What are the benefits of using 304 stainless steel tubing?
Struggling to find a material that offers longevity, strength, and value for your projects? The constant battle against corrosion, wear, and tear can lead to costly replacements and maintenance. 304 stainless steel tubing1 provides a reliable, cost-effective, and versatile solution for countless industrial applications.
Grade 304 stainless steel tubing is prized for its excellent corrosion resistance, high durability, and superior formability. Its composition, primarily 18% chromium and 8% nickel, creates a passive layer that resists oxidation and common corrosives, making it a versatile and long-lasting choice for various industries.
As Global Business Director at MFY, I've seen firsthand how choosing the right material can make or break a project's success. It’s not just about the initial cost, but the total lifecycle value. This is where 304 stainless steel truly shines, offering a balance of performance and affordability that is hard to beat. Let's explore why this material remains a top choice globally.
The decision to use 304 stainless steel tubing isn't merely a technical specification; it's a strategic business choice. In my experience, clients who embrace it move beyond simply purchasing a commodity. They are investing in operational stability and long-term asset integrity. For example, a client in the food processing industry initially considered a cheaper alternative but was swayed by data showing a 30% reduction in maintenance downtime over five years with 304 stainless steel. This highlights a crucial point: the material's inherent properties, such as its tensile strength of over 500 MPa and excellent weldability, translate directly into tangible economic benefits. Critically thinking, while 316 grade2 offers superior corrosion resistance in highly chlorinated environments, for the vast majority of applications—from architectural structures to automotive components—304 provides more than adequate performance at a significantly lower price point, making it the most pragmatic and economically sound choice for a wide spectrum of projects.
What are the key benefits of 304 stainless steel tubing?
Are your components failing prematurely due to environmental stress or material fatigue? This common problem leads to unexpected operational halts and budget overruns. The solution lies in a material engineered for resilience, offering a superior blend of strength, formability, and long-term value for your investment.
The key benefits of 304 stainless steel tubing include its exceptional corrosion resistance in various environments, high strength-to-weight ratio, and excellent fabrication characteristics. Its hygienic, non-porous surface and aesthetic appeal further expand its value, making it a cost-effective and versatile material for many applications.
In my years of navigating the global steel market, I've consistently seen clients return to 304 stainless steel tubing as their go-to solution. Its reputation isn't built on a single feature, but on a powerful combination of benefits that address the core challenges of modern manufacturing and construction. Think of it as the multi-tool of the alloy world; it’s strong, adaptable, and reliable. A client of ours, a large-scale contractor in Southeast Asia, once shared a story about a coastal hotel project. They had initially used galvanized steel for the balcony railings, but within two years, signs of corrosion were already visible due to the salty air. They replaced them with our 304-grade tubing, and a decade later, the railings still look pristine with minimal maintenance. This real-world example underscores the long-term economic wisdom of investing in a material that withstands environmental challenges, safeguarding both the structural integrity and the aesthetic value of the asset. This versatility extends beyond just durability; its excellent formability allows architects and engineers to create complex and elegant designs that would be impossible with more brittle materials.
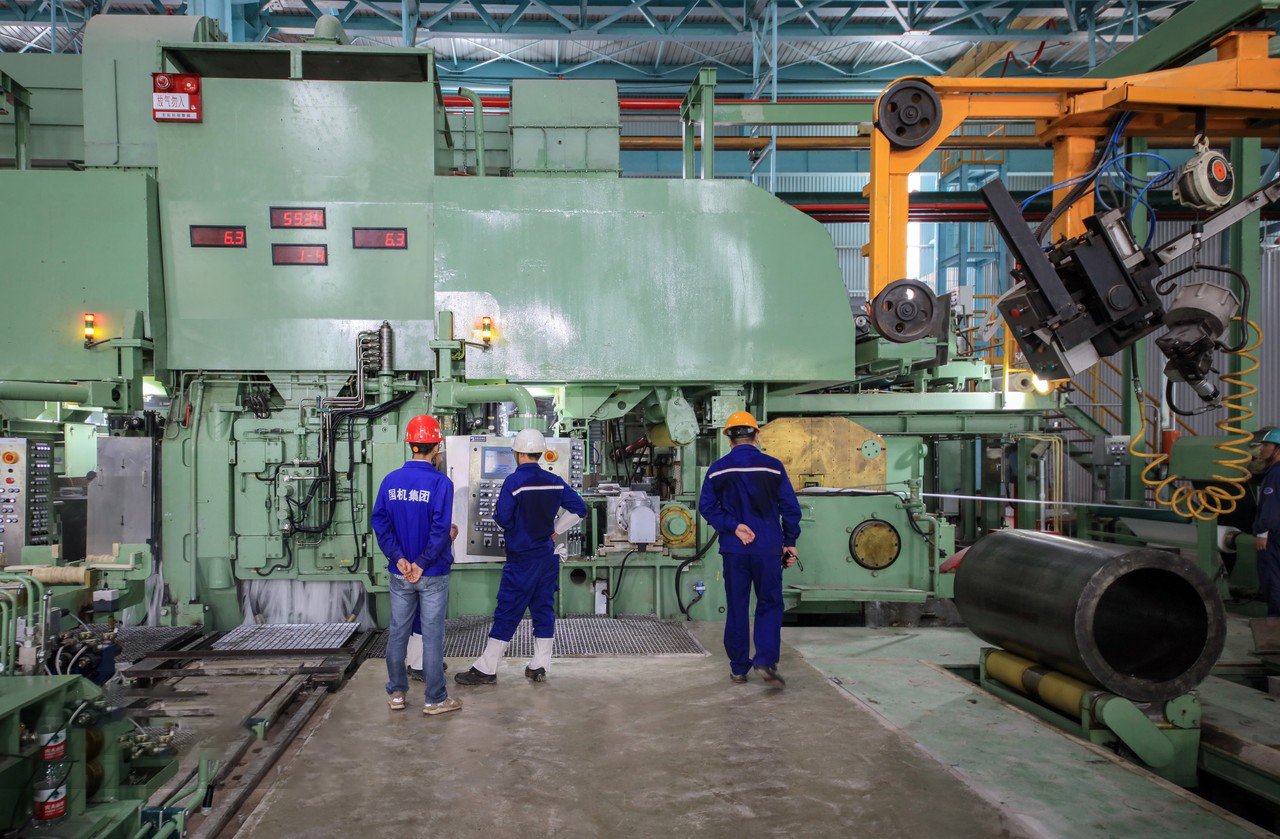
The decision to specify a material for any project, whether it's a massive architectural feat or a precision-engineered component, hinges on a complex interplay of cost, performance, and longevity. The enduring popularity of 304 stainless steel tubing is a testament to its mastery of this balance. It’s a material that doesn’t just meet specifications; it provides peace of mind. Its benefits are not abstract; they manifest in reduced maintenance budgets, extended product lifecycles, and enhanced safety and aesthetics. At MFY, we don't just supply steel; we provide a cornerstone for our clients' success, built on the proven performance of materials like 304 stainless steel. We guide our partners through the selection process, ensuring the material properties align perfectly with their application's demands, turning a simple purchase into a strategic advantage.
The Economic Advantage: Balancing Cost and Performance
When evaluating materials, the initial purchase price is just one part of the total cost of ownership equation. 304 stainless steel tubing presents a compelling economic case because it drastically reduces long-term expenditures. The primary saving comes from its inherent resistance to corrosion and degradation, which minimizes the need for costly repairs, replacements, and operational downtime. For instance, in a chemical processing plant, the cost of replacing a corroded pipeline extends far beyond the material and labor; it includes lost production, potential safety hazards, and cleanup efforts. By choosing 304, which resists most oxidizing acids and sterile solutions, the facility can operate with greater reliability and predictability.
I remember working with a mid-sized beverage manufacturer in India who was facing recurrent contamination issues traced back to their aging carbon steel piping system. The frequent maintenance and product spoilage were eating into their profits. We presented a comparative analysis showing that while the upfront investment for a full refit with MFY's 304 stainless steel tubing was 40% higher, the projected return on investment, factoring in reduced maintenance and eliminated product loss, was less than 18 months. They made the switch, and two years later, their maintenance director told me it was the best decision they had ever made for their plant's efficiency.
This economic benefit is further amplified by the material's longevity. While other materials might require protective coatings that need to be reapplied periodically, 304 stainless steel’s passive chromium-oxide layer is self-healing, ensuring its protective qualities endure for decades. This "install and forget" characteristic is a powerful economic driver, allowing capital and resources to be allocated to other growth areas instead of being tied up in asset maintenance. This long-term value proposition is why 304 remains the backbone of industries where reliability is not just preferred, but essential.
Versatility in Fabrication: Why Engineers Prefer 304
The theoretical benefits of a material are meaningless if it cannot be efficiently shaped and joined to meet design specifications. This is where the versatility of 304 stainless steel tubing truly comes to the forefront. Its austenitic crystal structure gives it outstanding ductility and formability, allowing it to be bent, drawn, and hydroformed into complex geometries without compromising its structural integrity. This is a critical advantage for engineers and designers who are constantly pushing the boundaries of innovation, whether in automotive exhaust systems that need to fit into tight spaces or in architectural designs featuring elegant curves.
This ease of fabrication directly translates into lower production costs and faster project timelines. A typical example comes from a client of ours who manufactures high-end kitchen equipment. Their designs often feature seamless, flowing lines which are both aesthetically pleasing and easy to clean. Using our 304 tubing, they were able to reduce their fabrication steps by 20% compared to a more brittle grade of steel they had tried previously. The material’s excellent weldability, particularly using common methods like TIG (Tungsten Inert Gas) and MIG (Metal Inert Gas), means that strong, reliable joints can be created with a clean finish, often requiring minimal post-weld treatment.
Furthermore, the consistency of MFY's 304 tubing ensures that fabrication processes are repeatable and predictable. We maintain tight tolerances on everything from wall thickness to chemical composition, which means our clients' automated bending and welding machines can run with fewer adjustments and lower rejection rates. This level of reliability in the raw material is crucial for manufacturers operating on lean principles, where every minute of production time counts. The inherent fabricability of 304 stainless steel is not just a convenience; it’s a core component of its value, enabling creativity and efficiency in equal measure.
Aesthetic Appeal and Low Maintenance: A Long-Term Value Proposition
Beyond its industrial and structural applications, 304 stainless steel tubing is widely celebrated for its clean, modern aesthetic. Its smooth, reflective surface can be finished in various ways—from a bright, mirror-like polish to a subtle brushed texture—to complement any design vision. This visual appeal is not fleeting. Unlike plated or coated materials that can chip, peel, or fade over time, the finish of stainless steel is integral to the material itself. This ensures that architectural features, consumer appliances, and decorative elements retain their beauty for years with minimal effort.
Consider the bustling environment of a major international airport. The handrails, column claddings, and signage are constantly exposed to traffic, luggage carts, and cleaning agents. I’ve seen projects where cheaper materials were used, and within a few years, they looked worn and dated, requiring significant refurbishment. In contrast, landmarks like the Chrysler Building and The Gateway Arch, which famously used stainless steel, have maintained their iconic luster for decades, cleaned primarily by natural rainfall. This enduring beauty is a direct result of the material’s passive layer, which resists staining and discoloration.
This low-maintenance aspect provides a significant long-term value proposition. For a commercial property owner, choosing 304 stainless steel for exterior cladding or interior fixtures means drastically reduced cleaning and maintenance budgets over the life of the building. The hygienic, non-porous surface is also incredibly easy to sanitize, a critical benefit for public spaces, hospitals, and of course, the food and beverage industry. This combination of timeless aesthetics and practical upkeep makes 304 stainless steel tubing an intelligent investment in lasting value.
Benefit Category | Key Feature | Practical Implication | Target Industry |
---|---|---|---|
Economic | High Total Lifecycle Value | Reduced maintenance and replacement costs. | Manufacturing, Chemical Processing |
Fabrication | Excellent Formability & Weldability | Faster production, complex designs possible. | Automotive, Engineering |
Aesthetic | Lasting Finish, Modern Look | Enhanced visual appeal, brand image. | Architecture, Consumer Goods |
Performance | High Corrosion Resistance | Increased product lifespan and reliability. | Food & Beverage, Marine |
304 steel resists oxidationTrue
The chromium content forms a passive oxide layer that prevents rust.
316 is always better than 304False
304 offers better cost-performance for most non-marine applications.
How does 304 stainless steel tubing impact durability and corrosion resistance?
Are you concerned that the materials you're using won't stand the test of time, especially in challenging environments? The threat of corrosion can silently undermine the structural integrity of your projects, leading to safety risks and costly failures. Choosing a material with proven resilience is paramount.
304 stainless steel tubing provides exceptional durability and corrosion resistance due to its 18% chromium content. This element forms a thin, invisible, and self-healing chromium oxide layer on the surface, which protects the iron base from rust and common environmental and chemical corrosives.
My experience in the steel industry has taught me that durability is not just about brute strength; it's about sophisticated material science. The magic of 304 stainless steel lies in its passive film—a feature that actively defends against degradation. I often explain to clients that they are not just buying steel; they are buying a self-repairing shield for their investment. A notable case involved a construction contractor in the Middle East building a large-scale desalination plant intake structure. They were hesitant about using 304 in a saline environment. We provided them with performance data and case studies demonstrating 304’s efficacy in brackish water applications, especially when proper cleaning schedules are maintained. By specifying MFY’s high-quality 304 tubing and implementing a simple freshwater rinse protocol, they successfully built a durable structure that met their budget, avoiding the much higher cost of specialized marine-grade alloys that would have been overkill for their specific application. This highlights how a deep understanding of the material's capabilities and limitations allows for smart, cost-effective engineering decisions that don't compromise on long-term performance.
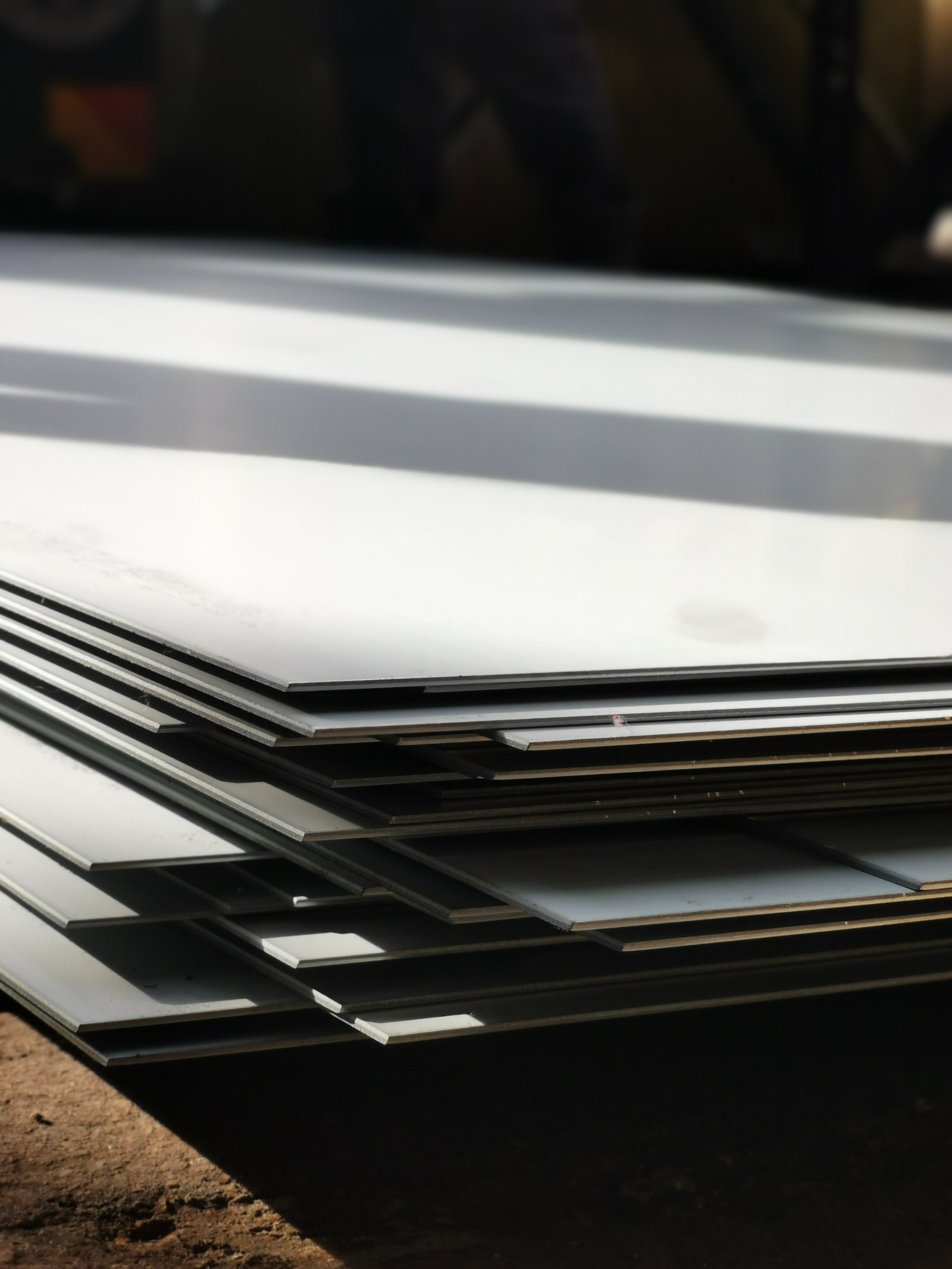
The conversation around durability often simplifies to a choice between "strong" and "weak" materials. However, the reality is far more nuanced, particularly when discussing corrosion. The true measure of a material's resilience is its ability to maintain its integrity over time in its intended service environment. 304 stainless steel's performance3 in this regard is not accidental; it is the result of precise alloying. The synergy between chromium and nickel in its composition creates a stable austenitic microstructure that is not only tough and ductile but also chemically resilient. At MFY, we leverage our integrated supply chain to ensure this precise chemical composition is maintained in every batch of tubing we produce. From sourcing raw materials to final processing, our quality control is rigorous, because we know that even a small deviation can impact the formation of that all-important passive layer. This commitment ensures that when our clients build with MFY steel, they are building with a material engineered for endurance, ready to withstand the rigors of its application from day one.
Understanding the Chromium Oxide Layer: The Science of Self-Healing
The primary reason 304 stainless steel is "stainless" is due to a remarkable phenomenon occurring at a microscopic level. The material is alloyed with a minimum of 10.5% chromium (304 grade typically has 18%). When exposed to oxygen, whether from the air or water, this chromium instantly reacts to form a very thin, stable, and inert layer of chromium oxide ($Cr_2O_3$) on the surface. This passive film is only a few nanometers thick, yet it is incredibly dense and non-porous, effectively creating a barrier that prevents oxygen and other corrosive elements from reaching the iron in the steel.
What makes this layer truly exceptional is its ability to "self-heal." If the surface of the tubing is scratched or cut, the newly exposed chromium almost instantaneously reacts with oxygen in the environment to reform the protective passive layer. This dynamic, self-repairing mechanism is what provides 304 stainless steel with its long-term, low-maintenance durability. It's a continuous, active defense, unlike a coating or paint which, once breached, leaves the underlying metal vulnerable to attack. I often use this analogy with clients: it’s like having a built-in, perpetually renewing coat of armor.
This scientific principle has profound practical implications. For an equipment integrator designing machinery for a food processing line, it means that the inevitable scratches and scuffs from daily use won't become points of rust and potential contamination. For an architect specifying railings for a public space, it means the structure will resist degradation from rain, pollution, and general wear. This fundamental property is the cornerstone of 304's reliability, providing a level of intrinsic protection that is unmatched by carbon steels or aluminum.
Pitting and Crevice Corrosion: Real-World Scenarios and Mitigation
While 304 stainless steel offers excellent general corrosion resistance, it's not entirely immune to all forms of attack, particularly in specific, aggressive environments. Two common localized corrosion types to be aware of are pitting and crevice corrosion. Pitting is a localized form of corrosion that creates small holes or "pits" in the metal, and it is most commonly initiated by exposure to chloride-rich environments, such as coastal sea spray or de-icing salts. Crevice corrosion, as the name suggests, occurs in tight, stagnant spaces—like under bolt heads or in gasket seals—where oxygen is depleted, preventing the passive layer from reforming.
Understanding these limitations is key to successful application. As a supplier, our role at MFY is not just to sell a product, but to ensure our clients use it correctly. I recall a case with a distributor whose customer was experiencing issues with 304 tubing used in a swimming pool equipment room. The warm, humid air with high chlorine content was causing premature pitting. While 316 grade, with its added molybdenum, is the standard recommendation for such direct chloride exposure, we were able to provide a more immediate solution. We advised them on design modifications to improve ventilation and a strict freshwater washing schedule to remove chloride deposits, which successfully mitigated the issue and extended the service life of the existing equipment.
This proactive approach to material education is crucial. By understanding the specific environmental triggers, manufacturers and engineers can design systems that minimize risk. This includes ensuring smooth welds to eliminate crevices, designing for free drainage to prevent stagnant solutions, and specifying regular cleaning protocols in chloride-heavy areas. By acknowledging and planning for these specific scenarios, the exceptional durability of 304 stainless steel can be maximized even in moderately challenging conditions.
The Role of Finishing and Passivation in Enhancing Longevity
The final state of the tubing's surface plays a critical role in its overall corrosion resistance and long-term durability. The manufacturing process itself—from welding to bending and polishing—can sometimes compromise the passive layer. For instance, welding can create heat tint or oxide scale, and tooling can embed free iron particles onto the surface. If not removed, these imperfections can become initiation sites for rust. This is why post-fabrication cleaning and, in some cases, passivation are essential best practices.
Passivation is a chemical treatment, typically involving a nitric or citric acid bath, that removes free iron and other contaminants from the surface and helps to thicken and strengthen the naturally occurring chromium oxide passive film. It doesn't "add" a layer; rather, it cleans and conditions the surface to optimize its inherent corrosion resistance. At MFY, we can provide tubing with a specific finish and can advise on proper passivation procedures to ensure the material performs at its peak.
The quality of the surface finish itself is also a factor. A smoother, polished surface has fewer microscopic peaks and valleys where corrosive particles can accumulate. This is why in hygienic applications, such as dairy or pharmaceutical processing, a highly polished finish (like a No. 4 or even a No. 8 mirror finish) is specified. I worked with a client who manufactures pharmaceutical mixing vessels. By shifting from a standard 2B mill finish to a polished and passivated interior surface for their tubing, they not only enhanced the cleanability of their equipment but also demonstrably improved its resistance to corrosion from the various chemical compounds they were handling, thereby ensuring product purity and extending the vessel's lifespan.
Parameter | Grade 304 SS | Carbon Steel | Aluminum (6061) |
---|---|---|---|
Primary Corrosion Mechanism | Passive $Cr_2O_3$ layer forms | Active oxidation (rust) | Passive $Al_2O_3$ layer forms |
Self-Healing Property | Yes | No | Yes, but less robust |
Resistance to Oxidizing Acids | Excellent | Poor | Fair to Good |
Resistance to Chlorides | Fair (susceptible to pitting) | Poor | Good |
Maintenance Requirement | Low | High (requires coating/painting) | Low to Medium |
Typical Tensile Strength | ~515 MPa | ~400 MPa | ~310 MPa |
304 stainless steel self-healsTrue
The chromium oxide layer reforms when scratched, providing continuous protection.
304 resists all corrosion typesFalse
304 is susceptible to pitting and crevice corrosion in chloride-rich environments.
What industries benefit the most from 304 stainless steel tubing applications?
Are you unsure if 304 stainless steel is the right fit for your specific industry needs? Selecting a material that doesn't align with your sector's standards for hygiene, durability, or aesthetics can lead to compliance issues and competitive disadvantage. A versatile material is key.
Industries that benefit most from 304 stainless steel tubing applications include food and beverage processing, architecture and construction, and automotive manufacturing. Its unique combination of corrosion resistance, hygiene, strength, and aesthetic appeal makes it the ideal choice for these demanding sectors.
As a global supplier, I have a unique vantage point on how different industries leverage the properties of 304 stainless steel. It’s fascinating to see the same material used to ensure the purity of milk in an Indian dairy and to provide the gleaming, durable façade of a skyscraper in Southeast Asia. This versatility is its greatest strength. For example, in the food industry, it’s not just about corrosion resistance, but about having a non-porous, non-reactive surface that won't harbor bacteria or alter the taste of the product. This is a non-negotiable requirement. For an architect, that same corrosion resistance translates into a building that maintains its visual appeal for decades against sun and rain. And for an automotive engineer, the material's excellent formability and strength-to-weight ratio are key to manufacturing lightweight, yet robust, exhaust systems and structural components. Each industry capitalizes on a different facet of 304's character, proving its immense value across the board.
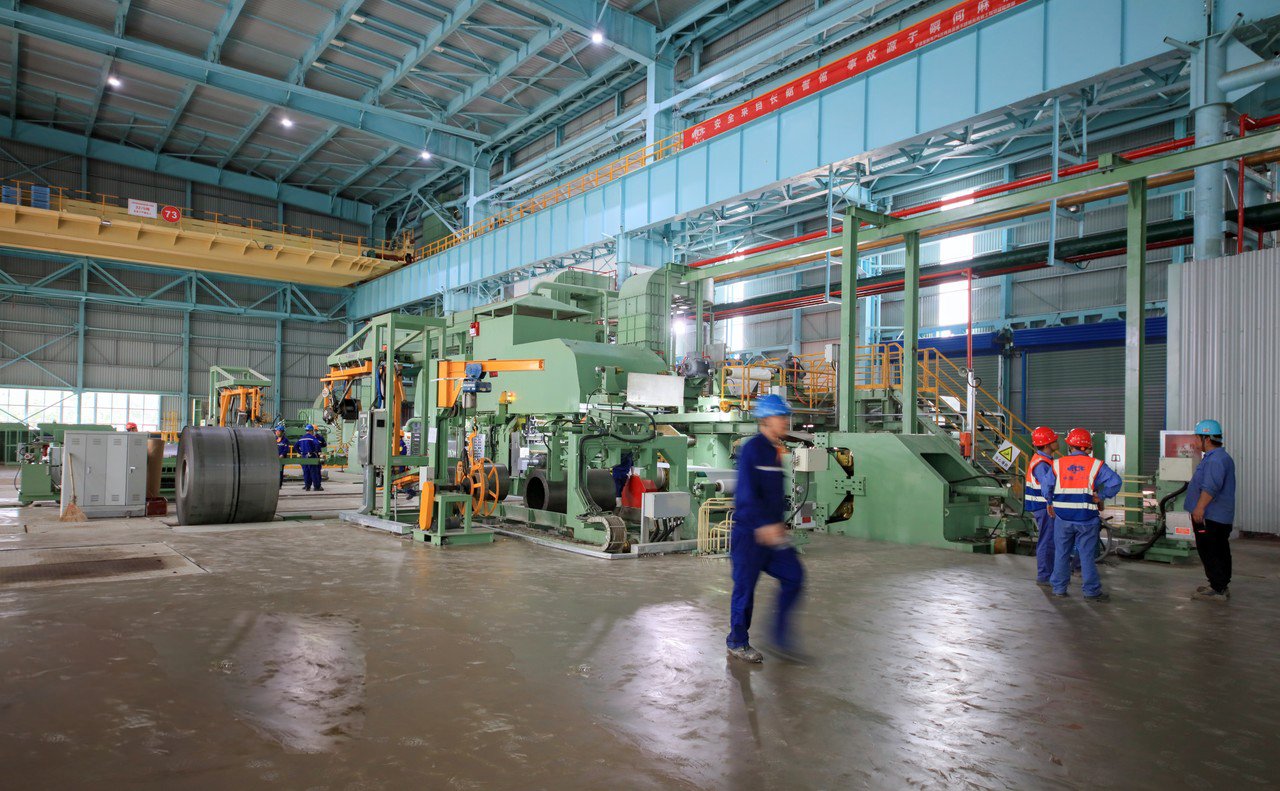
The widespread adoption of 304 stainless steel tubing across such diverse industries is no coincidence. It stems from the material's fundamental ability to solve core problems common to all of them: the need for longevity, reliability, and value. Whether the enemy is citric acid in a food plant, saline humidity in a coastal city, or corrosive exhaust gases in a vehicle, 304 provides an effective and economical defense. At MFY, our role is to act as a bridge, connecting the inherent potential of the material with the specific challenges of the industry. We work closely with our clients, from engineering contractors to equipment integrators, to understand their world. This collaborative approach allows us to not only supply high-quality tubing but also to share insights and best practices that help them innovate and excel within their respective fields, solidifying 304's position as a truly universal engineering material.
Food and Beverage: The Gold Standard for Hygiene and Safety
The food and beverage industry operates under the strictest standards of hygiene and safety, and 304 stainless steel tubing is the undisputed material of choice. Its primary advantage is its non-porous and non-reactive surface. This means it doesn't harbor bacteria or other pathogens within microscopic crevices, and it can be easily and effectively cleaned and sanitized to meet rigorous regulatory requirements from bodies like the FDA and EFSA. The material's ability to withstand aggressive cleaning chemicals4 and high-pressure washing cycles without degrading is crucial for maintaining a sterile production environment.
Furthermore, 304 stainless steel is prized for its inertness. It does not react with food products, meaning it won't alter their taste, color, or smell. I once consulted for a brewery that was experiencing a faint metallic taste in one of their craft beer lines. The issue was traced to an older section of piping made from a less stable material. After replacing the entire line with MFY's food-grade 304 tubing, the problem was completely eliminated, preserving the integrity and quality of their product. This is a perfect illustration of why material choice is so critical to the final consumer experience.
The durability of 304 also plays a key role. Processing equipment, from mixing tanks to conveyor systems and pipelines, must endure mechanical stress, temperature fluctuations, and the corrosive effects of various food acids (like citric, lactic, and acetic acids). According to Verified Market Research's report on the expanding global food processing sector5, the 304 stainless steel market is precisely because of its ability to provide a long-lasting, reliable, and hygienic infrastructure that safeguards both the product and the consumer.
Architectural and Construction: Blending Form with Function
In the world of architecture and construction, materials must deliver on two fronts: aesthetic appeal and structural longevity. 304 stainless steel tubing excels at both. Its clean, modern look and variety of available finishes, from brushed satin to a mirror polish, give architects immense design flexibility. It can be used for everything from striking curtain wall mullions and grand entranceways to durable handrails, balustrades, and decorative interior elements. As noted in guidelines by the Nickel Institute, iconic structures like The Gateway Arch6, clad in Type 304, demonstrate the material's ability to maintain its appearance over many decades, even with minimal maintenance.
The functional benefits are equally compelling. 304’s inherent corrosion resistance makes it ideal for exterior applications where it will be exposed to rain, snow, and urban pollution. This eliminates the need for paint or other protective coatings that would require periodic maintenance, thus lowering the building's lifecycle cost. A personal story I often share is of a client, a large property developer, who uses our 304 tubing exclusively for all the railings and exterior metalwork in their commercial projects. Their reasoning is simple: the "install and forget" nature of the material ensures their properties look pristine for years, enhancing tenant satisfaction and property value without adding to their maintenance burden.
Its strength is another key factor. Stainless steel's high tensile strength allows for the design of slender, yet robust, structural elements, contributing to a sense of lightness and elegance in the architecture. It's a material that doesn't force a compromise between beauty and brawn. It delivers both, making it a sustainable choice for buildings designed to be both inspiring and enduring.
Automotive and Transportation: Lightweight Strength for Modern Mobility
The automotive industry is in a constant pursuit of efficiency, which involves making vehicles lighter, more durable, and more resistant to harsh operating conditions. 304 stainless steel tubing is a key contributor to these goals, particularly in exhaust systems. An exhaust system must withstand extreme temperatures, corrosive gases, and constant vibration, as well as external attacks from road salt and moisture. 304 provides the perfect balance of high-temperature strength and corrosion resistance to handle these challenges, significantly outlasting traditional aluminized or carbon steel systems.
The formability of 304 tubing is critical for automotive engineers. Exhaust systems must be routed through complex and compact spaces within the vehicle's undercarriage. The excellent ductility of 304 allows it to be bent into tight radii without collapsing or cracking, enabling optimized gas flow and performance. This ease of manufacturing is essential for high-volume production lines where speed and precision are paramount.
Beyond exhausts, 304 stainless steel is also used for various other components, including fuel lines, sensor housings, and even structural elements in some high-performance vehicles. Its favorable strength-to-weight ratio helps engineers reduce overall vehicle mass, which in turn improves fuel economy and handling. As the industry moves towards more efficient and longer-lasting vehicles, the role of high-performance materials like 304 stainless steel will only continue to grow, making it an indispensable part of modern mobility.
Industry | Primary Requirement | Key 304 Benefit Utilized | Example Application |
---|---|---|---|
Food & Beverage | Hygiene & Non-Reactivity | Non-porous, inert surface | Dairy piping, mixing vats, conveyors |
Architecture | Aesthetics & Longevity | Lasting finish, corrosion resistance | Facades, railings, structural elements |
Automotive | Durability & Formability | High-temp strength, ductility | Exhaust systems, fuel lines, sensors |
Chemical Processing | Corrosion Resistance | Resistance to oxidizing chemicals | Pipelines, reactor vessels, valves |
304 stainless steel is used in food processingTrue
Its non-porous surface and corrosion resistance make it ideal for maintaining hygiene standards in food production.
304 steel alters food tasteFalse
304 is chemically inert and specifically chosen because it doesn't react with or affect food products.
How can manufacturers optimize the use of 304 stainless steel tubing?
Are you maximizing the potential of the materials in your production line? Simply using a quality material isn't enough; optimizing its application through smart design, fabrication, and supply chain management is where true competitive advantage is found. Inefficiencies can lead to waste and higher costs.
Manufacturers can optimize the use of 304 stainless steel tubing by focusing on strategic material specification, adopting advanced fabrication techniques, and integrating their supply chain. This holistic approach ensures the right grade is used, waste is minimized, and material flow is efficient.
From my perspective at MFY, I see optimization as a partnership. It’s not just about us delivering high-quality tubing; it's about us helping our clients use it in the most intelligent way possible. True optimization goes beyond the factory floor and starts with the initial design. I worked with an engineering contractor who was over-specifying a thicker wall tubing for a low-pressure hydraulic system out of an abundance of caution. By analyzing their operational parameters, we demonstrated that a thinner-walled MFY 304 tube would meet all safety and performance requirements, resulting in a 15% material cost saving and a lighter final product. This is optimization in practice: leveraging deep material knowledge and a collaborative spirit to achieve better outcomes—more efficient, more cost-effective, and ultimately, more competitive manufacturing. It's about transforming the material from a simple input into a strategic asset.
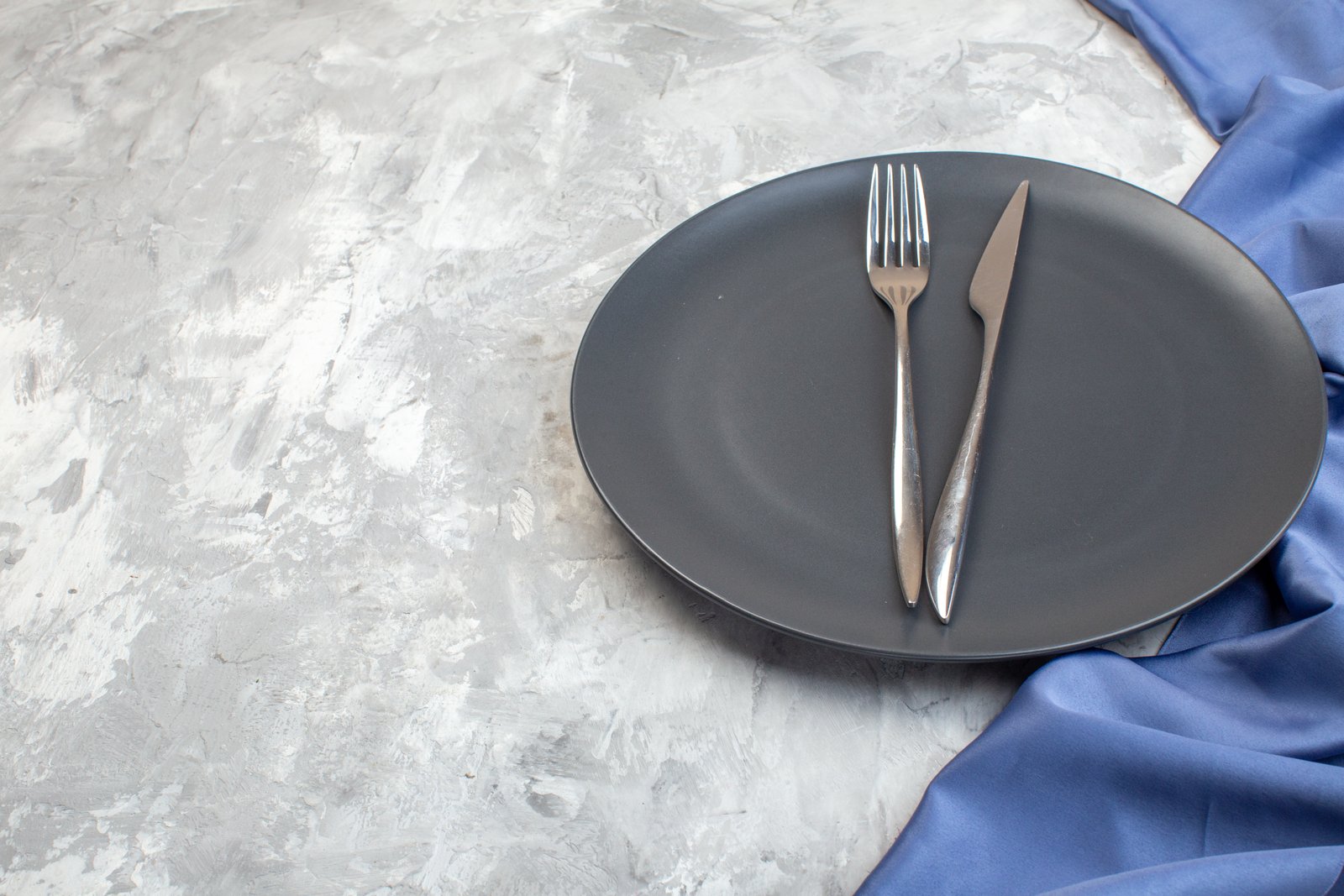
The quest for manufacturing excellence is a journey of continuous improvement, and material optimization is a critical leg of that journey. In a competitive global market, the manufacturers who thrive are those who scrutinize every aspect of their operation, from raw material procurement to final assembly. Optimizing the use of a versatile material like 304 stainless steel tubing can unlock significant value, but it requires a multi-faceted approach. It demands a shift in thinking—from viewing steel as a mere commodity to seeing it as an integral part of a lean, efficient production system. At MFY, our fully integrated supply chain7, from raw material trading to final tube manufacturing, gives us a unique ability to support this. We can provide not just the product, but the data, consistency, and reliability our clients need to fine-tune their processes, reduce waste, and build better products faster. This synergy between supplier and manufacturer is the key to unlocking the full potential of 304 stainless steel.
Strategic Material Specification: Matching Grade to Application
The first and most critical step in optimization is ensuring you are using the right material for the job. While "304 stainless steel" is a common term, there are subtle variations, such as 304L (low carbon) for improved weldability and reduced risk of intergranular corrosion in thicker sections. Choosing the correct variant can prevent future failures and reduce manufacturing complexity. Over-specifying—for instance, using the more expensive 316 grade when 304's corrosion resistance is perfectly adequate—is a common source of unnecessary cost. Conversely, under-specifying in a demanding environment leads to premature failure and warranty claims.
As a partner to our clients, we often engage in detailed application analysis. A manufacturer of heat exchangers in Southeast Asia approached us with a design that specified 304H (high carbon) for its superior high-temperature strength. However, upon reviewing their fabrication process, which involved extensive welding, we highlighted the potential for carbide precipitation. We collaboratively determined that using 304L for certain components and performing a final heat treatment would provide the necessary strength while ensuring maximum corrosion resistance in the heat-affected zones. This strategic specification saved them from potential field failures and optimized the product's lifespan.
This process involves a thorough evaluation of the service environment (temperature, chemical exposure, mechanical stress) and the fabrication methods. By precisely matching the material's properties to the application's demands, manufacturers can avoid paying for performance they don't need and ensure the reliability of their final product. This is the foundation of efficient and cost-effective manufacturing.
Advanced Fabrication Techniques: Welding, Bending, and Finishing
Once the right material is selected, optimizing how it's handled on the factory floor is paramount. For 304 stainless steel tubing, this centers on fabrication techniques that preserve the material's inherent properties. When it comes to welding, controlling heat input is crucial. As welding experts at MillerWelds advise, excessive heat can lead to warping and, more importantly, can sensitize the material, creating chromium carbides that reduce corrosion resistance. Utilizing techniques like TIG (Tungsten Inert Gas) welding for precise, clean welds, or pulsed MIG welding to manage heat input, are best practices. Furthermore, proper back-purging with an inert gas like argon is essential to prevent oxidation on the interior of the tube, which is critical for hygienic or fluid-flow applications.
Bending and forming processes also require careful control. Using the correct tooling, such as mandrels for tube bending, prevents the material from collapsing or cracking, ensuring structural integrity and a smooth interior for efficient flow. A client of ours, a manufacturer of architectural fixtures, significantly reduced their scrap rate by investing in a high-quality mandrel bender and working with our team to dial in the ideal bend radii for our specific tubing. This small change in process technology led to a major improvement in their production efficiency.
Finally, the finishing process should not be an afterthought. Proper cleaning to remove any free iron contamination from tooling, followed by passivation when necessary, restores and enhances the protective chromium oxide layer. By adopting these advanced fabrication practices, manufacturers can minimize waste, reduce rework, and produce a higher quality product that fully leverages the benefits of 304 stainless steel.
Supply Chain Integration: The MFY Approach to Efficiency
True optimization extends beyond the walls of the factory and into the supply chain. A reliable, responsive, and integrated supply chain is a powerful competitive weapon. Delays in material delivery, inconsistent quality, or large inventory requirements can cripple a lean manufacturing operation. At MFY, our vision is built around solving this exact problem. By integrating everything from raw material trading and cold-rolling to tube manufacturing and export logistics, we offer our clients a level of supply chain security and efficiency that is difficult to match.
For our target clients—be they manufacturers, contractors, or distributors—this integration means several things. First, it ensures consistent quality. Because we control the process from start to finish, we can guarantee the chemical and mechanical properties of our 304 tubing, which allows our clients to run their automated processes with confidence. Second, it leads to shorter lead times and more reliable delivery schedules. Our strong production capacity and inventory management mean we can respond quickly to our clients' needs, enabling them to reduce their own safety stock and improve cash flow.
I have seen the direct impact of this with a large engineering contractor we work with. They used to source tubing from multiple traders, leading to logistical headaches and variable quality. By consolidating their procurement with MFY, they streamlined their purchasing, received consistent, high-quality material on a predictable schedule, and ultimately improved their project execution timelines. This is the power of a fully integrated supply chain: it transforms the procurement of materials from a transactional process into a strategic partnership that drives efficiency across the board.
Optimization Area | Actionable Strategy | Key Benefit | MFY's Role |
---|---|---|---|
Specification | Conduct application analysis; choose correct sub-grade (e.g., 304L). | Avoids over-spending and premature failure. | Consultative partner providing material data. |
Fabrication | Control heat input in welding; use proper bending tools; passivate. | Reduces scrap, improves product quality and longevity. | Supplier of consistent material, technical advisor. |
Supply Chain | Consolidate procurement with an integrated supplier. | Shorter lead times, reliable quality, lower inventory costs. | Fully integrated supplier from raw materials to delivery. |
Design | Design for manufacturability (e.g., avoid tight crevices). | Reduces fabrication complexity and corrosion risks. | Sharing industry best practices and case studies. |
304L improves weldabilityTrue
304L's lower carbon content reduces carbide precipitation during welding, making it ideal for welded applications.
316 is always better than 304False
316 has superior corrosion resistance but is unnecessarily expensive for applications where 304's properties are sufficient.
What are the best practices for maintaining 304 stainless steel tubing?
Do you assume that "stainless" means "maintenance-free"? While highly resilient, neglecting proper care for your 304 stainless steel assets, especially in challenging environments, can lead to a gradual loss of integrity and appearance, diminishing your investment. A proactive approach is necessary.
The best practices for maintaining 304 stainless steel tubing involve regular cleaning to remove contaminants, immediate attention to any signs of discoloration or corrosion, and employing protective strategies in harsh environments. This preserves the passive layer and ensures maximum service life.
In my role, I often have to dispel the myth that stainless steel is invincible. It's incredibly robust, but not indestructible. Proper maintenance is the key to unlocking its full, multi-decade lifespan. The most important principle is simple: keep it clean. I recently advised a client who owns a chain of coastal cafes8 in Southeast Asia. They had installed beautiful brushed 304 stainless steel railings, but were noticing minor tea-staining due to the constant salt spray. We didn't recommend a costly replacement; instead, we provided them with a simple maintenance schedule involving a weekly wash-down with fresh water and a mild detergent. This simple, low-cost procedure was enough to remove the corrosive chloride deposits and restore the railings to their original condition. It’s a perfect example of how a little proactive care goes a long way in protecting the material and the investment.
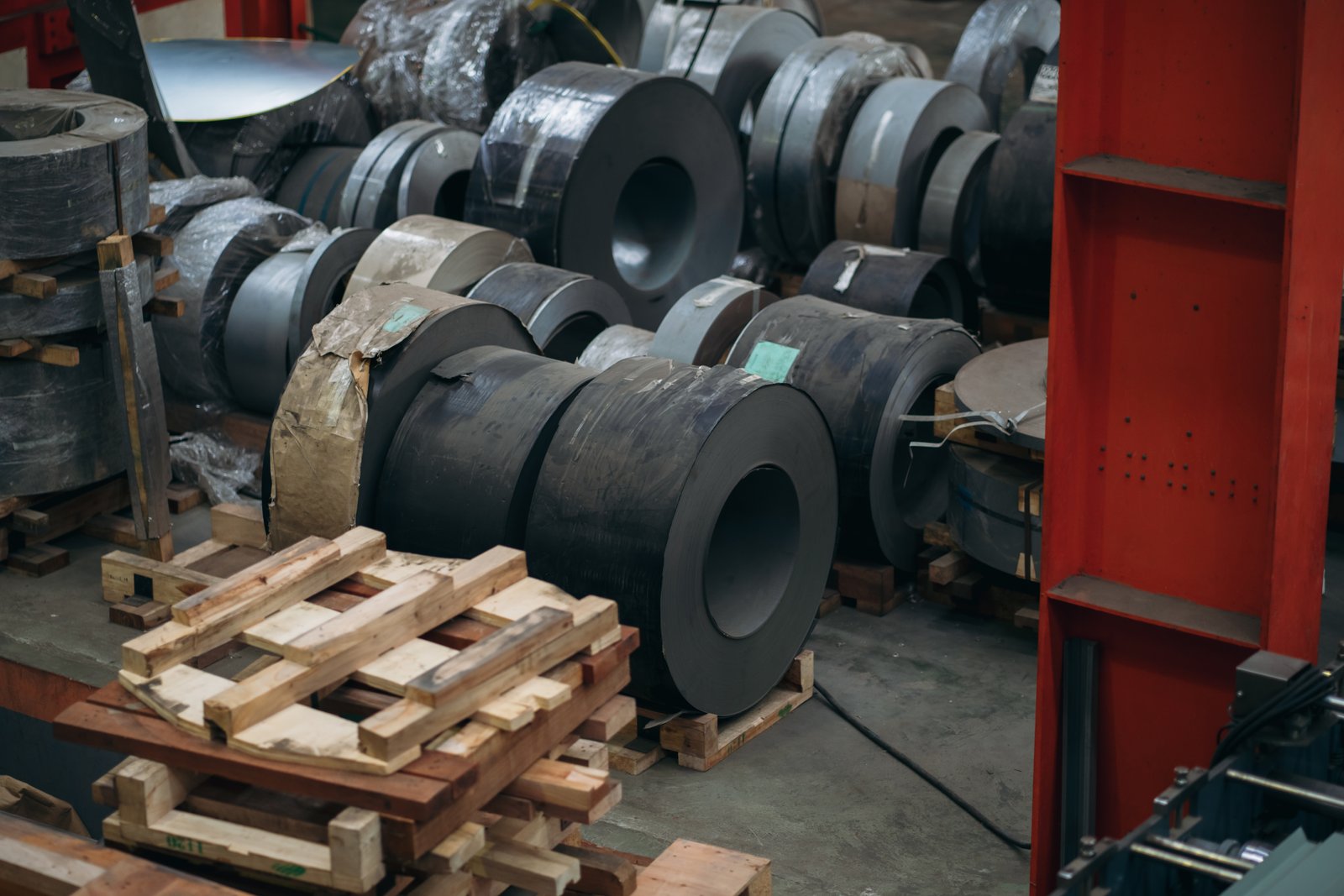
The longevity of 304 stainless steel is fundamentally linked to the health of its passive chromium oxide layer9. Maintenance, therefore, is not about applying coatings or adding protection; it's about creating and maintaining an environment where this passive layer can thrive. Any practice that removes surface deposits—dirt, salt, metallic particles—and allows the surface to have free access to oxygen will preserve the steel's integrity. Neglect, on the other hand, allows contaminants to accumulate, creating pockets where chlorides can concentrate or oxygen can be depleted, leading to localized corrosion. At MFY, we see our responsibility as extending beyond the point of sale. We believe in educating our clients, from large-scale contractors to local distributors, on these simple but crucial maintenance practices. By empowering them with this knowledge, we ensure that the MFY-branded tubing they install not only meets specifications on day one but continues to perform and look its best for many years to come.
Routine Cleaning Protocols: Preserving the Passive Layer
The most effective maintenance strategy for 304 stainless steel is routine, gentle cleaning. The goal is to remove surface deposits that could either break down the passive film or create crevices for corrosion to start. For most applications, especially architectural ones, cleaning with soap or a mild detergent and warm water, followed by a clear water rinse, is sufficient. It is crucial to rinse thoroughly to remove all cleaning agents. For a streak-free finish, especially on polished surfaces, wiping dry with a soft cloth is recommended. The frequency of cleaning depends on the environment; a rural exterior might only need cleaning once a year, while a surface in a marine or industrial zone may require cleaning every three to six months.
In my experience, consistency is more important than intensity. Aggressive cleaning with highly abrasive pads (like steel wool, which should never be used as it can leave iron particles) or chloride-containing cleaners (like bleach) can do more harm than good by scratching the surface and introducing corrosive agents. A client in the food processing industry learned this the hard way after an untrained cleaning crew used chlorinated sanitizers on their 304 stainless steel tanks, leading to pitting. We helped them develop a new protocol using appropriate alkaline cleaners and a final passivation step, which restored the equipment and prevented future issues.
The key takeaway is that the cleaning method should be the gentlest one that will get the job done. Regular, mild cleaning preserves the smooth, clean surface that allows the chromium oxide layer to protect the underlying steel effectively. It's a simple, low-cost insurance policy for the material's longevity.
Identifying and Addressing Early Signs of Corrosion
Even with proper maintenance, early signs of corrosion can sometimes appear, especially in more aggressive environments. It's vital to identify and address these signs promptly before they become significant problems. The most common sign on 304 stainless steel is "tea staining," a light brown surface discoloration that can occur in coastal or high-humidity areas. While it can be unsightly, it's important to note that tea staining is typically superficial and does not affect the structural integrity of the steel. It is, however, an indicator that surface deposits (usually salt) are not being removed frequently enough.
When such staining is identified, it can usually be removed with specialized stainless steel cleaners that often contain oxalic or phosphoric acid. It's critical to follow the manufacturer's instructions carefully and ensure the area is thoroughly rinsed with clean water afterward. For more stubborn spots or light rust from contact with carbon steel, a non-abrasive pad with the cleaning solution can be used, always scrubbing in the direction of the polish lines to avoid scratching.
I worked with a construction contractor who noticed minor rust spots on some 304 tubing installed near a welding area. We quickly identified the cause as iron particle contamination from grinding carbon steel nearby. By acting quickly—cleaning the affected areas with an appropriate gel cleaner and then implementing better housekeeping rules to isolate the stainless steel from carbon steel fabrication activities—they were able to resolve the issue completely. Early detection and swift, appropriate action are key to stopping localized corrosion in its tracks.
Long-Term Protection Strategies in Harsh Environments
For applications in particularly harsh or mission-critical environments, a more proactive long-term protection strategy may be warranted. While 304 is robust, environments with high concentrations of airborne chlorides, sulfur compounds (from industrial pollution), or other specific chemicals may require additional measures to ensure maximum service life. One effective strategy is the application of hydrophobic or barrier coatings. These are clear polymer or wax-based coatings that create a non-stick surface, making it more difficult for corrosive deposits to adhere and easier to clean them off.
Another strategy involves design. When designing components for harsh environments, it's crucial to avoid details that trap moisture and contaminants. This means designing for free drainage, using welded joints instead of bolted ones where possible to eliminate crevices, and orienting components to take advantage of natural rain washing. These design considerations, made early in the process, can significantly reduce future maintenance burdens.
A client in a heavy industrial zone was concerned about the long-term appearance of 304 stainless steel cladding on their new office building. While the material was suitable, the high level of industrial fallout was a concern. We recommended a two-part strategy: first, specifying a smoother surface finish (a 2B or No. 4 finish instead of a rougher one) to reduce particle adhesion, and second, scheduling a semi-annual professional cleaning and application of a clear protective sealant. This comprehensive strategy ensured their building would maintain its prestigious appearance despite the challenging surroundings, demonstrating that with the right plan, 304 stainless steel can succeed almost anywhere.
Maintenance Level | Environment | Recommended Action | Frequency |
---|---|---|---|
Routine | Rural / Light Urban | Wash with mild soap and water, rinse. | Annually / Semi-Annually |
Proactive | Marine / Coastal | Wash with mild soap and water, rinse thoroughly. | Quarterly / Monthly |
Restorative | Visible Tea Staining | Use specialized stainless steel cleaner, rinse, dry. | As needed |
Protective | Heavy Industrial / High Chloride | Professional cleaning and application of sealant. | Annually / Semi-Annually |
304 stainless steel requires maintenanceTrue
Despite being called "stainless", 304 steel needs regular cleaning to maintain its protective chromium oxide layer.
Steel wool is safe for cleaningFalse
Steel wool leaves iron particles that can cause corrosion; soft cloths and non-abrasive cleaners should be used instead.
Conclusion
In summary, 304 stainless steel tubing delivers an unparalleled combination of corrosion resistance, durability, fabricability, and aesthetic value. Its versatility makes it a cornerstone material for key industries, offering a cost-effective, reliable, and low-maintenance solution for a vast array of engineering and architectural challenges.
-
Discover how 304 stainless steel tubing is utilized in various industries ↩
-
Learn where each grade is most effectively applied regarding corrosion resistance ↩
-
Discover how alloying elements in 304 stainless steel improve its mechanical and chemical properties ↩
-
Learn about the chemical properties that make 304 stainless steel durable ↩
-
Insights into market trends and stainless steel demand in food processing ↩
-
Discover architectural feats showcasing the durability of 304 stainless steel ↩
-
Understand the advantages of supply chain integration in reducing lead times and ensuring consistent steel quality. ↩
-
Learn how environmental factors in coastal areas impact stainless steel and methods to protect it. ↩
-
Understand the science behind the passive layer's role in preventing stainless steel corrosion. ↩
Have Questions or Need More Information?
Get in touch with us for personalized assistance and expert advice.