What is 304 stainless steel?
Struggling to select the right material for your project? The sheer number of stainless steel grades can be overwhelming, and making the wrong choice can lead to costly failures and project delays. This guide will demystify 304 stainless steel1, the industry's most trusted and versatile alloy.
304 stainless steel is the most common austenitic stainless steel, containing approximately 18% chromium and 8% nickel. This composition gives it excellent corrosion resistance, superior formability, and strong weldability, making it a highly versatile and widely used material across countless industries globally.
By understanding the unique properties and applications of 304 stainless steel, you can make more informed purchasing decisions that optimize both performance and budget. In my role at MFY, I've guided countless partners through this selection process, ensuring their projects are built on a foundation of quality. Let's explore why this alloy might be the perfect solution for your needs.
As we dive deeper, it's crucial to look beyond the surface-level benefits. The global popularity of 304 isn't just about its technical specifications; it’s about its economic viability and supply chain maturity. According to market analysis2, 304 and its variants account for over 50% of all stainless steel produced globally, creating a stable and accessible supply chain. This ubiquity, however, demands a critical eye. While it's a fantastic general-purpose steel, its limitations in highly corrosive or high-temperature environments mean that specifying it without due diligence can be a costly mistake. My goal is to equip you with the nuanced understanding needed to leverage its strengths effectively.
What are the key properties of 304 stainless steel?
Are you concerned that the stainless steel you choose won't stand up to the demands of your application? Selecting a material without fully understanding its properties can lead to unexpected degradation, compromising product longevity and safety. Let's break down the core attributes that define 304's performance.
The key properties of 304 stainless steel are its excellent corrosion resistance in various environments, outstanding formability and weldability, and strong mechanical strength at ambient temperatures. Its hygienic, non-porous surface also makes it ideal for sanitary applications in the food and medical industries.
Understanding these foundational properties is the first step, but truly mastering material selection requires a deeper appreciation of how they interact within a specific industrial context. For instance, while its corrosion resistance is remarkable, it’s not absolute. Similarly, its formability comes with considerations regarding work hardening. A few years ago, we worked with a new client in the food processing industry in Southeast Asia. They were manufacturing large mixing vats and were initially drawn to 304 for its reputation. However, they were unaware of how the deep drawing process they used would affect the material's crystalline structure, a phenomenon known as work hardening. This process increases the steel's strength but reduces its ductility, making subsequent forming operations more challenging and increasing the risk of stress corrosion cracking if not properly managed. We guided them through annealing processes post-fabrication, a critical step to restore ductility and relieve internal stresses, ensuring the vats would have a long and reliable service life. This experience highlights why a surface-level understanding is insufficient; a successful project depends on a holistic view of the material's behavior throughout the entire manufacturing lifecycle.
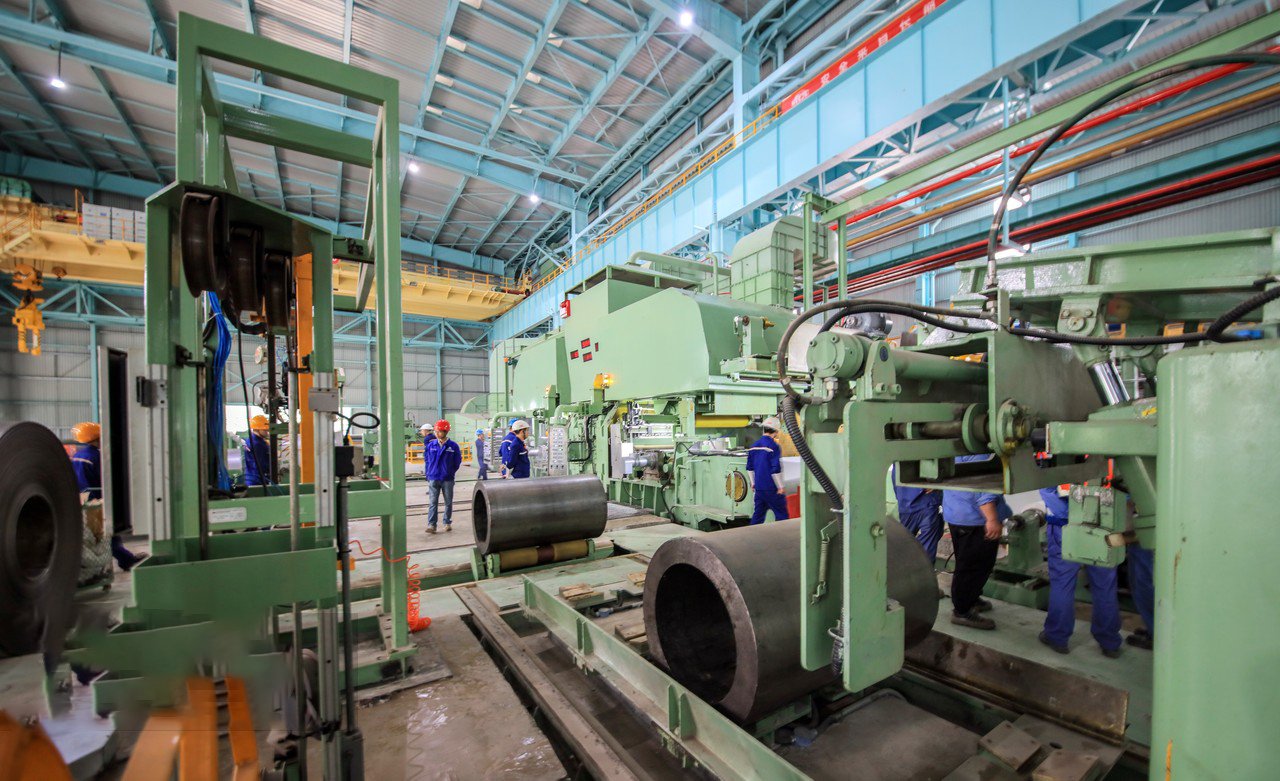
The versatility of 304 stainless steel is not accidental; it is a direct result of a finely tuned balance of chemical, mechanical, and physical properties. For our clients, from large-scale construction contractors to specialized equipment integrators, understanding this trifecta is non-negotiable for successful application and long-term performance. It’s the difference between a project that endures and one that incurs unforeseen maintenance costs. As a partner in their supply chain, it’s my responsibility to ensure they see the full picture, moving beyond a simple datasheet to a practical, operational understanding of the material they are investing in. This deeper knowledge prevents over-engineering with unnecessarily expensive alloys and under-engineering that leads to premature failure. It's about precision, efficiency, and building a foundation of trust through metallurgical expertise. We don't just sell steel; we provide the insights that make our clients' projects successful, resilient, and competitive in a demanding global market.
Unpacking the Chemical Resistance
The most celebrated property of 304 stainless steel is its corrosion resistance, a feature governed by its chemical composition. The key element is chromium, which must be present at a minimum of 10.5%. In 304, it typically ranges from 18% to 20%. When exposed to oxygen, the chromium forms a thin, stable, and passive layer of chromium oxide ($Cr_2O_3$) on the surface. This invisible film is self-healing; if scratched, it quickly reforms in the presence of oxygen, protecting the underlying steel from rust and chemical attack. The inclusion of 8% to 10.5% nickel is also critical, as it enhances this passivity, particularly in mildly acidic or reducing environments, and improves overall toughness and ductility.
However, this resistance has its limits, a fact we always emphasize to our clients. 304 stainless steel corrosion resistance3 is susceptible to chloride-induced corrosion, specifically pitting and crevice corrosion. This makes it unsuitable for prolonged exposure to saltwater or brine solutions. A client in the Middle East, an engineering contractor for a coastal desalination plant, once considered using 304 for non-critical structural components to save costs. We strongly advised against it, providing data that showed rapid pitting corrosion of 304 in environments with chloride concentrations above 100 ppm. We recommended grade 316, with its added molybdenum content, which offers significantly better resistance to chlorides. This guidance prevented a costly and potentially hazardous material failure down the line.
Furthermore, the operational environment extends beyond just chemical exposure. Factors like temperature and concentration play a massive role. For example, 304 performs well in handling nitric acid over a wide range of temperatures and concentrations, making it a staple in the chemical processing industry. Conversely, its performance with sulfuric acid is limited to very low concentrations at ambient temperatures. We provide our clients with detailed corrosion tables, but we also stress the importance of in-situ testing when possible. A distributor in India supplying to the local textile industry learned this lesson when 304 components in a dyeing machine failed prematurely. The dye baths contained not only acids but also salts at elevated temperatures, creating a synergistic corrosive environment that overwhelmed the 304's passive layer.
Analyzing Mechanical Strength and Formability
From a mechanical standpoint, 304 stainless steel offers an excellent combination of strength and ductility, which is why it's a favorite among manufacturers. In its annealed condition, it typically exhibits a tensile strength of around 515 MPa (75,000 psi) and a yield strength of 205 MPa (30,000 psi). More importantly, its high elongation, often exceeding 60%, allows it to be severely deep drawn, bent, and formed without cracking. This property is invaluable for producing complex shapes like kitchen sinks, hollowware, and automotive trim. One of our major clients, a manufacturer of high-end cookware, relies exclusively on our prime-grade 304 coils for their deep drawing operations. The consistency of our material's grain structure and mechanical properties ensures they can maintain high production speeds with minimal reject rates, a critical factor for their profitability.
A key characteristic of austenitic stainless steels like 304 is their propensity to work harden. As the material is cold-worked (e.g., rolled, drawn, or bent), its crystal structure deforms, increasing its tensile strength and hardness but reducing its ductility. This can be both a benefit and a challenge. For applications requiring higher strength, such as in structural components or fasteners, controlled cold working can be used to achieve desired mechanical properties. However, for multi-stage forming operations, work hardening can make subsequent steps difficult. A typical case involves a construction contractor using 304 for custom architectural panels. The initial bends were easy, but as more complex folds were introduced, the material became harder to work with, and they began to see cracking at the bend radii.
To manage this, we advise clients on the importance of process annealing. By heating the steel to a specific temperature (typically around 1010-1120°C) and then rapidly cooling it, the internal stresses from cold working are relieved, and the ductile austenitic structure is restored. This allows for further forming operations. Understanding the rate of work hardening and planning for intermediate annealing steps is a critical part of the fabrication process. It’s a conversation we have frequently with equipment integrators who are fabricating complex assemblies, ensuring they can achieve their designs without compromising the material's integrity.
Physical Properties and Fabrication Excellence
The physical properties of 304 stainless steel directly contribute to its ease of fabrication and performance in various applications. Its density is approximately 8.0 g/cm³, and its thermal conductivity is relatively low compared to carbon steels. This low thermal conductivity requires adjustments during welding, as heat tends to concentrate near the weld, potentially causing distortion or warping if not managed correctly. We often provide our clients, especially those new to stainless steel fabrication, with best-practice guides for welding 304. This includes recommendations on heat input, welding speed, and the use of fixtures to control distortion.
Weldability is one of 304's strongest assets. It can be readily welded by all common fusion and resistance welding methods. However, a critical consideration is the potential for carbide precipitation. If the steel is held in a temperature range of 425-860°C for too long during welding or cooling, chromium can combine with carbon in the steel to form chromium carbides along the grain boundaries. This depletes the chromium from the surrounding area, reducing its corrosion resistance and making the weld zone susceptible to intergranular corrosion. To mitigate this, we often recommend using low-carbon variants like 304L, which has a maximum carbon content of 0.03% compared to 0.08% for standard 304. For a client fabricating large tanks for the beverage industry in Russia, switching to 304L was a game-changer, eliminating post-weld corrosion issues they had previously faced.
Beyond welding, the machinability of 304 is another important consideration. It is tougher and more "gummy" than carbon steel, leading to poor chip breaking and increased tool wear. We advise machinists to use sharp, rigid tools, slower speeds, and heavier feeds to get below the work-hardened layer. Proper lubrication is also essential. By providing these practical tips, we help our partners in manufacturing optimize their machining processes, reduce downtime, and improve the surface finish of their final products. This holistic support, extending from raw material supply to final fabrication, is a core part of MFY's value proposition.
304 contains 18% chromiumTrue
The chromium content in 304 stainless steel is typically 18%, which forms a protective oxide layer for corrosion resistance.
304 resists all chloride corrosionFalse
304 is susceptible to pitting corrosion in chloride-rich environments, requiring grade 316 for such applications.
How does 304 stainless steel compare to other types of stainless steel?
Worried you might be overpaying for a material with features you don't need, or under-specifying and risking failure? The stainless steel family is vast, and choosing between grades like 304, 316, and 201 can be perplexing. Let's clarify the key differences to guide your decision.
304 stainless steel offers a balanced performance at a moderate cost. Compared to 316 stainless steel, it is less resistant to chlorides but more economical. Versus 201 stainless steel, it has superior corrosion resistance and formability due to higher nickel content, while being more expensive.
Making the optimal choice requires a cost-benefit analysis tailored to your specific application. It's a frequent topic of discussion I have with clients. For example, a distributor in India might find the lower upfront cost of 201 series stainless steel appealing for budget-conscious consumer goods. However, for coastal applications or industrial equipment, the superior longevity of 304 or even 316 provides better long-term value, preventing costly replacements and reputational damage. My role is to illuminate these trade-offs, ensuring that the material's lifecycle cost, not just its initial price, is the primary driver of the decision. We’ve seen firsthand how a small upfront investment in the right grade can yield significant savings over the product's lifespan. By exploring these comparisons in detail, you can confidently select the grade that aligns perfectly with your project's performance requirements and financial constraints, a cornerstone of efficient supply chain management.
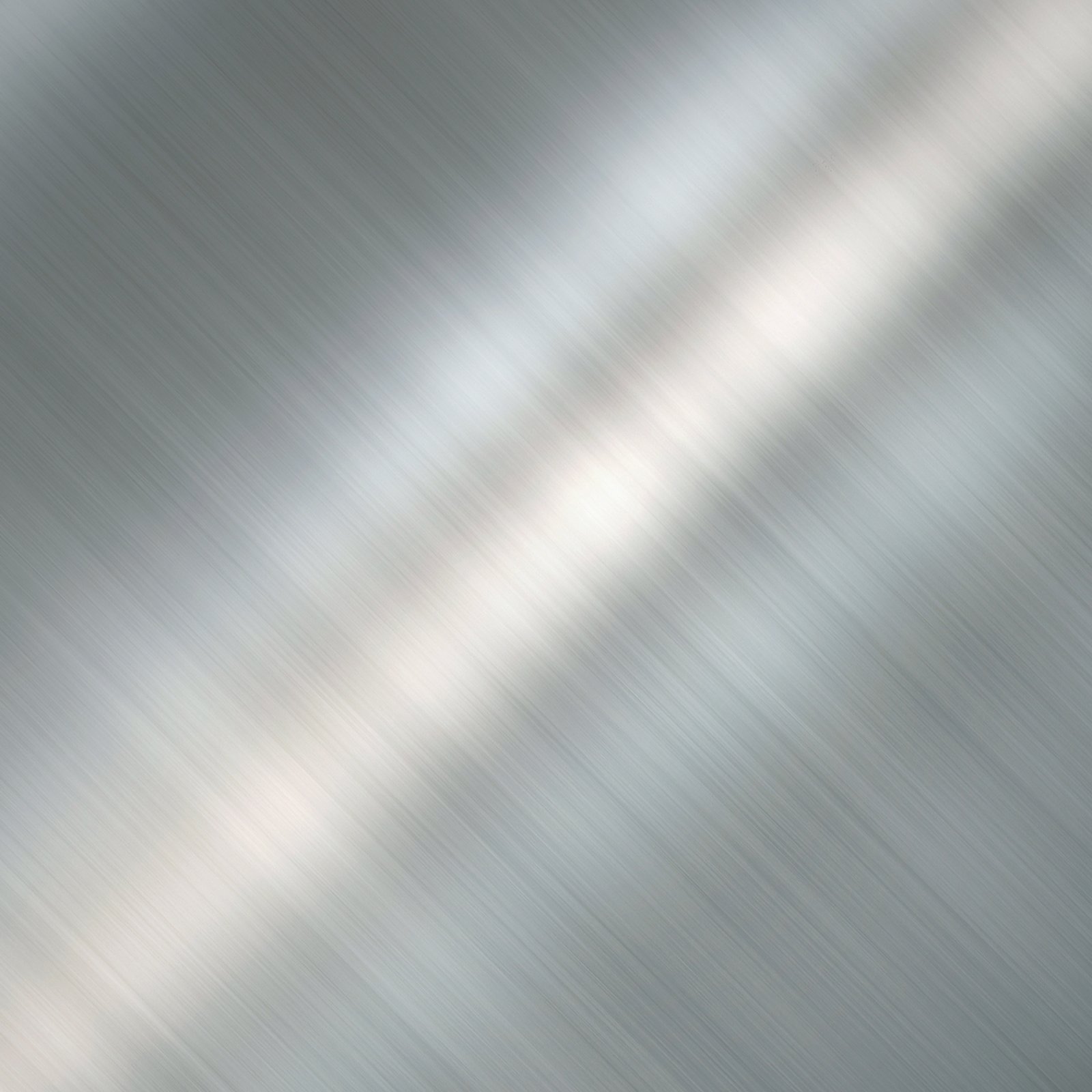
The global stainless steel market is a complex ecosystem where different grades compete for dominance in various applications. At the heart of this competition lies the fundamental trade-off between cost and performance. Grade 304 sits at a strategic crossroads, offering a robust, all-around performance that has made it the industry benchmark. However, relying on a benchmark without understanding its alternatives is a recipe for inefficiency. At MFY, we believe an educated client is our best partner. When a client understands the nuanced differences between 304, 316, 201, and 430, they can make strategic procurement decisions that directly impact their bottom line and product quality. This level of insight transforms the conversation from a simple price negotiation to a collaborative effort to find the most value-driven solution. It’s about empowering our clients to navigate the market with confidence, knowing they have a partner who prioritizes their long-term success over a short-term sale. This collaborative approach is what builds resilient supply chains.
304 vs. 316: The Molybdenum Advantage
The most common comparison in the austenitic family is between 304 and 316 stainless steel. On the surface, they appear similar in terms of strength, formability, and appearance. The critical difference lies in the chemistry: 316 contains 2-3% molybdenum, an element absent in 304. This single addition dramatically enhances its resistance to corrosion, particularly against chlorides and other industrial solvents. This makes 316 the superior choice for marine applications, chemical processing equipment, pharmaceutical manufacturing, and coastal architectural projects where exposure to salt spray is inevitable. A clear example is a project we supplied for an engineering contractor building a chemical storage facility near a port in Southeast Asia. For tanks holding saline solutions and specific acids, 316L was mandatory. However, for structural supports and walkways within the facility but away from direct chemical exposure, 304 provided sufficient corrosion resistance at a significantly lower cost.
This performance boost comes at a price. Molybdenum is a relatively expensive alloying element, making 316 consistently more costly than 304. The price differential can range from 20% to 40%, depending on market conditions. For a purchasing manager at a large manufacturing company, this cost difference is substantial, especially when procuring material in large quantities. The decision, therefore, becomes a clear exercise in risk versus reward. Is the operational environment harsh enough to justify the higher upfront cost of 316? Over-specifying with 316 for a mild-environment application, like indoor decorative paneling or kitchen appliances, is a waste of resources.
Conversely, under-specifying with 304 in a chloride-rich environment is a guarantee of premature failure. We guide our clients through this analysis by examining the specific corrosive agents, their concentrations, and the operating temperatures they will encounter. For instance, while 304 is excellent for dairy processing, the moment cheese production is involved, which uses salt brines, the specification must shift to 316 to prevent pitting corrosion and ensure product purity. This careful, application-specific selection process is fundamental to effective and economical engineering.
304 vs. 201: A Tale of Two Chemistries
The 200 series, particularly grade 201, presents a compelling, lower-cost alternative to 304. The primary difference is in the austenitic stabilizer. In 304, nickel (8-10.5%) serves this role. In 201, a portion of the expensive nickel is replaced by manganese and nitrogen. This substitution successfully creates an austenitic structure but with noticeable trade-offs in performance. Grade 201 has higher work-hardening rates and lower ductility than 304, making it more challenging to deep draw or form into complex shapes. Fabricators must use more powerful equipment and may experience higher tool wear and lower production speeds.
The most significant compromise is in corrosion resistance. With lower chromium (16-18%) and nickel (3.5-5.5%) content, 201 is demonstrably less resistant to corrosion than 304. It is suitable for dry, indoor applications or environments with minimal corrosive exposure. It's often used in developing markets for cost-sensitive items like budget cookware, decorative trim, and some structural components where aesthetics are prioritized over longevity in harsh conditions. We recently consulted with a distributor in India who was considering shifting a significant portion of their kitchenware inventory from 304 to 201 to compete on price. We provided them with comparative salt spray test data, which showed visible rusting on 201 within 24-48 hours, while 304 remained unaffected for over 200 hours.
This data empowered them to create a tiered product strategy. They introduced a budget 201-grade line for price-sensitive customers while continuing to market their 304-grade products as a premium, durable option, complete with clear warranty and care instructions. This prevented them from damaging their brand reputation for quality. The choice between 304 and 201 is a classic example of balancing initial cost against lifecycle value and brand positioning. For any application exposed to moisture, humidity, or food acids, the investment in 304 is almost always justified.
304 vs. 430: Austenitic vs. Ferritic
Shifting away from the austenitic family, a common comparison is with 430, a leading ferritic stainless steel. The fundamental difference is their crystal structure, which makes 430 magnetic, while 304 is non-magnetic. Grade 430 contains chromium but has negligible nickel content, making it significantly cheaper than 304. It offers good corrosion resistance to mild atmospheric conditions and oxidizing substances, making it suitable for applications like automotive trim, refrigerator panels, and restaurant equipment linings where direct food contact is minimal.
However, 430's performance falls short of 304 in several key areas. Its corrosion resistance is lower, and it is not recommended for environments with moderate to high corrosive potential. More importantly, its weldability is limited. Welding 430 can result in a brittle heat-affected zone that is prone to cracking, often requiring pre-heating and post-weld heat treatment to restore ductility, adding complexity and cost to fabrication. Its formability is also less robust than 304's; it doesn't handle deep drawing or aggressive stretching as well.
The table below provides a simplified comparison for quick reference:
Feature | 304 Stainless Steel | 316 Stainless Steel | 201 Stainless Steel | 430 Stainless Steel |
---|---|---|---|---|
Corrosion Resistance | Excellent | Superior (Chloride Resist) | Fair | Good (Mild Atmospheres) |
Cost | Medium | High | Low | Low |
Formability | Excellent | Very Good | Good | Fair |
Weldability | Excellent | Excellent | Good | Fair (Brittle Welds) |
Magnetic | No | No | No | Yes |
The choice between 304 and 430 often depends on the fabrication intensity and the specific environmental exposure. For a client manufacturing commercial kitchen countertops and backsplashes, 304 is the clear winner due to its superior weldability for seamless corners and better resistance to food acids. For a client making decorative panels for washing machines, where cost is a primary driver and welding is not required, 430 is a perfectly viable and economical solution.
304 has better corrosion resistance than 201True
304 contains higher chromium and nickel content (8-10.5%) compared to 201's 3.5-5.5% nickel, making it significantly more corrosion resistant.
316 is always better than 304False
316's molybdenum content is only necessary for chloride-rich environments. For most indoor/dry applications, 304 provides sufficient performance at lower cost.
What are the common applications of 304 stainless steel?
Are you unsure if 304 stainless steel is the right fit for your specific industry or product? Choosing a material that isn't suited for your application's environment can lead to premature failure and costly liabilities. Let’s explore where 304 truly shines and why.
Thanks to its excellent balance of corrosion resistance, formability, and cost, 304 stainless steel applications include kitchen sinks, cookware, food processing equipment, architectural paneling, automotive trim, and chemical tanks.
The ubiquity of 304 across these diverse sectors speaks volumes about its reliability and versatility. As a global supplier, I've seen our 304 coils and sheets transformed into everything from hygienic dairy tanks in India to striking architectural facades in the Middle East. Each application leverages a specific aspect of 304's robust property profile. However, this broad utility doesn't mean it's a one-size-fits-all solution. Understanding the specific demands that each application places on the material is crucial for ensuring its success. For example, the requirements for a food-grade surface are vastly different from those for an automotive exhaust component, even though both might use 304. In the following sections, we will dissect these applications, providing you with the granular insight needed to confidently specify 304 for your projects, ensuring you are leveraging its strengths in the most effective way possible.
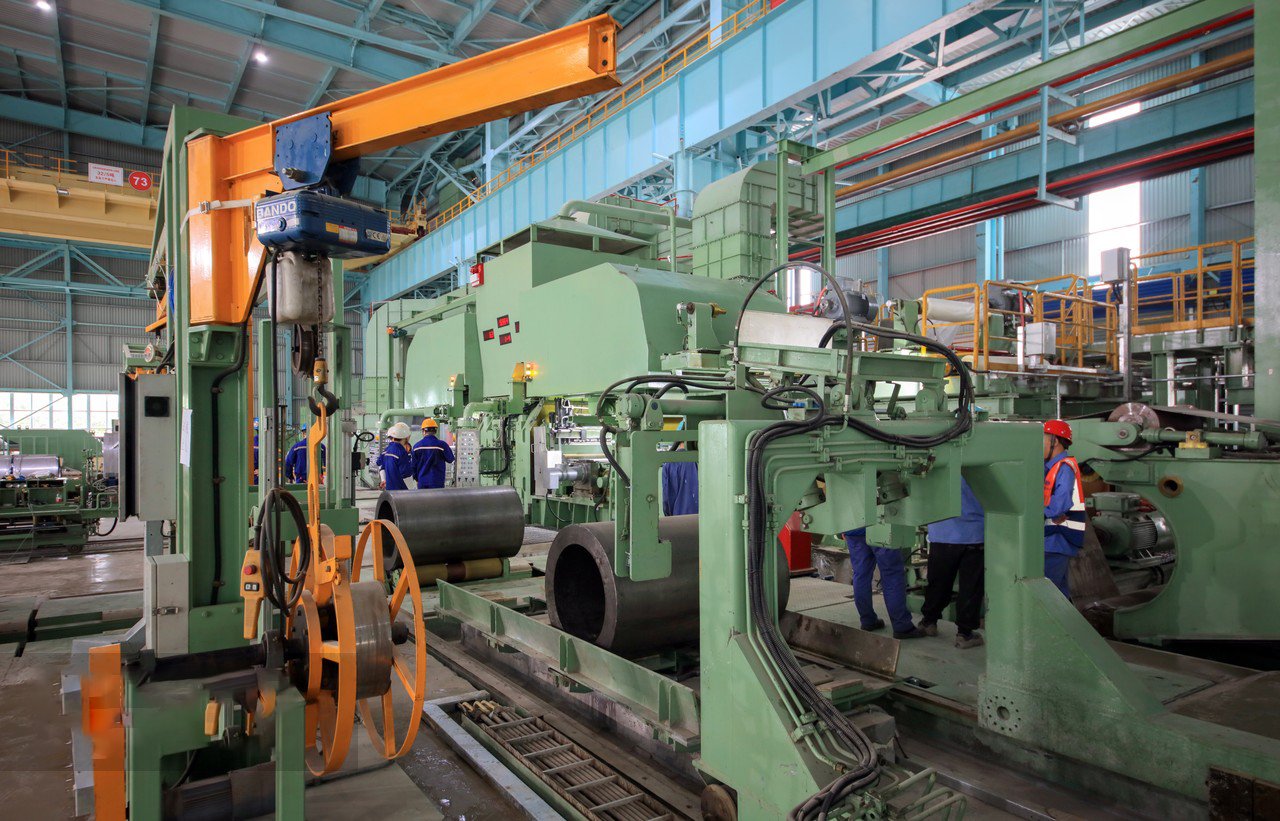
When we look at the global consumption of stainless steel, grade 304's dominance in multiple key sectors is undeniable. This isn't just a matter of happenstance; it's the result of decades of proven performance and a mature, efficient supply chain that MFY is proud to be a part of. For our clients, whether they are large-scale manufacturers or specialized engineering contractors, this means reliability—not just in the material itself, but in its availability and price stability relative to more niche alloys. My experience across different markets, from the rapidly growing industrial hubs of Southeast Asia to the established manufacturing centers in Russia, has shown me that while applications may vary, the fundamental need for a dependable, workable, and cost-effective material is universal. By dissecting the use of 304 in these key industries, we can move beyond a simple list of uses and into a deeper analysis of why it succeeds, providing a strategic framework for your own material selection process.
The Heart of the Home and Commercial Kitchen
One of the most visible applications of 304 stainless steel is in the food and beverage industry. From the humble kitchen sink and cutlery in our homes to the massive vats, piping, and preparation surfaces in commercial kitchens and food processing plants, 304 is the undisputed material of choice. The primary reason is its hygienic properties. The passive chromium-oxide layer creates a smooth, non-porous, and inert surface that is easy to clean and sanitize, preventing bacteria from harboring and growing. It does not impart any flavor or color to the food products it comes into contact with, ensuring product purity. This is a non-negotiable requirement for compliance with food safety standards like those from the FDA and NSF.
We supply a significant volume of 304 sheets with a 2B (smooth, reflective) or #4 (brushed) finish to equipment integrators who manufacture for this sector. A client of ours in Southeast Asia who produces dairy processing equipment—including pasteurizers, tanks, and piping systems—relies on the consistent quality of our 304L grade. The 'L' grade4 is critical here to prevent weld decay, ensuring the welded joints remain as corrosion-resistant as the parent material after fabrication. The cleanability of the finished equipment is paramount for them to prevent batch-to-batch contamination and ensure compliance. Their choice of 304 is a direct reflection of the need for a material that is not only resistant to corrosion from milk (lactic acid) and cleaning chemicals but is also highly formable to create the complex geometries of modern processing equipment.
The material's durability also plays a crucial role. Commercial kitchens are demanding environments with constant thermal cycling, physical impacts, and exposure to a variety of food acids and cleaning agents. 304's toughness and resistance to staining and corrosion ensure a long service life with a pristine appearance, which is important for both hygiene and the professional aesthetic of open-kitchen restaurant designs. The balance of performance and cost makes it accessible for a wide range of products, from high-end professional ranges to everyday cookware, demonstrating its incredible market penetration.
304 is used in food processingTrue
304 stainless steel's hygienic properties make it ideal for food processing equipment as it resists bacterial growth and meets FDA standards.
304 is suitable for coastal buildingsFalse
For coastal areas with salt exposure, 316 stainless steel is recommended instead of 304 to prevent corrosion.
What factors influence the selection of 304 stainless steel in various industries?
Are you basing your material selection solely on past experience or initial cost? Overlooking critical factors like the specific corrosive environment or long-term maintenance can lead to a material choice that is either too expensive or dangerously inadequate. Let's examine the key decision drivers.
The selection of 304 stainless steel is influenced by four main factors: the specific corrosive environment (chemicals, chlorides, temperature), the required mechanical performance (strength, formability), project budget and lifecycle cost, and any applicable industry or regulatory standards (e.g., food-grade).
Balancing these factors is the essence of smart engineering and procurement. As a director at MFY, I’ve seen this decision-making process play out across continents and industries. A construction contractor in a dry, inland region will prioritize cost and formability, making 304 an easy choice. In contrast, an equipment integrator for a pharmaceutical plant must prioritize regulatory compliance and resistance to specific cleaning agents above all else, often necessitating a move to higher grades. Understanding this matrix of influences is not just technical; it's a commercial strategy. It allows you to justify your choice, optimize your budget, and ensure that the material you procure is precisely aligned with the demands of its intended application, thereby minimizing risk and maximizing value for your organization.
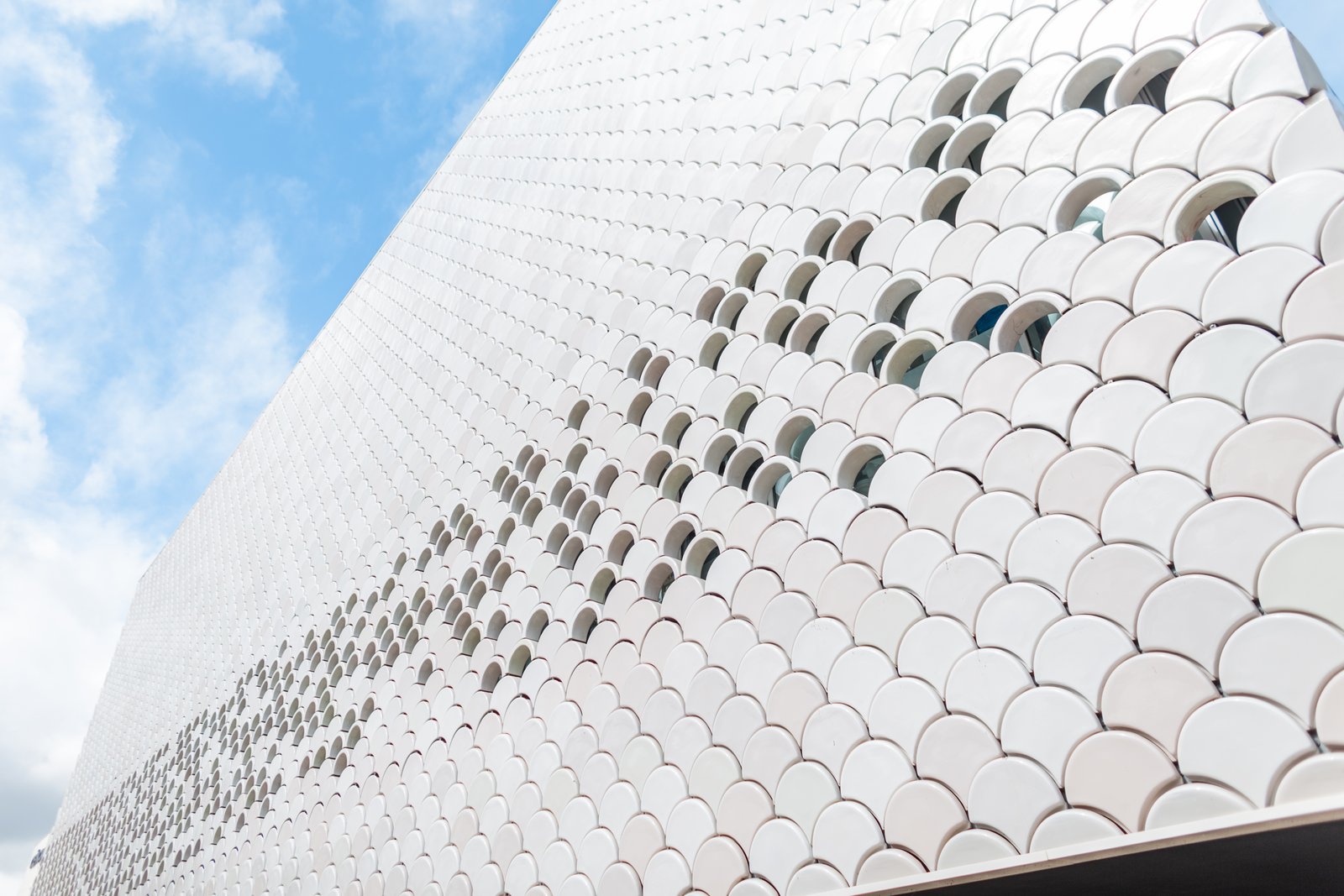
In my global business development role, I’ve learned that material selection is rarely a simple, one-dimensional decision. It's a complex negotiation between engineering requirements, financial constraints, and strategic objectives. 304 stainless steel often emerges as the preferred choice precisely because it offers a favorable outcome in this negotiation for a wide range of scenarios. It represents a point of equilibrium. However, treating it as a default choice without a rigorous evaluation of the influencing factors is a critical error. The most successful manufacturing companies and engineering contractors we partner with are those who approach this decision with diligence. They collaborate with us to analyze their specific context, weighing each factor to arrive at a data-driven conclusion. This analytical rigor is what separates industry leaders from the rest; it's a commitment to optimization that permeates their entire supply chain, starting with the fundamental choice of raw materials.
The Critical Role of the Service Environment
The single most important factor driving the selection of 304 stainless steel5 is the intended service environment. This encompasses the chemical exposure, temperature, and physical conditions the material will face. For any application, the first question must be: "What corrosive agents will the steel come into contact with?" 304 exhibits excellent resistance to a wide array of substances, including most oxidizing acids (like nitric acid), sterilizing solutions, organic chemicals, and foodstuffs. This makes it an immediate candidate for the food processing, beverage, and dairy industries. A client of ours, a large-scale fruit juice producer, uses 304 extensively for their storage tanks and piping precisely because it easily withstands the citric and other fruit acids present in their products.
However, the analysis must go deeper, considering concentration and temperature. A material that is resistant to a chemical at room temperature may corrode rapidly at higher temperatures. As discussed, the most significant environmental limitation for 304 is its susceptibility to chloride ions. Any environment with saltwater, de-icing salts, brine solutions, or certain industrial chemicals like hydrochloric acid will cause pitting and crevice corrosion. We once worked with an equipment integrator building a system for a potato chip manufacturer. While 304 was suitable for most of the line, the section involving the salting process, where salt brine was sprayed at a slightly elevated temperature, required an upgrade to 316 to prevent rapid corrosion and ensure food safety.
This environmental analysis is a core part of our consultative process at MFY. We encourage clients to provide as much detail as possible about their operating conditions. It's not just about selling steel; it's about providing a solution that lasts. By understanding the environment, we can confidently recommend 304 when it's appropriate or advise on a more robust grade when necessary, safeguarding our client's investment and reputation. This diligence prevents costly failures and builds the long-term partnerships that our business is founded on.
Balancing Mechanical Demands and Fabricability
Beyond corrosion resistance, the mechanical properties required by the application are a crucial selection factor. Does the part need to be strong and rigid, or does it need to be formed into a complex shape? 304 stainless steel offers a highly desirable balance: it has good tensile strength for structural integrity while also possessing exceptional ductility and formability. This dual capability is why it's so widely used. Manufacturers of kitchen sinks, for example, choose 304 because it can be deep-drawn into a seamless basin without cracking, a feat that would be impossible with a less ductile material like 430 ferritic steel.
The fabrication process itself is a major consideration. 304's excellent weldability is a significant advantage for projects that require complex assemblies, such as tanks, piping systems, and architectural structures. It can be welded using all standard techniques, and the availability of the low-carbon 304L variant provides a straightforward solution to the risk of weld decay. A manufacturing company client that produces custom-sized chemical holding tanks for various industries relies almost exclusively on 304L plates. The ease of welding reduces their fabrication time and cost, and it simplifies the process of achieving leak-proof, structurally sound seams that will maintain their corrosion resistance over the long term.
Conversely, if an application involves extensive machining, the selection might be more nuanced. While 304 is certainly machinable, its gummy nature and high work-hardening rate mean it's more challenging than plain carbon steels or more free-machining stainless grades (like 303, which has added sulfur). For a client producing high volumes of small, machined fittings, the slower machining speeds and higher tool wear associated with 304 might lead them to consider an alternative. However, for most applications where machining is a secondary process after forming or welding, 304's machinability is perfectly acceptable and is a trade-off worth making for its other superior properties.
Economic Considerations: Upfront Cost vs. Lifecycle Value
Ultimately, business decisions are driven by economics. The selection of 304 is often a pragmatic choice based on its favorable position in the cost-performance spectrum. It provides a significant leap in corrosion resistance and longevity compared to carbon steel or lower-end stainless grades like the 200 series, but without the premium price tag of molybdenum-bearing grades like 316 or other high-performance alloys. For many distributors and traders we work with, 304 represents the "sweet spot" in their inventory, meeting the needs of the broadest segment of their customer base. Its stable and high-volume global production, a chain in which MFY is a key link, also leads to competitive pricing and reliable availability.
A smart procurement strategy, however, looks beyond the initial purchase price per kilogram. It considers the total lifecycle cost of the component. This includes the initial material cost, fabrication costs, maintenance costs over its lifespan, and the potential cost of downtime or replacement if the material fails prematurely. I often walk clients through this calculation. For example, a manufacturer of outdoor electrical enclosures could use a cheaper, painted carbon steel. However, after factoring in the risk of paint scratching, subsequent rust, and the need for eventual replacement, the slightly higher initial investment in 304, which requires virtually no maintenance, often proves to be the more economical choice over a 10- or 20-year period.
This lifecycle value proposition is a powerful argument for 304. It's a story we helped a client in the public infrastructure sector articulate. They were bidding on a project for public benches and waste receptacles. By presenting a lifecycle cost analysis that compared painted steel to 304 stainless steel, they successfully justified the higher upfront cost of 304 by proving it would save the municipality significant money in maintenance and replacement costs over the product's lifespan. This approach shifts the conversation from price to value, a key strategy for any company focused on delivering quality and long-term performance.
304 resists fruit acidsTrue
304 stainless steel is commonly used in fruit juice production because it resists citric and other fruit acids effectively.
304 is chloride-resistantFalse
304 stainless steel is susceptible to pitting corrosion in chloride environments, unlike 316 which contains molybdenum for better chloride resistance.
What are the best practices for working with and maintaining 304 stainless steel?
Have you invested in high-quality 304 stainless steel, only to see it underperform due to improper handling or care? Rust stains, scratches, and contamination can compromise the material's integrity and appearance, negating the very benefits you paid for. Let's establish clear best practices.
Best practices for 304 stainless steel handling involve proper fabrication techniques, such as using dedicated tools to avoid iron contamination, and a routine maintenance schedule. Cleaning with mild soap and water, followed by a clean water rinse, is sufficient for most applications.
Adhering to these guidelines is crucial for maximizing the lifespan and performance of your stainless steel assets. As a supplier, our responsibility extends beyond delivering quality material; it includes empowering our clients with the knowledge to use it correctly. From the factory floor to the final installation, every step matters. We've seen firsthand how simple procedural changes—like implementing a dedicated stainless steel grinding area or a proper cleaning protocol—can dramatically improve outcomes. In the sections ahead, we will detail these fabrication and maintenance procedures, providing you with actionable advice to protect your investment and ensure your 304 stainless steel performs as expected for decades to come.
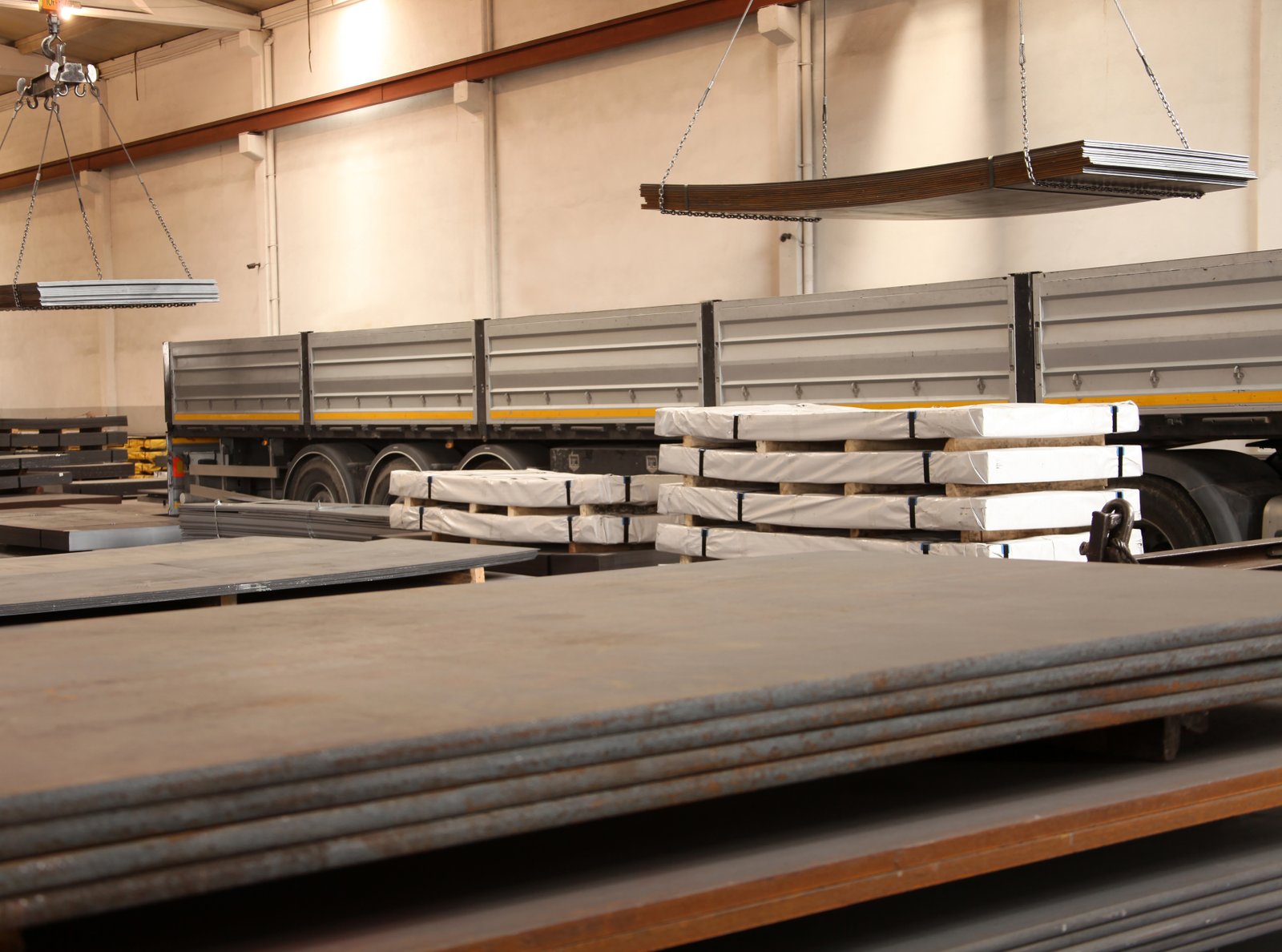
The journey of stainless steel doesn't end when it leaves our facility. Its ultimate success and longevity are determined in the hands of the fabricators, installers, and end-users. At MFY, we see this as a shared responsibility. Providing the highest quality 304 coil, sheet, or pipe is only half the battle. The other half is ensuring our partners have the knowledge to preserve that quality. I have visited client facilities around the world, and the difference between those who get exceptional performance from their 304 and those who struggle with issues like unexpected surface rust almost always comes down to workshop discipline and maintenance protocols. A pristine, high-performance alloy can be compromised in an instant by a contaminated grinding wheel or the use of a harsh, chloride-based cleaner. Therefore, our commitment to our clients includes education on stainless steel care5, transforming a simple supplier-client relationship into a true partnership for quality.
Best Practices in Fabrication and Handling
The foundation for a long-lasting 304 stainless steel product is laid during fabrication. The most critical rule is to prevent iron contamination. Stainless steel's passive layer can be breached if particles of carbon steel are embedded into its surface, leading to localized rust spots that can be mistaken for poor material quality. This contamination often occurs when tools used for carbon steel—such as grinders, wire brushes, cutting discs, and even hammers—are then used on stainless steel. To prevent this, a dedicated set of tools must be used exclusively for stainless steel work. Best-in-class fabrication shops maintain a segregated area for stainless steel work to avoid airborne contamination from carbon steel grinding dust.
Welding, a common fabrication process for 304, requires specific techniques to preserve corrosion resistance. As mentioned, using a low-carbon grade like 304L is the best defense against sensitization and subsequent intergranular corrosion in the heat-affected zone. After welding, proper post-weld cleaning is essential. This involves removing the heat tint or weld scale, which is a thickened, chromium-depleted oxide layer that has inferior corrosion resistance. This can be done mechanically with stainless steel wire brushes (never carbon steel!) or chemically using pickling pastes. A client of ours, a manufacturer of architectural elements in Russia, initially faced issues with rust appearing near welds. After a site visit, we identified their use of shared grinding tools as the culprit. By helping them implement a segregated tooling system and a proper post-weld pickling and passivation procedure, the issue was completely eliminated, restoring the integrity and appearance of their high-end products.
Handling and storage are equally important. Sheets and coils should be stored in a dry, clean environment and kept in their original packaging for as long as possible to protect the surface finish. When handling, operators should use clean gloves to avoid fingerprints, which can become visible after certain processing steps. Using vacuum lifters, nylon slings, or protective films can prevent scratches and dents. These seemingly small details collectively ensure that the material reaches the final stage of its production journey in pristine condition.
Routine Cleaning and Maintenance Protocols
For 304 stainless steel to maintain its signature appearance and corrosion resistance, a simple but consistent cleaning regimen is necessary. The frequency of cleaning depends on the application's environment. For indoor decorative applications or appliances, routine dusting and wiping with a damp cloth may be all that is needed. In more demanding applications, like commercial kitchens or outdoor architectural features, more frequent cleaning is required to remove dirt, grime, and deposits that could trap corrosives against the surface. The golden rule for cleaning is to use the gentlest method that will effectively do the job.
For general cleaning, warm water with a mild soap or detergent is the best choice. Apply with a soft cloth or sponge, wiping in the direction of the polish lines or "grain" of the steel. This helps to avoid disturbing the finish and ensures dirt is lifted from the microscopic grooves. After washing, it is crucial to rinse thoroughly with clean water to remove any remaining soap, and then wipe the surface dry with a soft cloth. Drying is an important step because it prevents water spots, which are mineral deposits left behind as water evaporates. We provide these simple care instructions to all our clients, especially distributors of consumer-facing products like cookware and appliances, to ensure their end-customers are satisfied with the long-term appearance of their purchase.
It's equally important to know what not to use. Harsh abrasives like steel wool or scouring powders should never be used, as they will scratch the surface and can embed iron particles. Cleaners containing chlorides, particularly hydrochloric acid, must be avoided at all costs. This includes many common household cleaners like bleach, which should not be used on 304 stainless steel. If a more stubborn stain appears, such as from grease or oil, a solvent can be used, followed by the standard soap and water cleaning procedure. For light rust stains caused by environmental contamination, a non-chloride cleaner containing oxalic acid can often be used to restore the surface.
Restoring and Protecting the Passive Layer
The passive layer of chromium oxide is the key to stainless steel's performance, and sometimes, it needs to be chemically restored or enhanced. This process is known as passivation. Passivation is a post-fabrication chemical treatment, typically using a nitric acid or citric acid bath, that removes any free iron or other contaminants from the surface and simultaneously thickens the protective passive layer. While a clean, freshly exposed stainless steel surface will passivate itself naturally in the presence of oxygen, this chemical treatment makes the process faster, more uniform, and more effective. It is a common final step for high-purity applications in the medical, pharmaceutical, and semiconductor industries.
We often recommend passivation for clients with demanding applications. For instance, an equipment integrator making components for a water treatment facility was experiencing minor corrosion. Although they were using 304 and following good handling practices, the combination of fabrication stresses and exposure to treated water was challenging the material. We advised them to incorporate a citric acid passivation step into their post-fabrication process. Citric acid is increasingly popular as it is less hazardous than nitric acid. This treatment removed any microscopic contaminants and created a more robust passive film, solving their corrosion issue and increasing the reliability of their equipment.
It's important to distinguish passivation from pickling. Pickling is a more aggressive acid treatment (often using a nitric-hydrofluoric acid mix) used to remove the thick, dark scale that forms during heat treatment or welding. Pickling is a cleaning operation that reveals a fresh surface, which is then typically passivated. Understanding when and how to apply these chemical treatments is an advanced aspect of working with stainless steel, but it is a critical piece of knowledge for ensuring maximum corrosion resistance in challenging environments. As a full-service partner, MFY provides the technical support to help our clients implement these processes effectively and safely.
304 requires dedicated toolsTrue
Using separate tools prevents iron contamination that can cause rust spots on stainless steel.
Bleach is safe for 304False
Chloride-based cleaners like bleach can damage 304 stainless steel's passive layer.
Conclusion
In essence, 304 stainless steel is the industry's workhorse, offering a superb balance of corrosion resistance, formability, and value. By understanding its properties, comparing it to alternatives, and applying best practices in fabrication and maintenance, you can leverage its full potential for lasting performance.
-
Learn why 304 stainless steel is prevalent in various industries due to its versatility ↩
-
Discover how 304 stainless steel dominates global production and supports supply chains efficiently ↩
-
Understand the limitations of 304 stainless steel in chloride-rich environments ↩
-
Learn about the advantages of 304L grade in preventing weld decay in stainless steel ↩
-
Understand how environmental factors impact stainless steel's performance ↩ ↩
Have Questions or Need More Information?
Get in touch with us for personalized assistance and expert advice.