their profitability.
Furthermore, the weldability of 304 stainless steel is excellent across all standard fusion and resistance welding techniques. This ease of joining is crucial for fabricating larger structures, such as tanks, piping systems, and structural supports. While it can be welded without pre-heating and generally doesn't require post-weld heat treatment for most applications, it's important to consider the potential for carbide precipitation at grain boundaries when welding thicker sections. This can reduce corrosion resistance in the heat-affected zone. To counter this, using low-carbon variants like 304L or employing appropriate welding techniques and filler metals is essential for maintaining the integrity of the entire structure, especially in more corrosive environments.
Balancing Mechanical Properties and Aesthetic Value
While 304 stainless steel is not primarily chosen for high-strength applications like hardened carbon steels, it offers a valuable combination of moderate strength, good toughness, and high ductility. In its annealed condition, it typically has a tensile strength of around 515 MPa (75,000 psi) and can be significantly hardened through cold working. This process of work hardening is often used in applications requiring higher strength, such as in the manufacturing of springs, fasteners, and structural components.
One of our target clients, a distributor in Russia, serves a diverse market of small to medium-sized manufacturing companies. They consistently report that the balanced mechanical profile of 304 is its strongest selling point. Their customers, who produce everything from industrial kitchen equipment to small machine parts, need a material that is strong enough for daily use but not so hard that it becomes difficult or expensive to machine and fabricate. The versatility of 304 allows this distributor to maintain a streamlined inventory that can meet the needs of a wide range of end-users, simplifying their logistics and ensuring consistent sales.
Finally, the aesthetic appeal of 304 stainless steel cannot be overstated. It is available in a wide variety of finishes, from a matte 2B finish to a highly reflective Bright Annealed (BA) or a brushed No. 4 finish. This aesthetic versatility makes it a favorite among architects and designers for applications like cladding, roofing, and interior fixtures. The clean, modern look of stainless steel, combined with its longevity and low maintenance requirements, provides a value proposition that few other materials can match. It delivers not just functional performance but also a lasting visual appeal that enhances the value of the final product or project.
304 stainless steel contains chromiumTrue
304 stainless steel contains 18-20% chromium, which forms a protective oxide layer that gives it corrosion resistance.
304 is magnetic in annealed stateFalse
304 stainless steel is non-magnetic in its annealed state due to its austenitic crystal structure.
How does the composition of 304 stainless steel affect its properties?
Have you ever wondered why one "stainless steel" performs so differently from another? This uncertainty can lead to costly material mismatches. The secret lies in the precise chemical recipe of each grade, where small changes in composition create vastly different performance characteristics.
The composition of 304 stainless steel, primarily its ~18% chromium and ~8% nickel content, is directly responsible for its signature properties. Chromium forms the passive, corrosion-resistant surface layer, while nickel stabilizes the austenitic structure, enhancing formability, weldability, and toughness.
I often explain to our clients that thinking of stainless steel as a single material is like thinking of all fabrics as just "cloth." The reality is far more nuanced. The specific percentages of elements like chromium, nickel, and carbon are not arbitrary; they are meticulously engineered to produce a specific set of behaviors. For example, a slight increase in nickel can improve weldability and formability, which was a critical factor for a manufacturing client in India producing deep-drawn kitchen sinks. They needed a material that could withstand significant plastic deformation without fracturing. By supplying a 304 coil with a nickel content at the higher end of the specification range, we helped them reduce their defect rate by nearly 15%. This demonstrates that a granular understanding of composition isn't just for metallurgists; it's a powerful tool for optimizing industrial processes and achieving superior results.
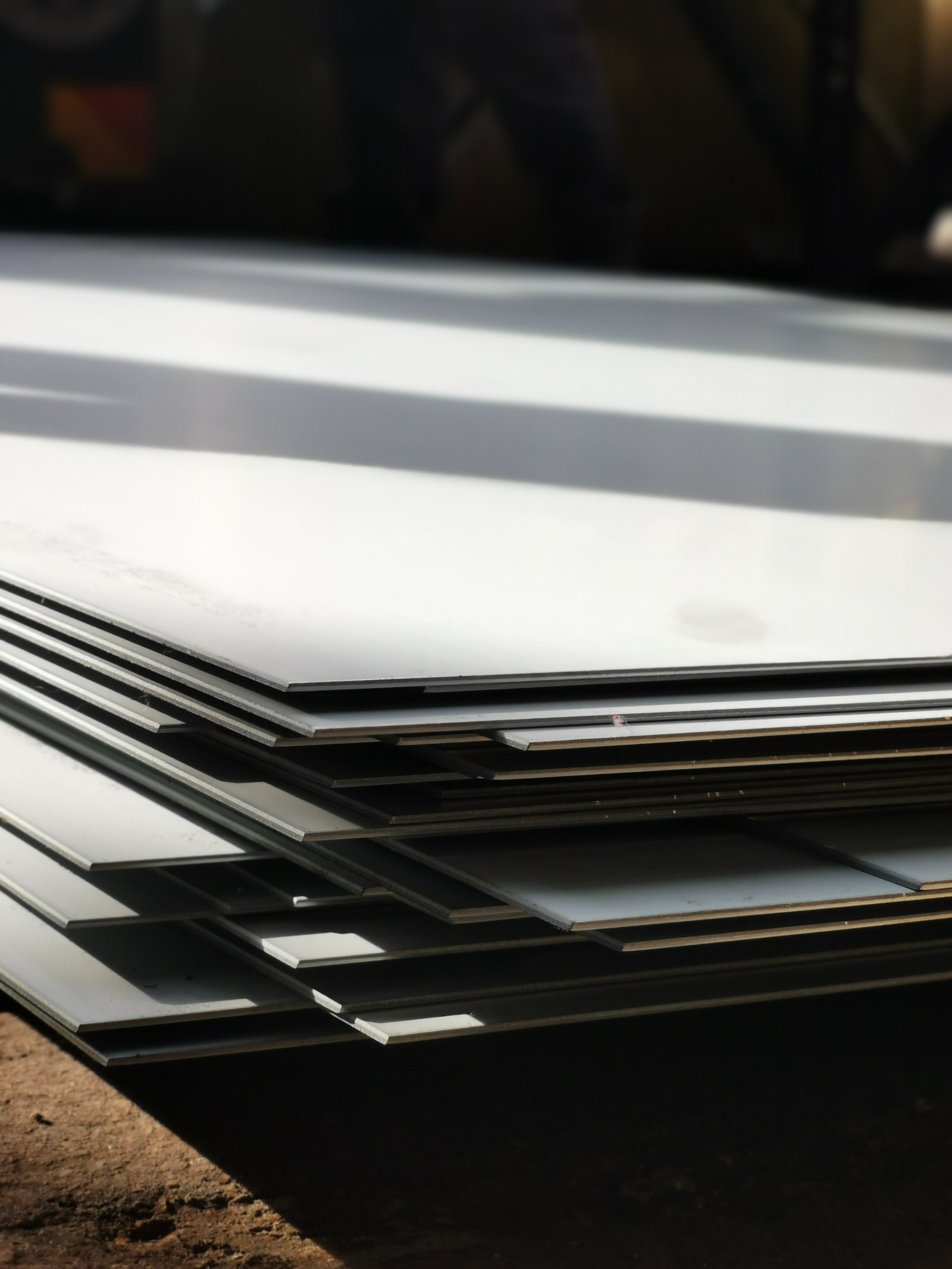
Chromium: The Architect of Corrosion Resistance
The single most important element in defining any stainless steel is chromium (Cr). For a steel to be classified as "stainless," it must contain a minimum of 10.5% chromium by weight. Grade 304 significantly exceeds this, with a composition of 18-20% chromium. This high chromium content is the primary reason for the material's excellent corrosion resistance. As mentioned earlier, chromium reacts with oxygen in the atmosphere to form a very thin, stable, and passive layer of chromium oxide ($Cr_2O_3$) on the steel's surface. This layer acts as a barrier, isolating the iron in the steel from the surrounding environment and preventing the oxidation process we commonly know as rust.
The robustness of this passive layer is remarkable. It is incredibly tenacious, adhering strongly to the steel surface, and is self-healing. If the surface is scratched, abraded, or cut, the exposed chromium immediately reacts with oxygen to reform the protective layer. This dynamic, self-repairing quality is what provides 304 stainless steel with its long-term durability in a wide range of environments. For instance, a construction contractor we supply in the humid climate of Southeast Asia uses our 304 sheets for exterior architectural cladding. Despite constant exposure to rain and humidity, the material maintains its integrity and appearance for decades, a direct result of the protective power of its chromium content.
However, the effectiveness of this chromium-oxide layer is dependent on the environment. While it provides superb protection against atmospheric corrosion and many chemicals, it has its limits. The layer can be compromised by reducing agents and, most notably, by chloride ions. This is why 304 stainless steel is generally not recommended for marine applications or environments with high salinity. Understanding this limitation is crucial for proper material selection, preventing misapplication and ensuring the long-term success of a project. The role of chromium is foundational; it transforms ordinary steel into a high-performance, corrosion-resistant material.
Nickel: The Key to Structure and Versatility
If chromium is the architect of protection, nickel (Ni) is the element that defines the structure and enhances the versatility of 304 stainless steel2. With a typical content of 8-10.5%, nickel's primary role is as an "austenite former." At room temperature, steel naturally wants to exist in a ferritic or martensitic crystal structure, which is magnetic and less formable. The addition of nickel stabilizes the austenitic crystal structure, which is a face-centered cubic (FCC) lattice. This austenitic structure is what gives 304 its most valuable mechanical properties: exceptional ductility, excellent formability, and superior weldability.
The practical implications of this nickel-induced austenitic structure are vast. It allows the steel to be bent, stretched, and drawn into complex shapes without undergoing brittle failure. I worked with an automotive parts manufacturer who was struggling with high rejection rates when forming a lower-grade ferritic stainless steel. The material was cracking during the deep-drawing process for exhaust system components. When they switched to 304, the problem was virtually eliminated. The superior ductility provided by the nickel-stabilized austenite allowed them to achieve the complex geometry required with a high degree of consistency, drastically improving their production efficiency and reducing material waste.
Beyond formability, nickel also enhances the material's performance at both high and low temperatures. It improves toughness, particularly at cryogenic temperatures, preventing the material from becoming brittle. It also contributes to better high-temperature strength and creep resistance. Furthermore, nickel improves the steel's performance in certain corrosive environments, particularly in reducing acids. It broadens the range of applications where 304 can be used effectively, making it a truly all-purpose grade. While nickel is one of the more expensive alloying elements, its contribution to the overall performance and workability of 304 stainless steel is indispensable, providing the unique combination of properties that manufacturers and engineers value so highly.
The Supporting Role of Carbon and Manganese
While chromium and nickel are the star players, other elements like carbon (C) and manganese (Mn) play crucial supporting roles that fine-tune the properties of 304 stainless steel. The carbon content in standard 304 grade is kept low, typically below 0.08%. Carbon is a powerful hardening agent in steel, but in austenitic stainless steels, it can be problematic. When the steel is heated to temperatures between 425°C and 815°C (as can happen during welding), carbon can combine with chromium to form chromium carbides at the grain boundaries. This process, known as sensitization, depletes the chromium from the surrounding areas, reducing the effectiveness of the passive layer and making the steel susceptible to intergranular corrosion.
To address this, a low-carbon variant, 304L, was developed with a maximum carbon content of 0.03%. This lower carbon level significantly reduces the risk of carbide precipitation during welding, making 304L the preferred choice for welded components that will be used in corrosive environments without subsequent heat treatment. We often recommend 304L to our engineering and construction clients for projects involving extensive on-site welding of pipes and tanks, providing them with an extra margin of safety against corrosion.
Element | Symbol | Typical % in 304 | Key Function |
---|---|---|---|
Chromium | Cr | 18.0 - 20.0% | Forms passive layer for corrosion resistance |
Nickel | Ni | 8.0 - 10.5% | Stabilizes austenite, enhances formability & weldability |
Carbon | C | < 0.08% | Provides strength; controlled to prevent carbide precipitation |
Manganese | Mn | < 2.0% | Improves hot workability; acts as an austenite stabilizer |
Silicon | Si | < 0.75% | Deoxidizer; improves resistance to scaling |
Phosphorus | P | < 0.045% | Impurity; kept low to maintain toughness |
Sulfur | S | < 0.030% | Impurity; kept low to improve weldability and formability |
Manganese, typically present at up to 2%, also contributes to the steel's properties. Like nickel, it is an austenite stabilizer, though less potent. It is often used to supplement nickel and helps to improve the steel's strength and hot workability, making it easier to process at the steel mill. By carefully controlling the balance of these primary and secondary elements, we at MFY can produce 304 stainless steel sheets with consistent, reliable properties that our clients can depend on for their most demanding applications.
Chromium prevents rust formationTrue
Chromium forms a passive oxide layer that prevents iron from oxidizing (rusting).
304 steel is ideal for marine useFalse
304's chromium oxide layer is vulnerable to chloride ions in seawater.
What industry applications benefit from using 304 stainless steel sheets?
Are you selecting materials based on tradition rather than optimal fit? This can lead to missed opportunities for innovation and efficiency. The key is to see how a versatile material like 304 stainless steel3 is being successfully applied across diverse industries to solve real-world challenges.
Industries that benefit most from 304 stainless steel sheets include food and beverage processing, architectural and construction, chemical and pharmaceutical equipment, and automotive manufacturing. Its unique combination of hygiene, corrosion resistance, formability, and aesthetic appeal makes it an ideal solution.
In my role, I have the privilege of seeing the incredible breadth of applications for 304 stainless steel. It’s far more than just a commodity. One week, I might be discussing specifications with a food processing equipment integrator in Southeast Asia who needs pristine, hygienic surfaces for their machinery. The next, I could be advising a construction contractor in the Middle East on the best finish for architectural panels that need to withstand sun and sand. This cross-industry exposure has shown me that the "benefit" of using 304 is not just in its technical properties, but in its ability to provide a reliable, cost-effective, and elegant solution to a vast array of industry-specific problems, from ensuring food safety to creating iconic buildings.
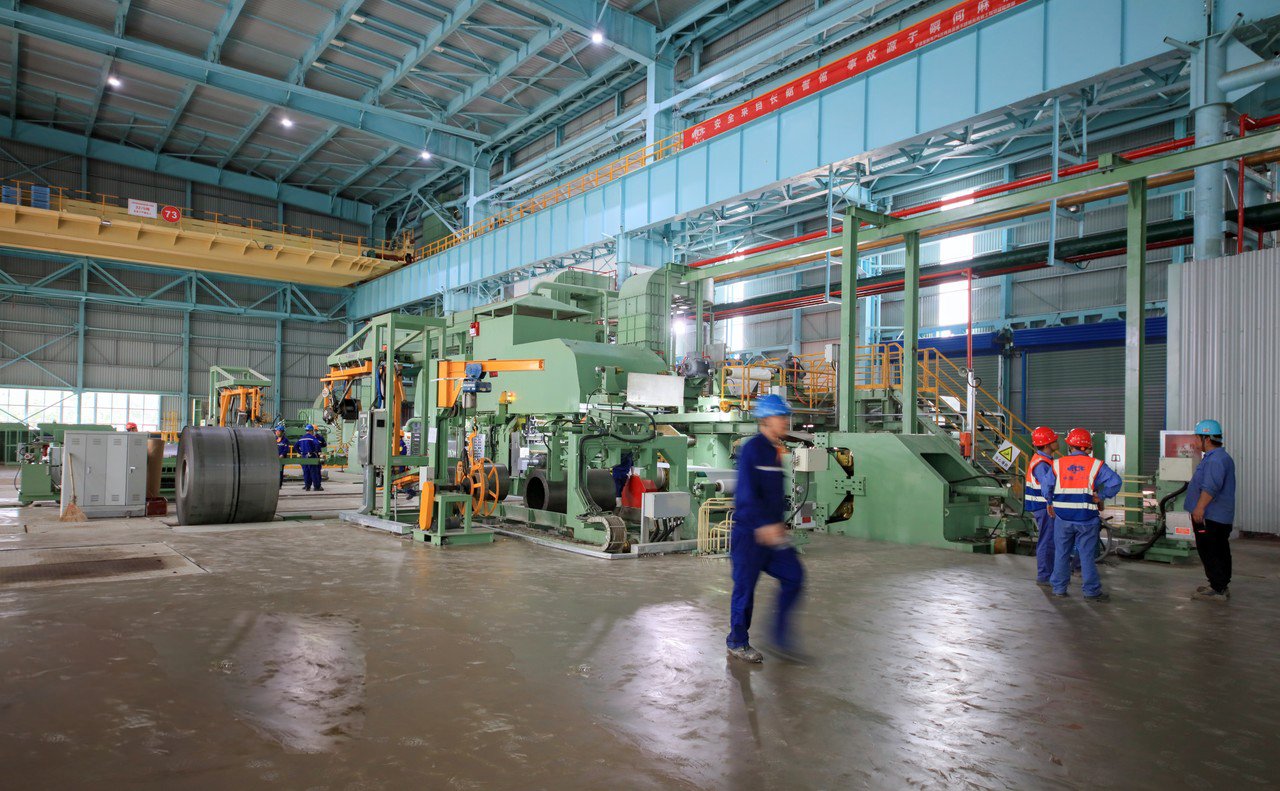
Food Processing and Commercial Kitchens: The Gold Standard for Hygiene
The food and beverage industry is one of the largest consumers of 304 stainless steel, and for good reason. The material's hygienic properties are unmatched. Its surface is non-porous, incredibly smooth, and easy to clean, which prevents the trapping of food particles and the growth of bacteria. This is a non-negotiable requirement in an industry governed by strict health and safety regulations. From mixing tanks and storage vessels to conveyor systems and preparation surfaces, 304 stainless steel4 is the material of choice because it imparts no taste or odor and can withstand the harsh, corrosive effects of various food acids and aggressive cleaning chemicals.
A great example comes from a long-standing client of ours in India that manufactures a complete line of commercial kitchen equipment for hotels and restaurants. They use our 304 sheets with a No. 4 brushed finish for everything from countertops and sinks to range hoods and refrigerators. The choice is strategic. The material not only meets the stringent food safety standards but also provides the durability to withstand the intense, fast-paced environment of a commercial kitchen—resisting dents, scratches, and constant scrubbing. The brushed finish is particularly practical as it helps to hide minor scratches and fingerprints, maintaining a professional appearance over time. Their success is built on the reliability and trust that 304 stainless steel provides.
According to industry reports, the global food processing equipment market is projected to grow significantly, driven by increasing consumer demand for processed foods and stricter food safety regulations worldwide. Within this market, the demand for stainless steel components is expected to rise in tandem. The proven track record of 304 stainless steel in food processing5 ensures it will remain the dominant material, offering an optimal balance of performance, cost, and compliance that is critical for manufacturers in this competitive field.
Architecture and Construction: A Fusion of Durability and Design
In the world of architecture and construction, materials are chosen for both their performance and their aesthetic contribution. 304 stainless steel excels on both fronts. Its excellent corrosion resistance makes it suitable for exterior applications such as facade cladding, roofing, and window frames, especially in urban and light industrial environments. It withstands weathering and pollution, retaining its appearance with minimal maintenance, which is a significant factor in reducing the long-term cost of ownership for a building.
I have personally witnessed a surge in the use of 304 for high-profile construction projects, particularly in rapidly developing regions like the Middle East. We supplied a significant quantity of 304 sheets with a mirror finish to a contractor for the interior of a luxury retail complex in Dubai. The designers chose it to create a sense of space and opulence, using it for column covers, elevator doors, and decorative trim. The material’s ability to be formed into sleek, modern shapes while providing a durable, easy-to-clean surface was essential to realizing the project's ambitious design vision. The reflective quality of the mirror finish also helped to amplify the interior lighting, enhancing the overall customer experience.
The versatility extends to structural applications as well. While not as strong as carbon steel, its corrosion resistance means it can be used for structural elements like handrails, support brackets, and canopies without the need for protective coatings like paint or galvanizing. This not only saves on initial costs but also eliminates future maintenance expenses associated with recoating. As sustainable building practices become more prevalent, the longevity and recyclability of stainless steel in architecture6 make it an increasingly attractive choice for architects and developers focused on building for the future.
Automotive and Transportation: Lightweight, Strong, and Lasting
The automotive industry operates under immense pressure to produce vehicles that are not only safe and reliable but also fuel-efficient and aesthetically pleasing. 304 stainless steel plays a key, if sometimes unseen, role in meeting these demands. It is widely used in the manufacturing of exhaust systems, including mufflers, pipes, and catalytic converter shells. Here, the material's resistance to high temperatures and corrosive exhaust gases is critical for ensuring the longevity of these components. Its ability to be easily formed and welded simplifies the manufacturing of these complex assemblies.
A few years ago, we worked with a Tier 1 automotive supplier who was developing a new exhaust system. They needed a material that offered a better lifespan than traditional aluminized steel but was more cost-effective than the higher-grade 316. 304 stainless steel in automotive7 provided the perfect balance. We provided them with sample coils for extensive testing, which confirmed the material's ability to withstand thermal cycling and acidic condensate, the primary failure modes for exhaust components. By adopting 304, they were able to offer an extended warranty on their products, giving them a distinct competitive advantage in the aftermarket parts industry.
Beyond exhaust systems, 304 is also used for various trim components, grilles, and wheel covers, where its bright, durable finish adds to the vehicle's visual appeal. In the broader transportation sector, it's used in the construction of tanker trucks for hauling chemicals and food products, as well as in components for rail cars and shipping containers. Its favorable strength-to-weight ratio compared to some other materials, combined with its corrosion resistance, contributes to building lighter, more durable, and more efficient transportation equipment.
304 stainless steel is used in food processingTrue
304 stainless steel's hygienic properties make it ideal for food processing equipment and surfaces.
304 is stronger than carbon steelFalse
While 304 stainless steel has excellent corrosion resistance, it is not as strong as carbon steel for structural applications.
What are the advantages of using 304 stainless steel sheets over other grades?
Confused by the alphabet soup of steel grades like 316, 430, or 201? Choosing the wrong one can mean overpaying for unnecessary performance or, worse, suffering premature material failure. The advantage lies in finding the "sweet spot" of cost and performance for your specific need.
The primary advantage of 304 stainless steel is its exceptional balance of cost, performance, and workability. It offers excellent corrosion resistance for most applications, superior formability, and weldability compared to many other grades, all at a more accessible price point than higher-spec alloys.
As a business director, I constantly emphasize the concept of "value engineering" with my clients. It's not about finding the cheapest option; it's about finding the most cost-effective solution for the entire lifecycle of the product. I often share the story of a distributor client in Vietnam who was facing intense price competition. Some of their customers were tempted to switch to cheaper 200-series stainless steel for their products. We provided our client with comparative data showing the long-term costs of corrosion failure and warranty claims associated with the lower-grade material. By arming them with this knowledge, they were able to educate their customers on the superior long-term value of 304. They successfully retained their clients by shifting the conversation from price per kilogram to total cost of ownership, a powerful advantage that 304's balanced profile provides.
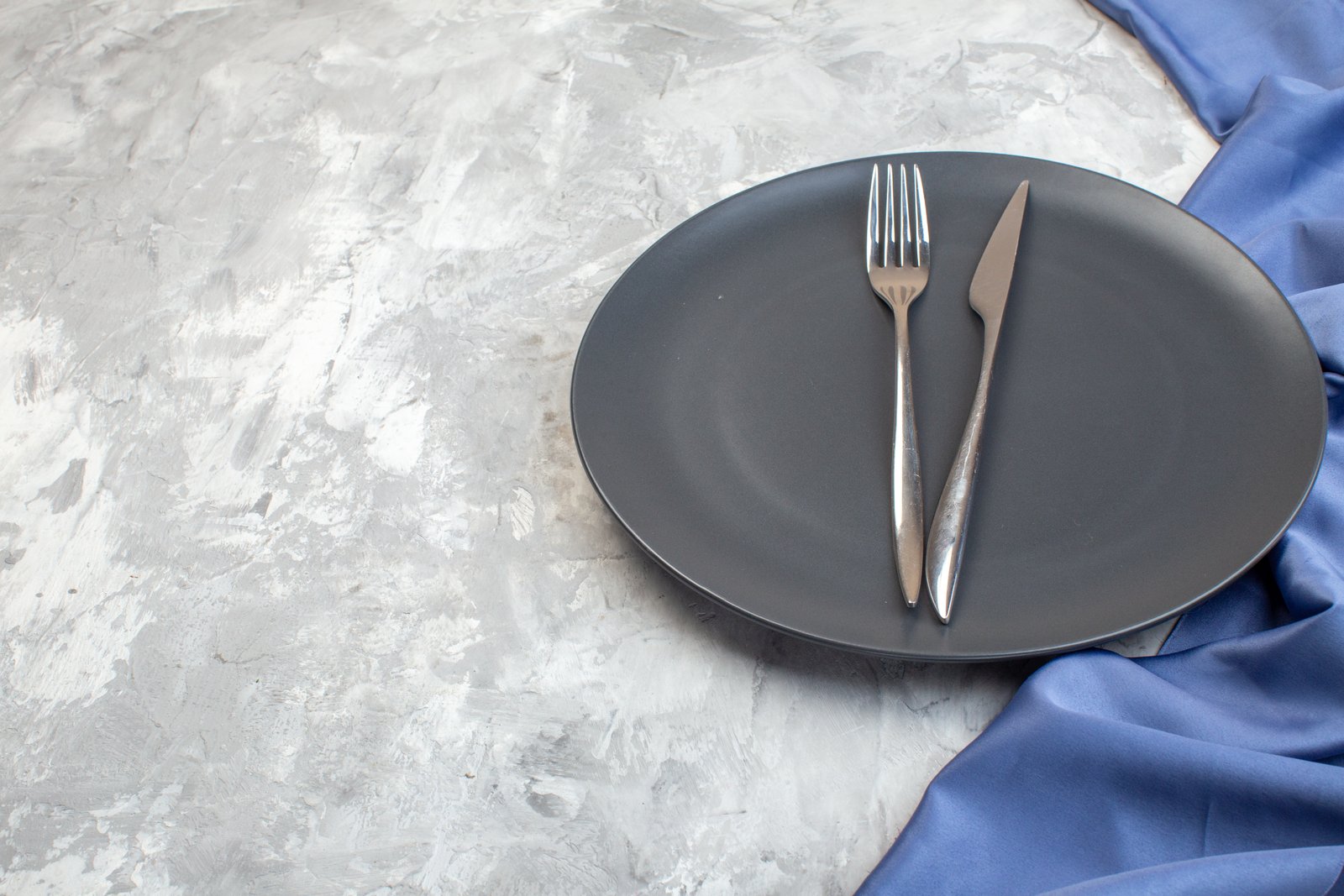
The Cost-Performance Sweet Spot: 304 vs. 316
The most common comparison in the austenitic stainless steel family is between Grade 304 and Grade 316. While they may look identical, their performance in certain environments differs significantly due to a key compositional difference: Grade 316 stainless steel8 contains molybdenum (typically 2-3%), which 304 lacks. This addition of molybdenum drastically enhances its resistance to corrosion, particularly from chlorides and other industrial solvents. This makes 316 the superior choice for marine applications, chemical processing plants dealing with aggressive chemicals, and coastal architectural projects. However, this superior performance comes at a premium price, as molybdenum is an expensive alloying element.
The key advantage of 304 lies in its cost-effectiveness for the vast majority of applications that do not involve high chloride exposure. For general-purpose use—in kitchens, for architectural trim in non-coastal areas, in food processing of non-saline products, and for general manufacturing—the corrosion resistance of 304 is more than sufficient. I frequently advise engineering contractors to conduct a thorough environmental analysis. A client planning a series of inland water treatment facilities initially specified 316 for all tanks and piping. After reviewing the water chemistry reports, which showed very low chloride levels, we demonstrated that 304 would provide a service life well beyond the project's requirements. By switching to 304 for the bulk of the project, they reduced their material costs by approximately 20-25% without sacrificing performance or safety. This is the essence of value engineering.
Choosing 304 over 316 where appropriate represents a strategic financial decision. The cost savings can be redirected to other critical areas of a project or can directly improve a manufacturer's profit margins. The ubiquity and high production volume of 304 also mean it often has better availability and more stable pricing, simplifying procurement and logistics. The advantage is clear: 304 provides all the performance you need for most jobs, without making you pay for the specialized resistance you don't.
The Durability and Formability Edge: 304 vs. 400 Series
Another frequent comparison is between 304 and ferritic stainless steels, most commonly Grade 430. The most immediate difference is cost; 430 is significantly cheaper because it does not contain expensive nickel. Grade 430 is a magnetic stainless steel that offers decent corrosion resistance, particularly against nitric acid, and is often used in applications like refrigerator paneling, automotive trim, and decorative interior elements. However, its advantages largely end with its lower price tag.
Grade 304 holds a substantial advantage in both durability and workability. The austenitic structure of 304 makes it far more ductile and formable than the ferritic 430. This means 304 can be subjected to deep drawing and more complex bending operations with a much lower risk of cracking. A manufacturer of kitchen utensils we supply learned this lesson the hard way. They experimented with 430 to lower costs on a line of mixing bowls but experienced high rates of failure during the deep drawing process. Reverting to 304 immediately solved the production issues. While the raw material cost was higher, the reduction in scrap and machine downtime made 304 the more profitable choice overall.
Furthermore, the weldability of 304 is vastly superior to that of 430. Welding 430 can result in brittle welds that are susceptible to failure unless specific pre-heating and post-weld heat treatments are applied, adding complexity and cost to the fabrication process. 304, particularly the 304L variant, can be readily welded with excellent results. For any application requiring significant fabrication, forming, or welding, 304 provides a level of reliability and ease of use that the 400 series simply cannot match, making it the better long-term investment for quality manufactured goods.
A Balanced Choice: 304 vs. 200 Series
In recent years, the 200 series of austenitic stainless steels has emerged as a lower-cost alternative to the 300 series. In these grades, the expensive nickel is partially replaced by manganese and nitrogen, which also act as austenite stabilizers. Grades like 201 are visually similar to 304 and possess similar mechanical properties in terms of strength and formability. This has made them a tempting option for cost-sensitive markets, particularly for decorative applications and household goods. However, this cost saving comes with a significant compromise in a critical area: corrosion resistance.
The lower chromium and nickel content in Grade 201 makes it significantly more susceptible to rust and pitting corrosion than Grade 304, especially in humid or polluted environments. We have seen numerous cases, particularly with clients who source finished goods from various suppliers, where products marketed as "stainless steel" begin to show rust spots after only a short period of service. Invariably, material analysis reveals the use of a 200-series grade instead of the specified 304. For any product that requires long-term durability and a lasting clean appearance—from industrial equipment to consumer appliances—304 offers a fundamental advantage in reliability.
This is why at MFY, we are strong advocates for material transparency. We encourage our clients, especially distributors and traders, to be vigilant about material certification and testing. Choosing 304 over 201 is an investment in brand reputation and customer satisfaction. The initial cost difference is small compared to the potential costs of product failures, warranty claims, and the loss of customer trust. Grade 304's advantage here is its dependable, industry-standard performance that provides peace of mind for both the manufacturer and the end-user.
304 offers better corrosion resistance than 200-seriesTrue
304 stainless steel has higher chromium and nickel content, providing superior corrosion resistance compared to 200-series grades like 201.
316 is always better than 304False
316 is only superior in chloride-rich environments; for most applications, 304 provides sufficient corrosion resistance at a lower cost.
What recommendations should be considered when selecting 304 stainless steel sheets?
Ready to purchase, but worried about hidden pitfalls in the procurement process? Simply choosing "304" isn't enough. Overlooking details like surface finish, thickness tolerances, or supplier credibility can lead to production issues and materials that don't perform as expected.
When selecting 304 stainless steel sheets, consider the required surface finish for your application (e.g., 2B, No. 4, BA), verify the precise thickness and tolerances, and, most importantly, partner with a reputable supplier who provides Material Test Certificates (MTC).
This final step—selection and procurement—is where the theoretical becomes practical. It's also where costly mistakes can happen. I always guide my new clients through a simple checklist. A recent case involved a new equipment integrator for the dairy industry. They knew they needed 304L for weldability, but they hadn't considered the surface finish. Their process required an extremely smooth, easy-to-clean surface to prevent bacterial buildup. By recommending a Bright Annealed (BA) finish over the standard 2B, we provided a surface that significantly improved the cleanability of their equipment, a critical performance metric for their end customers. This highlights that a successful outcome depends on getting these final details right.
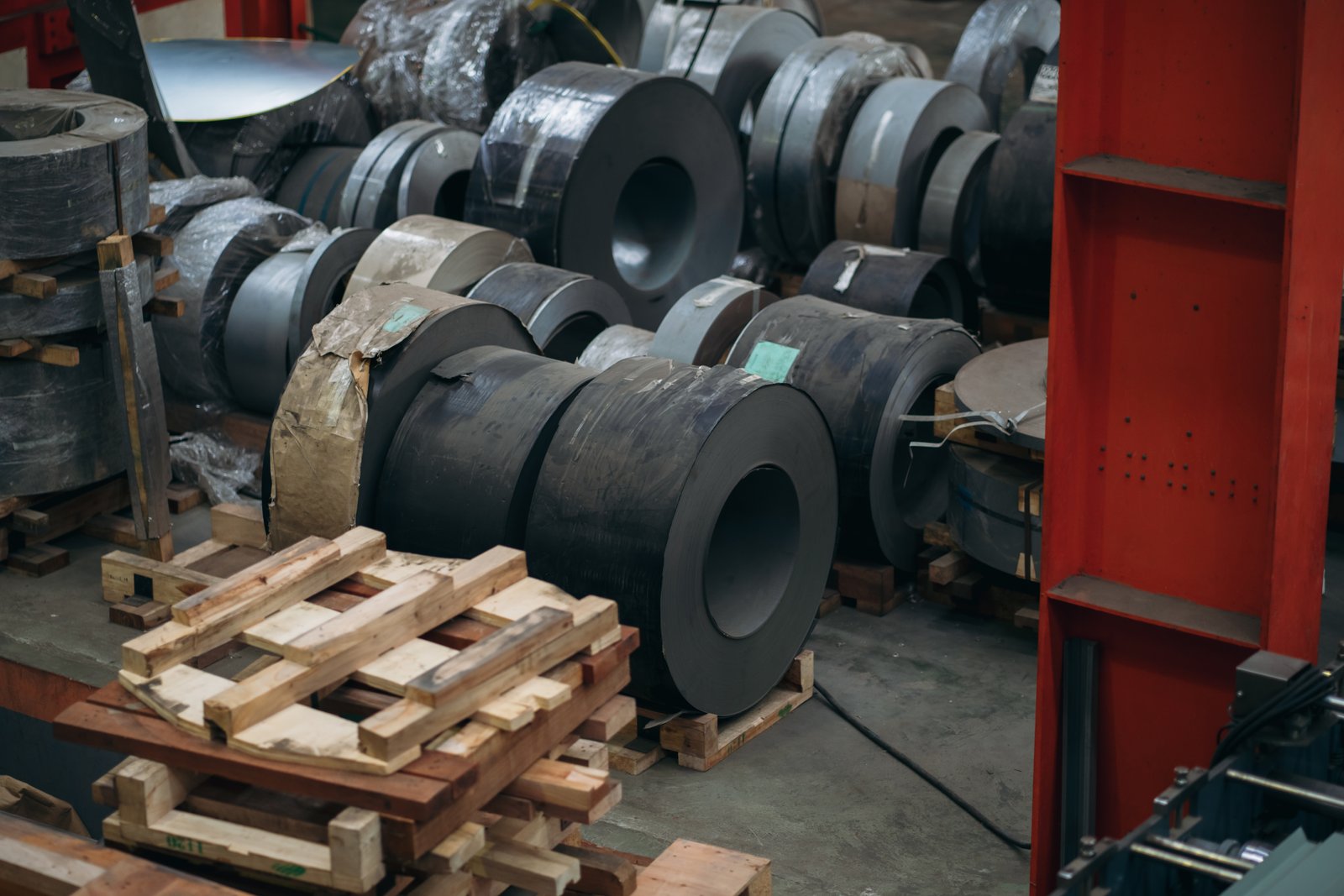
Specifying the Right Surface Finish for Function and Aesthetics
The surface finish of a stainless steel sheet is not just a cosmetic detail; it is a functional characteristic that has a significant impact on performance, cleanability, and cost. Choosing the correct finish is a critical step in the selection process. The most common mill finish is the 2B, a smooth, moderately reflective cold-rolled finish that is suitable for a wide range of applications where appearance is not the primary concern. However, for applications requiring higher aesthetic appeal or specific functional properties, other finishes should be considered.
For example, the No. 4 finish, which has a brushed, polished look with a uniform grain, is a favorite in architectural applications and for commercial kitchen equipment. The brushed pattern is effective at hiding minor scratches and fingerprints, making it practical for high-traffic areas. For applications demanding the highest level of reflectivity and smoothness, such as mirrors, decorative trim, and cleanroom equipment, the Bright Annealed (BA) finish is the ideal choice. It is produced by heat-treating the steel in a controlled atmosphere, resulting in a mirror-like appearance that is also exceptionally easy to clean. A client in the pharmaceutical industry depends on our BA-finish 304L sheets for their processing equipment specifically because its ultra-smooth surface minimizes product adhesion and allows for effective sterilization.
When making a selection, you must balance the desired aesthetic, the functional requirements of the application (like corrosion resistance and cleanability, as a rougher surface can sometimes trap contaminants), and the overall cost. More processed finishes like No. 4 or BA are more expensive than the standard 2B mill finish. Therefore, specifying the right finish ensures that you are not overpaying for a cosmetic quality you don't need, nor are you compromising the performance of your product with an inadequate surface.
Verifying Thickness, Tolerances, and Dimensions
Ensuring you receive the correct thickness and dimensions is fundamental to successful manufacturing. While it may seem obvious, variations in sheet thickness can have significant consequences. If a sheet is thinner than specified, it can compromise the structural integrity and strength of the final product. If it's thicker than required, it can lead to increased material cost, higher overall weight, and potential issues with forming and tooling. It is essential to specify not only the nominal thickness but also the acceptable tolerance range.
We once worked with a manufacturing company that was producing precisely engineered enclosures for electronic equipment. They were experiencing issues with parts not fitting together correctly. Upon investigation, we found that their previous supplier had been providing sheets with a wide thickness tolerance. Some sheets were at the low end of the acceptable range, and others were at the high end. This inconsistency was causing their automated bending and forming machines to produce parts with slight dimensional variations, leading to assembly problems. By supplying them with MFY's 304 sheets produced to a much tighter thickness tolerance, we eliminated the variability in their process, restoring the precision and consistency of their final product.
Beyond thickness, it's crucial to confirm the sheet's length and width, as well as its flatness and edge condition. Poorly leveled sheets can cause problems in automated cutting and stamping operations, while rough or slit edges may require additional processing before use. Always communicate your specific dimensional and tolerance requirements clearly with your supplier to ensure the material you receive is fit for your manufacturing process right out of the box, minimizing waste and pre-production labor.
The Critical Importance of Supplier Vetting and Certification
Perhaps the most important recommendation of all is to partner with a reputable and trustworthy supplier. In a global market, it can be tempting to choose a supplier based on the lowest price alone, but this can be a risky strategy. The quality and consistency of stainless steel can vary significantly between producers. A reliable supplier provides more than just a product; they provide assurance, transparency, and support. This starts with comprehensive documentation, most notably the Material Test Certificate (MTC) or Mill Test Report (MTR).
The MTC is a quality assurance document that certifies a material's chemical and physical properties. It should detail the precise chemical composition (showing the percentages of Cr, Ni, C, etc.), as well as the results of mechanical tests like tensile strength and elongation. I always insist that our clients request and review the MTC for every batch of material they receive. This document is your proof that you are getting exactly what you paid for—genuine Grade 304 with the properties required for your application. It protects you from substandard or counterfeit materials, like the lower-cost 200-series grades that are sometimes passed off as 304.
At MFY, we view our MTCs as a pact of trust with our clients. As a fully integrated group, we have control over the entire supply chain, from raw materials to final processing. This allows us to guarantee the quality and traceability of our products. When you select a supplier, ask about their quality control processes, their production capabilities, and their track record in your industry. A strong partnership with a supplier like MFY means you have access to technical expertise, a stable supply chain, and the confidence that the material you build your products with is of the highest standard.
Surface finish affects cleanabilityTrue
The BA finish provides an ultra-smooth surface that improves cleanability, crucial for industries like pharmaceuticals.
2B finish is most reflectiveFalse
Bright Annealed (BA) finish is the most reflective, not the standard 2B mill finish.
Conclusion
Ultimately, 304 stainless steel sheet is the industry's most trusted material for a reason. Its unparalleled balance of corrosion resistance, workability, and cost-effectiveness makes it a versatile and reliable foundation for countless applications, ensuring both product quality and sound commercial value for your projects.
-
Understand the role of chromium in enhancing corrosion resistance. ↩
-
Discover the impact of nickel on the formability and durability of 304 stainless steel ↩
-
Discover diverse applications and why industries choose 304 stainless steel ↩
-
Learn about its hygienic properties and regulatory compliance advantages ↩
-
Understand 304's role in food safety regulations and market growth ↩
-
Explore the durability, low maintenance, and aesthetic appeal in buildings ↩
-
Discover its role in exhaust systems and other vehicle components ↩
-
Discover how molybdenum improves 316's performance in corrosive environments ↩
Have Questions or Need More Information?
Get in touch with us for personalized assistance and expert advice.