What is a stainless steel coil?
Are you struggling to source the right materials for your projects, feeling overwhelmed by the complexities of stainless steel grades and specifications? This uncertainty can lead to budget overruns and production delays. Understanding the fundamentals of stainless steel coils is the crucial first step toward optimizing your supply chain.
A stainless steel coil is a continuous, long strip of stainless steel that has been wound or coiled after rolling. It serves as a foundational raw material for countless manufacturing and construction applications due to its exceptional corrosion resistance, durability, hygiene, and aesthetic appeal, enabling efficient, large-scale production.
As the Global Business Director for MFY, I’ve seen firsthand how a deeper knowledge of this core material transforms a company's procurement strategy. Moving beyond a simple definition allows you to unlock cost savings, enhance product quality, and build a more resilient supply chain1. It’s not just about buying steel; it’s about making a strategic investment in the foundation of your products.
This material, while seemingly a simple commodity, presents a fascinating duality. On one hand, it's a standardized product traded globally. On the other, the nuances of grade selection, surface finish, and processing can make or break a project's success and profitability. A study by the International Stainless Steel Forum (ISSF) consistently highlights that selecting the appropriate grade can reduce lifecycle costs by up to 40% in corrosive environments. At MFY, our integrated supply chain model is designed specifically to help clients navigate this complexity. We don’t just supply a coil; we provide a comprehensive solution, from raw material sourcing and cold-rolled processing to final delivery, ensuring you get the precise specifications needed for optimal performance.
Background introduction: What is the history and development of stainless steel coils?
Do you view stainless steel as just another modern material? Agitate: Overlooking its century-long evolution means you miss the critical lessons and innovations that define its performance today, potentially leading to misapplication. Solution: Let's explore its history to fully appreciate its capabilities.
The history of stainless steel coils tracks from the discovery of rust-proof iron-chromium alloys in the early 20th century to modern mass production. The development of continuous hot and cold rolling technologies after World War II was the true turning point, making the coil format the global standard for industrial supply.
This journey from a laboratory curiosity to a cornerstone of modern industry is a story I often share with my clients. It’s a narrative of relentless innovation that mirrors the values we champion at MFY: agility, resilience, and continuous evolution. The principles discovered by pioneers like Harry Brearley in 1913 laid the groundwork, but it was the subsequent scaling of production that truly democratized its use. A long-standing distributor partner in India once remarked to me how our digital procurement platform, offering real-time tracking and quality certificates, felt like science fiction compared to the stacks of paper and uncertain lead times he managed just fifteen years ago. This evolution from manual, localized supply to a transparent, globalized network is a direct continuation of the industry's innovative spirit. We aren’t just part of the stainless steel supply chain; we see ourselves as custodians of its legacy, pushing it forward with technology to solve modern challenges for our clients in manufacturing, construction, and beyond. This historical context isn't just academic—it's the foundation upon which trust and quality are built in our industry.
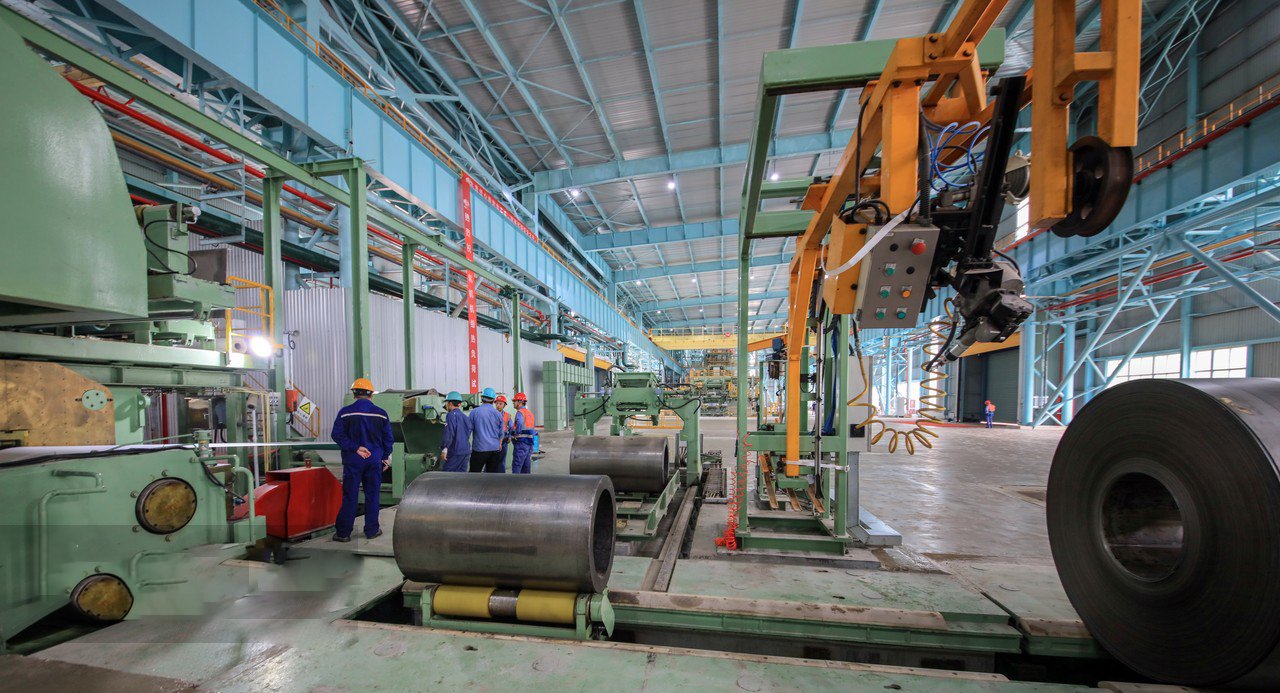
The evolution of stainless steel from a niche alloy to a global commodity is a powerful story of scientific discovery meeting industrial demand. Understanding this trajectory helps clarify why certain grades and forms exist and how they are best utilized today. At MFY, we believe that appreciating this history allows our clients to make more informed decisions, not just about the material itself, but about the long-term value it brings to their projects. This historical perspective is woven into our consultative approach, ensuring the solutions we provide are grounded in a century of material science excellence.
The Genesis of an Alloy: Early Discoveries
The birth of stainless steel wasn't a single event but a series of discoveries across Europe in the early 1900s. While several researchers were experimenting with chromium-steel alloys, it was Harry Brearley of Sheffield, England, who, in 1913, is credited with discovering a "rustless" steel while seeking a more erosion-resistant alloy for gun barrels. He noticed that his 12.8% chromium iron samples did not corrode after being exposed to the elements. This fundamental discovery—that a sufficient amount of chromium (typically above 10.5%) creates a passive, self-repairing oxide layer on the steel's surface—remains the core principle of all stainless steels today.
Initially, the applications were limited. The first major commercial use was in cutlery, which, while successful, hardly hinted at the material's future potential. The primary challenges in these early days were the high cost of chromium and the difficulty in producing the alloy consistently. Early 20th-century steel production was a fraction of today's output, and creating these specialized alloys was an art as much as a science. These initial hurdles meant that for decades, stainless steel remained a specialty material, used only where its anti-corrosive properties were absolutely essential and worth the premium price.
This foundational period established the core value proposition of stainless steel. The lessons learned about the critical role of chromium and the challenges of consistent production paved the way for future innovations. It was this initial focus on quality and specific performance characteristics that set the stage for the highly specialized and reliable material we know today. At MFY, we honor this legacy by maintaining rigorous quality control throughout our integrated production process, from raw material trading to final coil processing.
Post-War Industrialization and the Rise of Coils
The true industrial ascent of stainless steel began in the post-World War II era. The demands of the war had spurred massive advancements in metallurgy and manufacturing technology. Chief among these were the development and refinement of continuous hot-strip mills and, subsequently, cold-rolling techniques. This was the pivotal innovation that allowed for the production of long, thin, uniform sheets of steel that could be efficiently wound into large, heavy coils. Before this, steel was primarily produced in individual plates or bars, a much slower and less scalable process.
The coil format was a revolution. For industries like automotive manufacturing and home appliances, it meant a continuous supply of raw material that could be fed directly into stamping and forming lines, drastically increasing production speed and reducing waste. I recall a story from a client whose family founded a kitchenware manufacturing business in the 1960s. He described how the switch from buying individual stainless steel sheets to purchasing coils transformed their factory overnight, enabling them to compete on a national scale for the first time. This shift is what made the widespread use of stainless steel in products like kitchen sinks, washing machine drums, and decorative trim economically viable.
This era cemented the stainless steel coil as the primary delivery form for flat-rolled products. It wasn't just a change in shape; it was a fundamental change in the economics of manufacturing. The availability of coils drove innovation in downstream processing and fabrication, creating a virtuous cycle of growth. This history underscores why MFY has invested so heavily in our cold-rolling and processing facilities. By controlling this critical stage of the supply chain, we provide our clients with the same efficiency and scalability benefits that first propelled the industry forward over 70 years ago.
The Modern Era: Globalization and Specialization
The last few decades have been characterized by two parallel trends: the proliferation of specialized grades and the globalization of the supply chain. As technology advanced, so did the ability to fine-tune the composition of stainless steel, adding elements like nickel, molybdenum, and titanium to achieve specific properties. This led to the development of hundreds of different grades, each optimized for a particular environment, from the standard austenitic Grade 304 to the highly corrosion-resistant duplex grades used in marine and chemical processing applications.
This specialization created a new challenge: complexity. For an engineering contractor in the Middle East or a distributor in Southeast Asia, navigating this vast landscape of grades, finishes, and international standards can be daunting. This is where the globalization of the supply chain, powered by technology, has become critical. At MFY, we have built our business model to address this exact issue. Our digital platforms and expert teams act as a bridge, connecting our clients to a global network of supply while simplifying the procurement process. We help them select the precise grade and finish for their application, ensuring both performance and cost-effectiveness.
The table below illustrates a simplified overview of how different grades, which became more distinct in this modern era, are suited for various historical and current applications, a common point of discussion I have with new clients.
Grade | Key Elements | Key Properties | Typical Applications |
---|---|---|---|
430 | Cr | Good corrosion resistance, formability, magnetic | Automotive trim, indoor decorative, kitchen utensils |
304 | Cr, Ni | Excellent corrosion resistance, non-magnetic | Food processing equipment, kitchen sinks, architectural |
316L | Cr, Ni, Mo | Superior corrosion/pitting resistance, low carbon | Chemical processing, marine hardware, medical implants |
Duplex 2205 | Cr, Ni, Mo, N | Very high strength, excellent chloride resistance | Oil & gas pipelines, chemical tankers, bridges |
This modern era of specialization, supported by a resilient and digitally integrated global supply chain, is where MFY thrives. Our vision is to be the leading service brand in this space, using our fully integrated capabilities—from raw material sourcing to rapid export delivery—to empower our clients to build, create, and innovate with the remarkable material that is stainless steel.
Stainless steel coils are foundational for manufacturingTrue
Stainless steel coils serve as essential raw materials for various industries due to their durability and corrosion resistance.
Stainless steel was invented in the 1800sFalse
Stainless steel was discovered in the early 20th century, with Harry Brearley's work in 1913 being a key milestone.
Current situation analysis: How are stainless steel coils used in today's industries?
Do you only associate stainless steel with kitchen sinks? Agitate: This narrow perspective means you're likely missing opportunities to leverage its versatility in more demanding and profitable applications. Solution: Understand the full scope of its use across today's most critical industries.
Today, stainless steel coils are indispensable across a vast industrial landscape. They are fabricated into structural components for buildings, sterile equipment for hospitals, high-performance parts for automobiles, and durable tanks for the chemical and food processing industries, prized for their unmatched versatility and lifecycle value.
The sheer breadth of applications never ceases to amaze me. In a single day, I might speak with an engineering contractor in Russia about coils for a new bridge, a manufacturer in Southeast Asia developing a new line of high-end appliances, and a distributor supplying to the booming construction market in the Middle East. Each client has unique demands, yet the stainless steel coil is the common thread. Recently, a client in the food processing sector came to us for Grade 304L coils for storage tanks. After discussing their new product line, which involved more acidic ingredients, we guided them toward Grade 316L. This small change, based on a deeper application knowledge, prevented potential corrosion issues and saved them from a costly product recall down the line. This is the partnership we strive for at MFY—moving beyond a transactional sale to provide solutions that enhance our clients' products and protect their reputations. Our integrated supply chain ensures we can deliver these specific grades reliably, anywhere in the world.
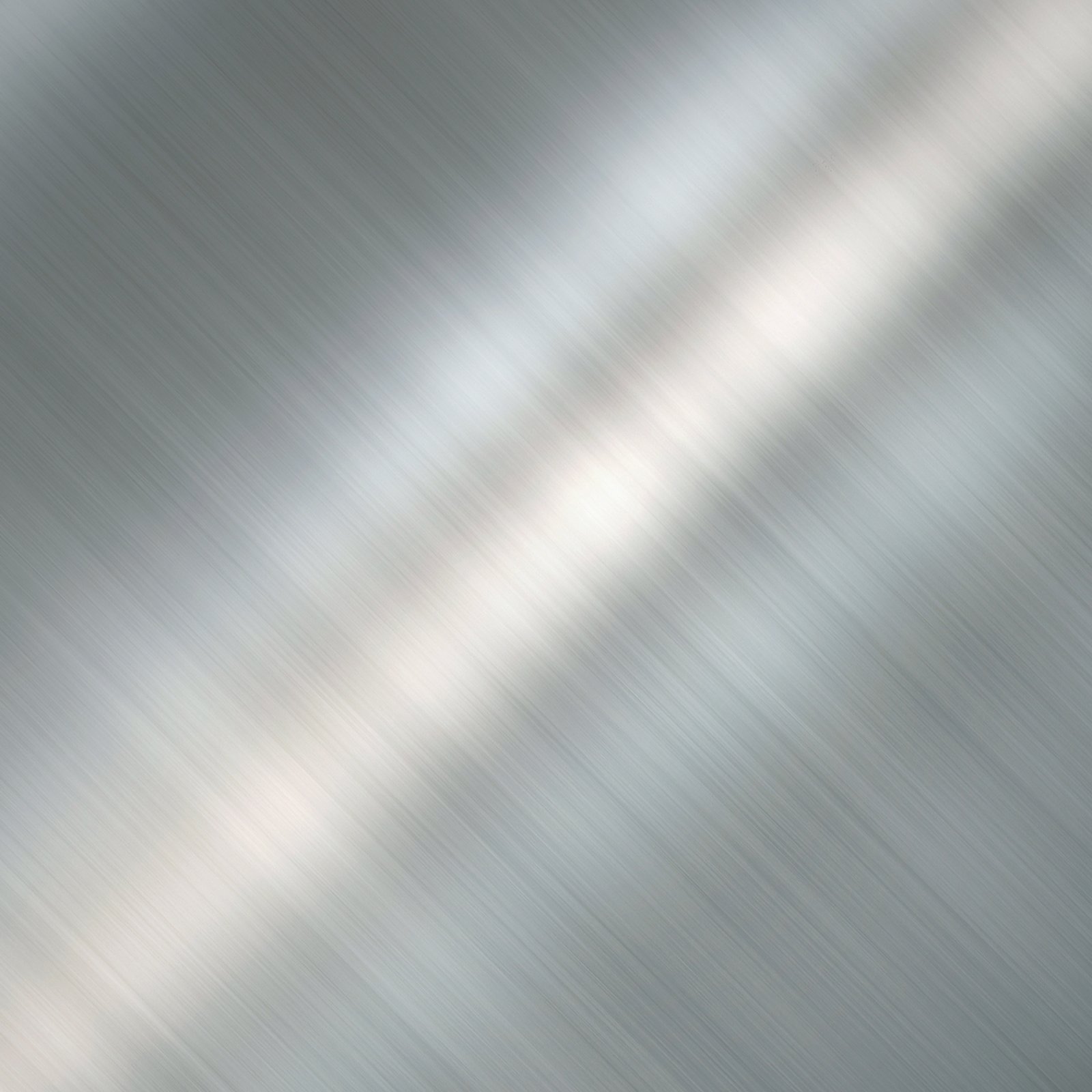
The modern industrial landscape is built, quite literally, on materials that can withstand the tests of time, environment, and intensive use. Stainless steel, delivered in the efficient coil format, has become a hero material in this context. Its applications are not just widespread; they are often critical. From ensuring the safety of our food supply to enabling architectural marvels, the impact of the humble stainless steel coil2 is profound. At MFY, being at the heart of this supply chain gives us a unique perspective on how this material is driving progress across the globe.
The Backbone of Manufacturing and Consumer Goods
In the realm of manufacturing, stainless steel coils are the starting point for a staggering array of products that touch our daily lives. The automotive industry, for example, relies heavily on them for exhaust systems, catalytic converters, and structural components where resistance to heat, corrosion, and vibration is paramount. According to industry reports, an average car can contain 15-20 kg of stainless steel, a figure that is growing with the demand for longer-lasting vehicles. The choice of finish is critical here; a bright annealed (BA) finish3 might be used for visible trim, while a standard 2B finish is sufficient for under-body parts.
The home appliance and consumer goods sector is another dominant user. The hygienic properties, ease of cleaning, and sleek appearance of stainless steel make it the premier choice for refrigerator doors, oven fronts, washing machine drums, and high-end cookware. I recently worked with a large appliance manufacturer who was facing challenges with formability on their deep-drawing press lines. By working with our technical team and adjusting the cold-rolling parameters, we were able to supply coils with enhanced ductility, reducing their rejection rate by over 15% and significantly boosting their production efficiency.
This sector demonstrates the importance of both aesthetics and functionality. The material must not only perform flawlessly for years but also meet the design expectations of modern consumers. MFY's ability to produce coils with a wide variety of finishes and precise mechanical properties allows our manufacturing clients to innovate and compete effectively in a crowded marketplace, turning a raw material into a signature feature of their brand.
Engineering and Construction Marvels
Within engineering and construction, stainless steel coils are specified for projects where longevity and structural integrity are non-negotiable. Its superior strength-to-weight ratio and exceptional corrosion resistance make it an ideal choice for landmark architectural projects, from curtain walls and roofing to intricate facades like that of the Walt Disney Concert Hall. In these applications, the material is not just structural; it's a core part of the aesthetic vision, chosen for its ability to maintain its appearance over decades with minimal maintenance.
I take great pride in MFY's role in such projects. A compelling case was a large infrastructure project on the coast of the UAE, where our client, a major construction contractor, was building a series of pedestrian bridges. The saline, humid environment demanded a material that could resist chloride-induced pitting corrosion. We supplied them with Duplex 2205 stainless steel coils, a grade specifically designed for such harsh conditions. Our integrated logistics ensured a phased delivery schedule that matched their construction timeline perfectly, preventing costly on-site storage issues and project delays. The lifecycle cost analysis for this project showed that despite a higher initial investment, the duplex stainless steel would be 30% cheaper over a 50-year lifespan compared to coated carbon steel due to the elimination of maintenance and repainting costs.
From structural supports and rebar in corrosive environments to heavy-duty industrial flooring and cable trays, stainless steel provides a "fit and forget" solution. It ensures the safety and durability of the infrastructure that underpins our economies. Our role at MFY is to ensure that contractors and engineers have reliable access to these high-performance materials, backed by the technical data and supply chain certainty needed to build with confidence.
Critical Applications in Process Industries
The process industries—namely chemical, pharmaceutical, and food and beverage—operate under the most stringent standards of safety and hygiene, and stainless steel is the material of choice. In these sectors, the primary concern is non-reactivity. The material must not corrode, leach metallic ions, or harbor bacteria, any of which could contaminate the final product. Austenitic grades like 304L and 316L are ubiquitous, used to construct everything from massive chemical reactors and storage tanks to intricate piping systems and clean-in-place (CIP) equipment.
The regulatory environment is a major driver of material selection. For an equipment integrator client designing a pharmaceutical-grade mixing vessel, full material traceability is not a preference; it's a legal requirement mandated by bodies like the FDA and EMA. They need to know the exact origin and composition of the steel. MFY provides comprehensive Mill Test Certificates (MTCs) with every coil, offering the granular data our clients need to satisfy audits and ensure compliance. We helped this particular client select the 316L grade and a specific polished finish to exceed sanitary standards, preventing biofilm attachment and ensuring product purity.
The following table shows a basic comparison of common grades used in these sensitive industries, a frequent topic of technical consultation with our clients.
Feature | Grade 304/304L | Grade 316/316L |
---|---|---|
Primary Use | General purpose, food contact | Pharmaceutical, chemical, high-purity |
Corrosion Resistance | Good | Excellent, especially against chlorides |
Composition | 18% Cr, 8% Ni | 16-18% Cr, 10-14% Ni, 2-3% Mo |
Cost Factor | Base | ~20-30% Higher than 304 |
In these critical applications, there is no room for error. The material must be perfect. MFY's investment in state-of-the-art production and quality assurance is a direct response to this need. We act as a trusted partner to equipment integrators and facility owners, providing the certified, high-purity stainless steel coils that form the bedrock of safe and efficient process manufacturing.
Stainless steel is used in car exhaust systemsTrue
Stainless steel's heat and corrosion resistance make it ideal for automotive exhaust components.
Grade 304L is best for acidic food storageFalse
Grade 316L with molybdenum content is superior for acidic applications as it resists corrosion better.
Challenges analysis: What are the common challenges faced in using stainless steel coils?
Think using stainless steel is straightforward? Agitate: Underestimating its complexities can lead to unexpected failures, budget blowouts, and supply chain disruptions that jeopardize your entire operation. Solution: Acknowledge and prepare for the common challenges before they arise.
Common challenges in using stainless steel coils include navigating extreme price volatility, selecting the correct grade for specific corrosive environments, and managing technical issues during fabrication like welding and forming. Overcoming these requires deep market insight, technical expertise, and a resilient supply chain partner.
These are not theoretical problems; they are daily realities for my clients and for us at MFY. I once had a client, an equipment manufacturer for the marine industry, who was facing weld decay in their 304-grade components4. The issue was post-weld corrosion along the seams, a classic case of sensitization. They were on the brink of a costly recall. After analyzing the application, which involved saltwater exposure, we helped them transition to Grade 316L. The lower carbon content of "L" grade minimizes carbide precipitation during welding, and the added molybdenum provides the necessary chloride resistance. By addressing the root cause—improper grade selection—we not only solved the immediate technical crisis but also helped them build a more durable and reputable product. This experience highlights how the initial choice of a coil has profound downstream consequences.
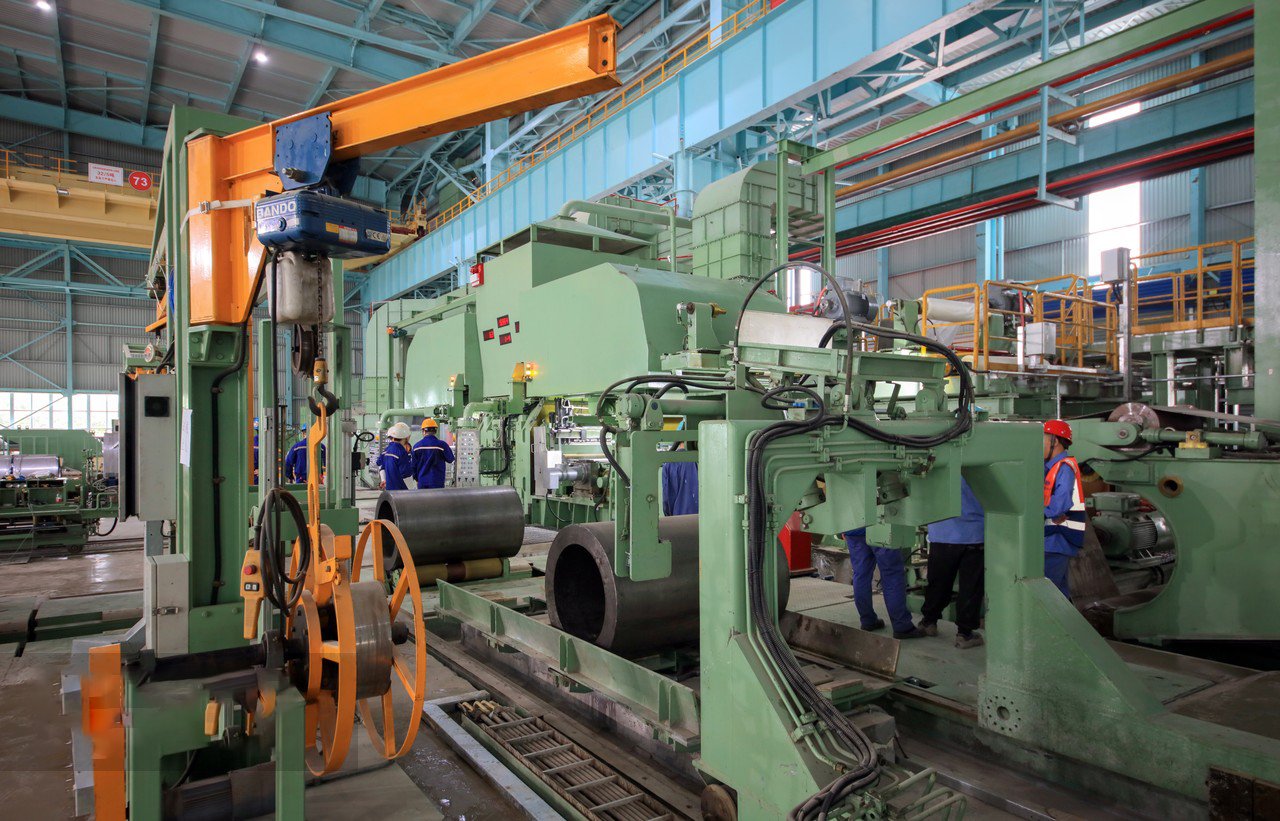
While stainless steel offers unparalleled benefits, its path from coil to finished product is paved with potential pitfalls. These challenges are not reasons to avoid the material, but rather a call for greater diligence, expertise, and strategic partnership. An effective procurement strategy is not just about finding the lowest price; it is about mitigating risk. At MFY, our entire business model, from our market intelligence teams to our in-house technical experts and robust inventory, is structured to help our clients anticipate and overcome these very challenges, turning potential liabilities into competitive advantages.
Navigating Price and Supply Chain Volatility
One of the most significant challenges for any business relying on stainless steel is the inherent volatility of its price. The cost of a stainless steel coil is directly tied to the fluctuating global market prices of its primary alloying elements, namely nickel and chromium, which are traded as commodities on exchanges like the London Metal Exchange (LME)5. Sudden geopolitical events, changes in mining output, or shifts in global demand can cause prices to swing dramatically in a matter of weeks, making long-term project budgeting and stable costing incredibly difficult for manufacturers and contractors.
This volatility creates a constant dilemma for procurement managers: buy now and risk a price drop, or wait and risk a sharp increase? A client in the construction sector shared a story of how a sudden 20% spike in the nickel price nearly derailed a major project's profitability because their initial bid was based on outdated material costs. This is where a strategic supply partner becomes invaluable. At MFY, our raw material trading division constantly monitors these markets, leveraging market intelligence and bulk purchasing power to help buffer our clients from the worst of this volatility. We offer flexible pricing mechanisms and forward-contracting options that allow our clients to lock in costs and ensure budget certainty.
Beyond price, supply chain reliability itself can be a challenge. Port congestion, shipping container shortages, or unforeseen production disruptions can lead to significant delays. MFY mitigates this risk through its integrated model. By controlling production, maintaining a strong inventory of common grades, and managing our own logistics and warehousing, we create a more resilient and predictable supply chain. We provide our clients with the stability they need to operate confidently, even in an unstable global market.
The Critical Task of Grade Selection
Choosing the wrong grade of stainless steel is one of the most common and costly mistakes in the industry. With hundreds of available grades, each with a unique profile of corrosion resistance, strength, heat resistance, and cost, the selection process can be overwhelming. A choice made on the basis of upfront cost alone can lead to premature failure, safety hazards, and significant financial losses. For example, using a standard Grade 304 in a coastal or chemical-rich environment where Grade 316 or a duplex steel is required will inevitably lead to pitting corrosion and structural failure.
The complexity of this decision is a recurring theme in my conversations with clients. I worked with an engineering firm designing a new food processing plant. They were initially leaning towards using Grade 304 throughout to save costs. However, our technical team analyzed their process, which involved processing brines and acidic sauces. We presented them with corrosion rate data showing that 304 would have a service life of less than five years, while 316L would last for over 20. The evidence was clear. The slightly higher initial investment in 316L would provide a vastly superior lifecycle value and prevent costly downtime and replacement.
This is why MFY positions itself as a consultative partner. We believe it is our responsibility to ensure our clients have the right material for the job. Our team of metallurgists and engineers works alongside our clients' design teams to analyze the service environment, mechanical requirements, and regulatory standards. We provide the data, case studies, and expert guidance necessary to make an informed decision, moving the conversation from "what is the cheapest option?" to "what is the best solution?" This collaborative approach prevents failures and ultimately builds more successful, long-term partnerships.
Overcoming Fabrication and Processing Hurdles
The journey of a stainless steel coil does not end upon delivery; it is just beginning. The subsequent fabrication processes—such as welding, forming, machining, and finishing—each present their own set of technical challenges that can impact the final quality and performance of the material. For instance, welding stainless steel requires careful control of heat input to avoid issues like sensitization (weld decay), distortion, or cracking, especially in thicker sections. Each grade has its own unique welding characteristics, requiring specific filler materials and techniques.
Formability is another critical concern. I often speak with manufacturers who struggle with cracking or excessive "springback" when stamping complex parts from stainless steel coils. These issues can stem from improper grade selection, inconsistent material properties within a coil, or an incorrect processing setup. A client in the automotive components sector was experiencing a high failure rate when deep-drawing a particularly complex part. Our technical team analyzed their process and the material specifications. We discovered that by supplying a coil with a specific, highly controlled grain size and tensile strength—achieved through precise adjustments in our cold-rolling mill—we could significantly improve its ductility and formability. This technical intervention led to a direct improvement in their production yield.
The table below outlines some common fabrication challenges and the corresponding considerations MFY helps its clients address.
Fabrication Process | Common Challenge | MFY's Approach / Solution |
---|---|---|
Welding | Weld decay (sensitization), distortion | Recommend low-carbon ("L") grades, advise on heat input control, provide appropriate filler material guidance. |
Forming/Stamping | Cracking, springback, wrinkling | Supply coils with optimized and consistent mechanical properties (e.g., high formability, specific tensile strength). |
Machining | Poor tool life, work hardening | Advise on grades with improved machinability (e.g., those with sulfur additions like 303), recommend appropriate speeds and feeds. |
Finishing/Polishing | Inconsistent surface appearance | Provide coils with high-quality, uniform surface finishes (e.g., 2B, BA) as a starting point, reducing downstream polishing effort. |
These fabrication hurdles underscore the fact that supplying a coil is only half the battle. True partnership involves providing the downstream technical support to ensure the material can be used successfully. At MFY, our commitment extends beyond the point of sale. Our deep manufacturing expertise, integrated into our supply chain, means we understand these challenges intimately and can proactively help our clients overcome them.
316L resists chloride corrosionTrue
316L stainless steel contains molybdenum which provides superior resistance to chloride-induced pitting corrosion compared to 304 grade, making it ideal for marine environments.
Price volatility only affects nickelFalse
Stainless steel price volatility stems from multiple alloying elements including both nickel and chromium, along with other market factors like supply chain disruptions and geopolitical events.
Response strategies: How can industries overcome the challenges of using stainless steel coils?
Are you reactive, only dealing with stainless steel challenges as they arise? Agitate: This firefighting approach leads to constant stress, project delays, and eroded profits. Solution: Adopt proactive strategies to turn these challenges into sources of competitive advantage.
Industries can overcome stainless steel challenges by forging strategic partnerships with integrated suppliers like MFY steel suppliers, leveraging market intelligence for procurement, and investing in technical education for their teams. This proactive approach transforms material sourcing from a simple transaction into a strategic business function.
This strategic shift is the core of my message to clients. The old model of simply sending out a request for quotation to the cheapest supplier is broken. It ignores risk, quality, and long-term value. I recently onboarded a new client, a large distributor, who was constantly plagued by inconsistent quality from a rotating cast of suppliers. By partnering with MFY, they gained a single point of accountability. Our integrated quality control, from melt shop to final coil, gave them the product consistency they needed. Furthermore, our market reports and dedicated account management helped them plan their inventory more strategically, improving their cash flow and ability to respond to their customers' needs. They didn't just buy steel from us; they outsourced their supply chain risk, allowing them to focus on growing their business.
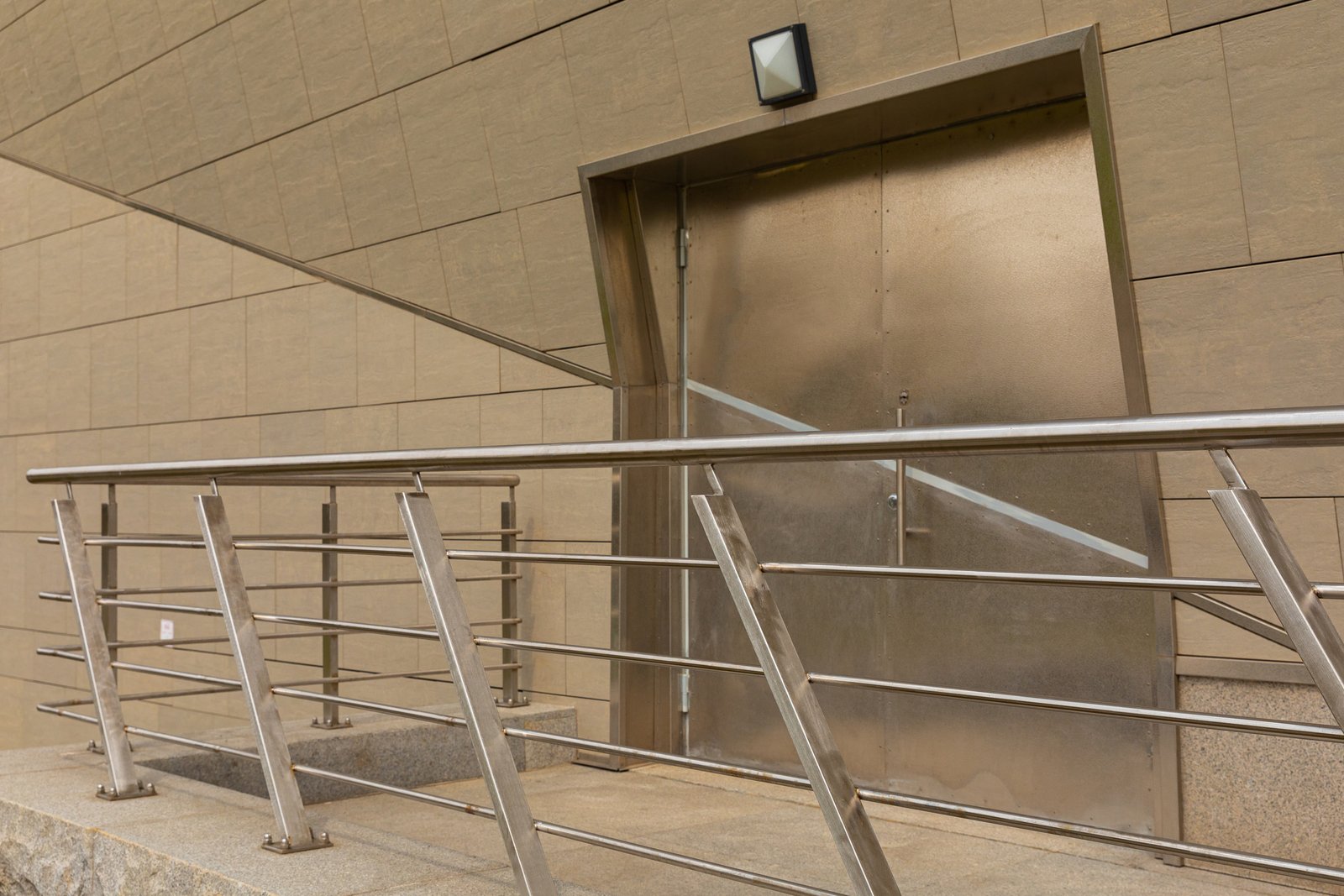
Thriving in the modern industrial landscape requires resilience and foresight. The challenges associated with stainless steel—volatility, technical complexity, and fabrication hurdles—are significant, but they are not insurmountable. The key is to move from a tactical, price-driven procurement model to a strategic, value-driven partnership approach. By doing so, companies can not only mitigate risks but also unlock new efficiencies and innovations. At MFY, we have built our company around being this strategic partner, offering integrated solutions that address these challenges head-on.
Forging Strategic Supply Chain Partnerships
The single most effective strategy for overcoming the challenges of using stainless steel is to move away from transactional purchasing and build a deep, strategic partnership with an integrated supplier. A true partner does more than just deliver a coil; they offer a holistic solution that encompasses market intelligence, technical expertise, inventory management, and logistical support. This changes the dynamic from a simple buyer-seller relationship to a collaborative one, where the supplier is an extension of the client's own team, invested in their success.
Consider the challenge of price volatility. An arm's-length supplier has little incentive to help you manage this risk. A strategic partner like MFY, however, works proactively with you. We provide clients with regular market analysis and forward-looking forecasts6, allowing them to make more informed purchasing decisions. For a large manufacturing client with predictable annual consumption, we can structure a long-term agreement with fixed or formula-based pricing, effectively removing market volatility from their budget and allowing them to quote their customers with confidence. This level of collaboration is only possible through a deep, trust-based relationship.
Furthermore, a partner with an integrated supply chain offers unparalleled reliability. Because MFY controls key production stages, from cold-rolling to tubing, and manages extensive warehousing, we can provide a buffer against external disruptions. When a port strike or a mill shutdown occurs, our clients are better insulated from the fallout because we have the inventory and production flexibility to adapt. This integration transforms the supply chain from a source of risk into a source of competitive advantage.
Leveraging Technical Expertise and Education
Successfully using stainless steel demands technical knowledge. Overcoming challenges in grade selection and fabrication requires a commitment to education and leveraging the expertise of your partners. The most successful companies I work with are those who empower their engineers, designers, and procurement teams with a deep understanding of the material they are working with. This knowledge prevents costly errors and unlocks opportunities for innovation.
A strategic supplier should be a primary source of this technical education. At MFY, we see this as a core part of our value proposition. We regularly host workshops and webinars for our clients on topics like "Selecting the Right Grade for Corrosive Environments" or "Best Practices in Stainless Steel Welding." When a client, an equipment integrator, was developing a new product for a highly specialized chemical process, our metallurgists worked with their R&D team for weeks. We provided material samples for testing, analyzed corrosion data, and helped them write the final material specification. This collaborative effort ensured they selected the optimal, most cost-effective material, preventing a potential product failure.
Investing in this knowledge base internally, supported by a technically proficient supplier, pays dividends. It allows teams to design better products, optimize manufacturing processes, and troubleshoot problems more effectively. It shifts the conversation from a reactive "Why did this fail?" to a proactive "How can we make this better?" MFY encourages this by providing accessible, expert support, ensuring our clients feel confident in every decision they make regarding our materials.
Implementing Proactive Procurement and Inventory Models
A final key strategy is to adopt a more sophisticated and proactive approach to procurement and inventory management. Instead of ordering on a just-in-time basis and being exposed to every market shock, companies can work with their supply partners to develop models that balance cost, availability, and risk. This requires transparency and data sharing between the client and the supplier to create a more efficient and resilient system.
One such model is a vendor-managed inventory (VMI) program. For a high-volume distributor client in Southeast Asia, we implemented a VMI system for their most common stainless steel sheet and coil grades. Based on their sales data and our shared forecast, MFY manages an agreed-upon level of inventory at a nearby warehouse. This ensures they always have stock to meet immediate customer demand without tying up their own capital in excess inventory. It smooths out the impact of shipping delays and price fluctuations while dramatically improving their service level.
The table below contrasts a traditional procurement model with a strategic, proactive one.
Aspect | Traditional Procurement Model | Strategic Partnership Model (e.g., with MFY) |
---|---|---|
Supplier Relationship | Transactional, adversarial (price-focused) | Collaborative, long-term (value-focused) |
Pricing Strategy | Spot market, high volatility exposure | Hedging, forward contracts, formula-based pricing |
Inventory Strategy | Just-in-time (JIT), high risk of stock-outs | Vendor-managed inventory (VMI), safety stock, consignment |
Technical Support | Minimal to none | Integrated, consultative, pre- and post-sale support |
Overall Goal | Lowest unit price | Lowest total cost of ownership, risk mitigation |
By embracing these more advanced procurement and inventory strategies, companies can fundamentally change their relationship with their stainless steel supply chain. It becomes less of a cost center to be minimized and more of a strategic asset to be optimized. This proactive stance, built on the foundation of a strong supplier partnership, is the ultimate key to overcoming the inherent challenges of the industry.
Strategic partnerships reduce supply chain risksTrue
Integrated suppliers like MFY provide quality control and market intelligence that help mitigate risks associated with stainless steel procurement.
Price is the only factor in procurementFalse
Strategic procurement considers total cost of ownership, including quality, reliability, and technical support, not just unit price.
Technical advice: What are some technical recommendations for optimizing the use of stainless steel coils?
Are you applying generic steel-working rules to stainless steel? Agitate: This mistake leads to suboptimal results, including corrosion, tool wear, and aesthetic flaws, negating the very benefits you paid for. Solution: Follow specific technical recommendations to unlock its full performance potential.
To optimize stainless steel coil use, always ensure proper grade-specific fabrication techniques, maintain meticulous cleanliness to preserve the passive layer, and implement correct storage and handling protocols. These technical details are critical for maximizing the material's longevity, performance, and aesthetic integrity in any application.
This advice is born from years of troubleshooting client issues. A classic example I often share involves a manufacturer of architectural panels who was seeing small rust spots appear on their finished 304-grade products7 after installation. The problem wasn't the steel itself; it was contamination. Their workshop also handled carbon steel, and tiny iron particles had become embedded in the stainless surface during fabrication, creating sites for galvanic corrosion. We advised them to implement dedicated stainless-only tooling, grinding wheels, and handling equipment. This simple, but critical, change in workshop practice completely eliminated the problem, protecting the product's quality and our client's reputation. It’s a powerful lesson in how crucial downstream handling is to performance.
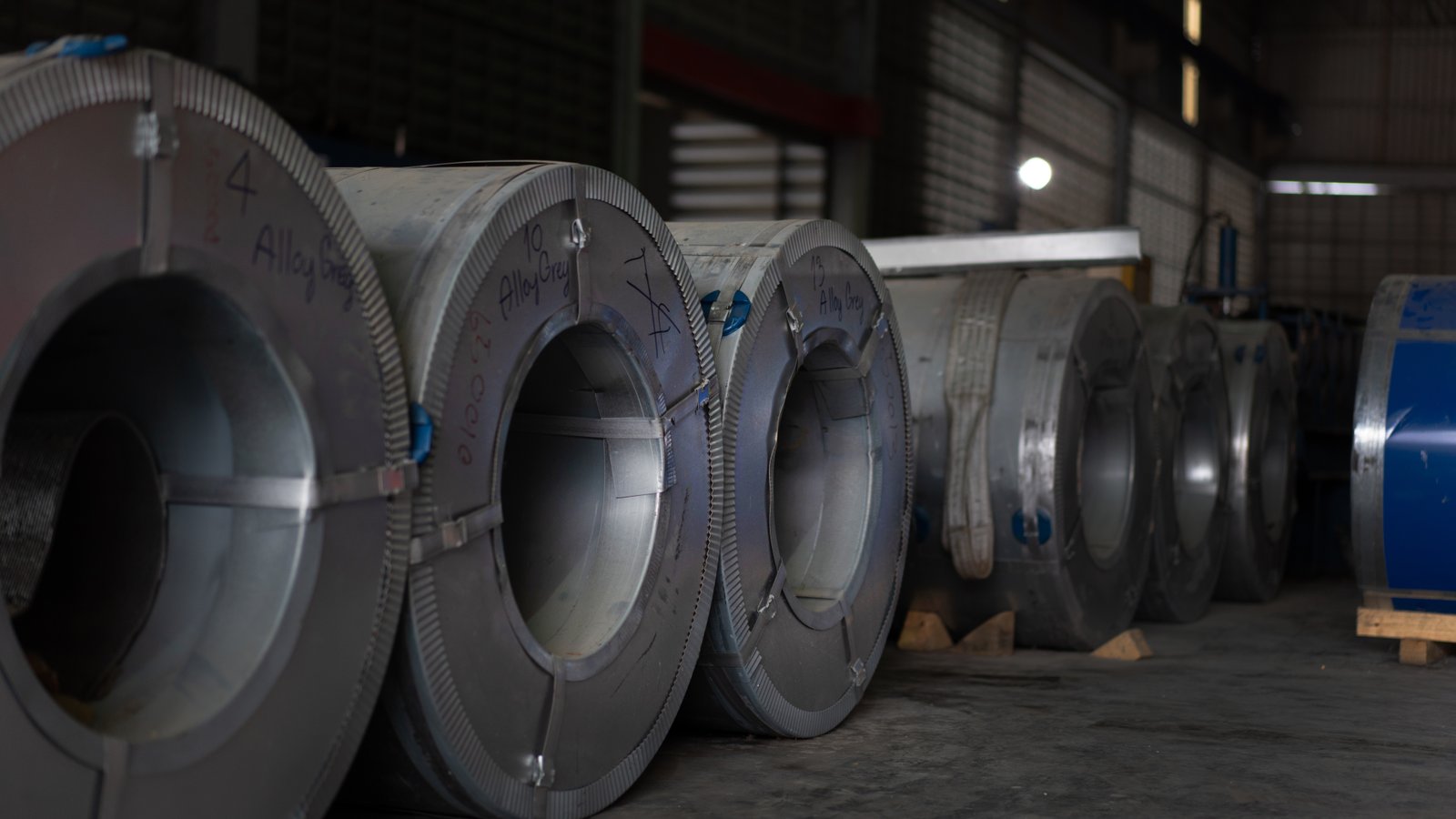
The superior properties of stainless steel are not automatic; they must be preserved and enhanced through proper technical practices. From the moment a coil arrives at your facility to the final finishing of the product, every step matters. Small oversights in handling, fabrication, or cleaning can compromise the material's integrity and lead to disappointing results. At MFY, we believe that providing a high-quality coil is just the beginning. We are committed to sharing the technical knowledge our clients need to transform that coil into a superior finished product. These recommendations are essential for anyone serious about quality and long-term performance.
Proper Storage and Handling
The optimization of stainless steel begins the moment the coil arrives at your facility. The material's passive chromium-oxide layer8, which provides its corrosion resistance, can be damaged by contamination and improper handling. To protect this crucial feature, stainless steel coils and sheets should always be stored in a clean, dry, and sheltered environment, away from industrial pollutants and, most importantly, away from any carbon steel or iron materials. Contact with carbon steel can lead to iron contamination, which disrupts the passive layer and can cause localized rusting, defeating the purpose of using stainless steel in the first place.
When handling the material, best practice dictates the use of dedicated equipment. Lifting straps, clamps, and forklift tines that are used for carbon steel should never be used for stainless steel unless they are thoroughly cleaned and protected with non-contaminating materials like wood or plastic. Workers should wear clean gloves to avoid leaving fingerprints, which can become visible after certain chemical treatments or in critical aesthetic applications. I once visited a client's facility where they had meticulously planned every aspect of their fabrication process but had overlooked storage. Their stainless coils were stored outdoors next to their carbon steel inventory, exposed to rain and industrial dust. Correcting this single issue, by moving the coils to a dedicated indoor rack, significantly improved the surface quality of their final product and reduced their pre-polishing cleaning time.
This disciplined approach to storage and handling is the foundation of quality work. It is a low-cost, high-impact practice that prevents many of the most common surface-quality issues. It ensures that the material entering the fabrication stage is in pristine condition, ready to be transformed without any pre-existing compromise to its integrity.
Grade-Specific Fabrication Techniques
Different families and grades of stainless steel behave differently during fabrication. Applying a one-size-fits-all approach is a recipe for failure. For instance, the austenitic grades9 (like 304 and 316) are known for their high work-hardening rate. During machining or forming operations, they become harder and stronger very quickly. This requires the use of powerful, rigid machinery, sharp tooling, and slower speeds with heavier feeds compared to carbon steel. Attempting to machine austenitic stainless steel with light cuts will only serve to glaze and harden the surface, dramatically reducing tool life and resulting in a poor finish.
Welding also requires grade-specific knowledge. As mentioned previously, standard austenitic grades can be susceptible to sensitization if held at high temperatures for too long, leading to intergranular corrosion. This is why low-carbon "L" grades (e.g., 316L) are specified for many welded applications. In contrast, duplex stainless steels, which have a mixed austenite-ferrite microstructure, require careful control of heat input and cooling rates during welding to maintain the proper phase balance, which is critical to their strength and corrosion resistance. Using the wrong filler metal or welding procedure can destroy the properties of this high-performance material.
At MFY, we provide our clients with detailed technical datasheets that include recommendations for fabrication. For a client fabricating pressure vessels from our duplex coils, our technical team provided specific Welding Procedure Specification (WPS) guidelines to help them achieve the required phase balance and mechanical properties in their weldments. This level of specific guidance is crucial for translating the potential of an advanced material into real-world performance. It highlights the need to treat each grade as a unique material with its own set of rules.
Cleaning and Passivation Post-Fabrication
The final and perhaps most crucial technical step is the cleaning and, if necessary, passivation of the finished stainless steel component. Fabrication processes like welding, grinding, and machining can damage or contaminate the passive layer. Welding, for example, produces a heat-tinted oxide scale near the weld, which has a lower chromium content and is less protective than the original passive film. Similarly, grinding can embed abrasive particles or iron contaminants into the surface. If these are not removed, they will become initiation sites for corrosion.
A thorough cleaning routine is therefore essential. This typically involves removing any gross contaminants and then using a nitric acid or citric acid bath (passivation) to restore a uniform and robust chromium-oxide passive layer over the entire surface, especially on and around welds and ground areas. For a client manufacturing sanitary tubing for the dairy industry, we emphasized the importance of a final passivation step. This process removes any free iron left from the manufacturing process and maximizes the corrosion resistance, ensuring the tubes meet the stringent hygienic standards of the industry.
The table below provides a simplified guide to post-fabrication cleaning, a topic we frequently discuss with equipment integrators and manufacturing clients.
Contaminant / Issue | Recommended Cleaning Action | Purpose |
---|---|---|
Dirt, grease, fingerprints | Degreasing with an alkaline or solvent cleaner | General cleaning to prepare surface for further treatment. |
Weld heat tint (oxide scale) | Pickling (using nitric-hydrofluoric acid paste/bath) or mechanical abrasion | Removes the low-chromium oxide layer to expose fresh material underneath. |
Embedded iron particles | Chemical passivation (nitric or citric acid bath) | Dissolves free iron and chemically enhances the passive chromium-oxide layer. |
Minor scratches / abrasions | Mechanical polishing followed by passivation | Restores aesthetic uniformity and ensures a passive surface. |
Proper final cleaning and passivation are not optional cosmetic steps; they are critical technical procedures that guarantee the stainless steel will perform as designed. It is the final act of quality assurance that locks in the material's inherent corrosion resistance for its entire service life.
Stainless steel requires grade-specific fabricationTrue
Different stainless steel grades (like 304 vs duplex) have unique machining and welding requirements for optimal results.
Carbon steel tools are safe for stainlessFalse
Using carbon steel tools contaminates stainless surfaces with iron particles, creating corrosion initiation sites.
Conclusion
Ultimately, understanding a stainless steel coil—from its history and applications to its challenges and technical nuances—is key to strategic sourcing. By partnering with an integrated supplier like MFY, you transform this essential material from a simple commodity into a source of competitive strength and innovation.
-
Learn strategies to optimize cost and build a resilient procurement strategy ↩
-
Discover the essential functions and growing importance of stainless steel coils in industries. ↩
-
Understand the benefits and common uses of bright annealed finish in automotive applications. ↩
-
Understand why 316L offers better corrosion resistance in marine environments ↩
-
Learn about the market dynamics affecting nickel and chromium prices ↩
-
Learn about MFY's tools to help manage price volatility and improve purchasing strategies. ↩
-
Learn about contamination issues leading to rust spots on 304 stainless steel ↩
-
Understand how the passive layer protects stainless steel from corrosion ↩
-
Discover the unique properties of austenitic stainless steel grades ↩
Have Questions or Need More Information?
Get in touch with us for personalized assistance and expert advice.