Stainless Steel Sheet Weight Calculator: Gauge, mm & kg Conversion Made Easy
Struggling with complex stainless steel sheet calculations? The process of deciphering gauges, converting them to millimeters, and accurately estimating weights for shipping and project costing can often feel like a frustrating puzzle, leading to potential errors and inefficiencies in your planning.
Calculating the weight of a stainless steel sheet requires understanding the gauge system for thickness, converting that gauge to a precise millimeter value, and then applying a formula using the sheet's dimensions and the specific density of the steel grade. This process is fundamental for accurate procurement and logistics.
From my experience as Global Business Director at MFY, I’ve seen countless clients grapple with these conversions. Getting them right isn't just an academic exercise; it's a critical factor that directly impacts your budget, logistics, and project timelines. Accurate calculations prevent over-ordering and waste while ensuring you have the exact material needed to keep production moving forward smoothly.
This guide is designed to be your go-to resource, moving beyond simple formulas to provide a deeper, more practical understanding. We'll explore the nuances that can make or break your project's budget and efficiency. By mastering these calculations, you're not just buying steel; you're building a more resilient and cost-effective supply chain. At MFY, we believe that empowering our clients with this knowledge is key to navigating the complexities of the global steel market and achieving a true competitive advantage.
How to understand stainless steel sheet gauge sizes?
Ever looked at a gauge chart and felt confused? It's a common problem. The system is counterintuitive—a lower gauge number means a thicker sheet. This simple inversion can easily lead to ordering the wrong material, causing expensive mistakes, fabrication issues, and significant project delays.
Stainless steel sheet gauge is a standardized, dimensionless measurement where smaller numbers denote thicker sheets. This system provides a quick reference for thickness, but converting the gauge to an exact millimeter or inch value is essential for precise engineering, manufacturing, and international trade applications.
This isn't just a theoretical issue. I recall a new client in the automotive sector who was on the verge of ordering a massive shipment based on a misunderstood gauge specification. They were accustomed to one standard, but the quote was based on another, resulting in a thickness difference that would have made the parts completely unusable. The potential financial loss and production downtime were enormous. We managed to catch the error by insisting on clarifying all specifications in millimeters, a core part of our verification process at MFY. This situation highlights why a clear, practical understanding of gauge sizes is mission-critical. It prevents costly errors and ensures that the material you specify is the material you receive. In the following sections, we will break down the origins of the gauge system, compare the different standards you might encounter, and explain why precise unit specification is the gold standard in modern manufacturing and procurement.
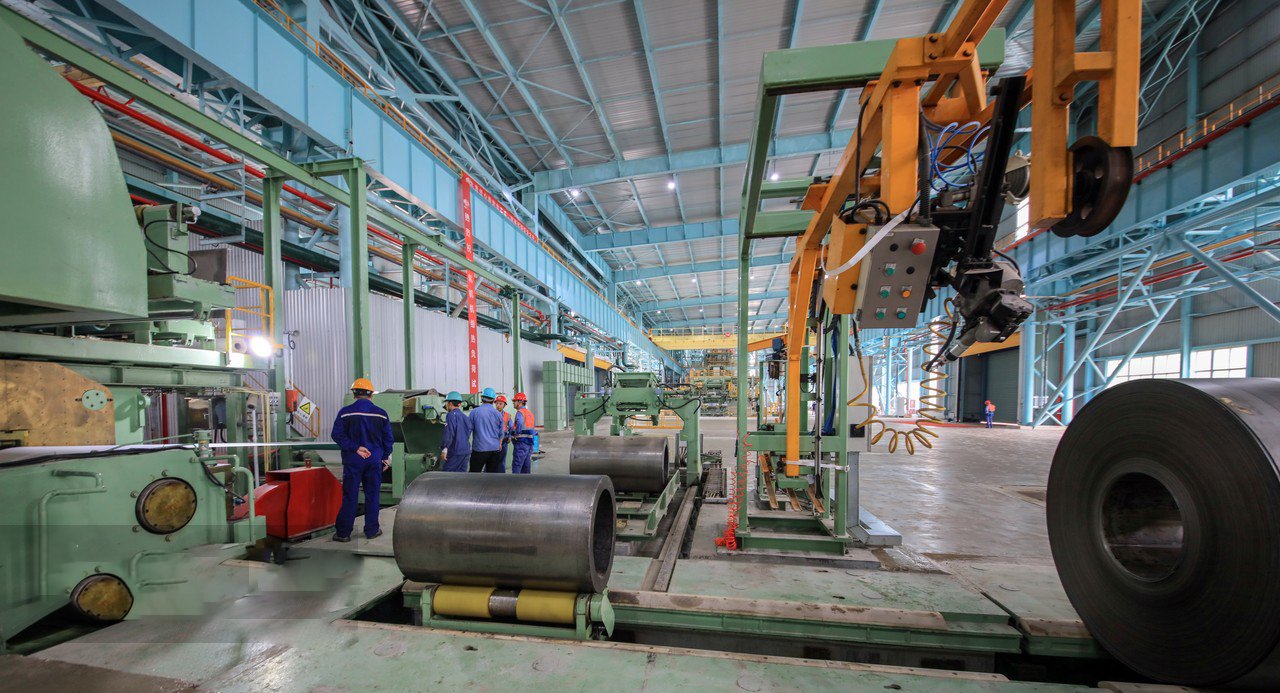
The journey to mastering steel specifications begins with understanding its most traditional, and often confusing, measurement: the gauge. This isn't just about memorizing a chart; it's about appreciating the system's logic, its variations, and its practical limitations in a globalized market. For anyone involved in sourcing, designing, or fabricating with stainless steel, this foundational knowledge is indispensable for ensuring accuracy and avoiding costly missteps. A deep dive into the gauge system reveals why modern industries are increasingly moving towards more universal and precise units of measurement.
The Origins and Logic Behind the Gauge System
The gauge system's logic, or seeming lack thereof, is rooted in the history of metalworking. Before the advent of precise digital calipers, thickness was often described by the process used to create it. For wire and sheet metal, this involved a series of "drawing" operations where the metal was pulled through successively smaller dies or rollers to reduce its thickness. The gauge number originally corresponded to the number of drawing steps the metal had undergone. More drawings (a higher gauge number) resulted in a thinner product, which is why the system is inverted—10 gauge is thicker than 20 gauge.
This historical context is crucial because it also explains the system's inherent lack of universal standardization. Different industries and regions developed their own drawing processes and, consequently, their own gauge systems. For instance, the system used for steel sheets is different from the one used for aluminum or copper, and different again from the standards for electrical wire. The Manufacturers' Standard Gauge (MSG) became the predominant standard for stainless steel, but other systems like the Birmingham Wire Gauge (BWG) or Standard Wire Gauge (SWG) also exist, creating a landscape ripe for confusion if not specified correctly.
At MFY, we often encounter this issue when dealing with international clients. A request for "16 gauge sheet" requires immediate clarification: which standard are they using? Assuming the wrong one can lead to a thickness variance of up to 10%, a difference significant enough to compromise a project's structural integrity or manufacturing tolerances. This historical ambiguity is precisely why our technical teams are trained to always convert and confirm specifications in millimeters, creating a universal language of precision.
Comparing Common Gauge Standards in the Steel Industry
To illustrate the potential for confusion, it's helpful to compare some of the different gauge standards directly. While the Manufacturers' Standard Gauge (MSG) is most common for stainless steel in North America, other standards are prevalent elsewhere. Understanding the subtle but critical differences is key to accurate global sourcing. Let's look at a comparison of a few key gauges across different standards.
Gauge Number | Manufacturers' Standard Gauge (MSG) for Stainless Steel (mm) | Standard Wire Gauge (SWG) (mm) | Birmingham Wire Gauge (BWG) (mm) |
---|---|---|---|
10 | 3.57 | 3.25 | 3.40 |
14 | 1.98 | 2.03 | 2.11 |
18 | 1.27 | 1.22 | 1.24 |
22 | 0.79 | 0.71 | 0.71 |
As the table clearly shows, the same gauge number can refer to different thicknesses depending on the system. A classic case we handled involved an engineering contractor in India responsible for a large-scale commercial kitchen project. Their specifications called for "18 gauge" stainless steel for countertops and paneling. They received quotes from various global suppliers, and the prices varied significantly. Upon investigation, we discovered some suppliers were quoting based on SWG, while others used MSG. The slight difference in thickness (1.27mm for MSG vs. 1.22mm for SWG) not only affected the material cost but also had implications for the product's durability and weldability. By helping them standardize their request to MSG and specify the millimeter equivalent, we enabled them to compare quotes accurately and procure the correct material for their high-quality standards.
Practical Implications for Procurement and Fabrication
The ambiguity of gauge systems has profound practical implications that extend beyond the initial procurement phase. In fabrication, consistency is everything. Automated machinery, bending brakes, and welding parameters are all calibrated for a specific material thickness. If a batch of 14 gauge material is suddenly 5% thinner than the previous one because it came from a supplier using a different standard or wider tolerance, it can wreak havoc on a production line. Bending angles will be incorrect, weld penetration may be insufficient, and the structural integrity of the final product could be compromised.
Furthermore, procurement teams must be vigilant about how specifications are listed on quotes and purchase orders. Simply stating "20 gauge 304 stainless steel sheet" is not enough. A robust purchase order should specify the standard (e.g., "per MSG") and, ideally, the nominal thickness in millimeters along with the acceptable tolerance range (e.g., "1.0mm ±0.05mm"). This level of precision eliminates ambiguity and provides a contractual basis for quality control upon delivery.
For our clients in the Middle East's rapidly growing construction sector, who rely on vast quantities of stainless steel for architectural cladding and structural components, this precision is non-negotiable. The visual and physical alignment of thousands of panels depends on uniform thickness. This is why MFY’s entire process, from production at our cold-rolled mills to final export documentation, is anchored in clear, universally understood metric specifications. We ensure that our clients' calculations and production planning are built on a foundation of certainty, not approximation.
Lower gauge means thicker sheetTrue
The gauge system is inverted - smaller numbers indicate thicker stainless steel sheets.
Gauge standards are universalFalse
Different industries and regions use different gauge systems (MSG, SWG, BWG) with varying thicknesses for the same gauge number.
How to convert gauge to millimeters in stainless steel sheets?
Need to translate a gauge number into a precise millimeter measurement for your CAD designs or CNC machinery? Relying on rough estimates or outdated mental notes is a risky strategy in modern engineering, where precision is paramount. A small error can have big consequences.
To convert stainless steel sheet gauge to millimeters, you must reference a standard gauge to mm conversion chart specific to the gauge system, such as the Manufacturers' Standard Gauge (MSG). There is no direct mathematical formula; it is a fixed mapping where each gauge number corresponds to a precise mm value.
The act of converting gauge to millimeters might seem like a simple clerical task, but it's a critical control point where project success is often determined. The difference between 1.2mm and 1.25mm might look negligible on paper, but in high-precision applications, it can be the difference between a perfect fit and a costly failure1. I worked with a client in Russia that was developing a new line of advanced surgical instruments. Their entire design and prototyping process was based on metric units with extremely tight tolerances. Their previous material supplier, however, only communicated in gauges. This "translation" step became a major source of anxiety and potential error. We were able to provide a solution by supplying certified 316L stainless steel sheets with a guaranteed nominal thickness in millimeters, backed by comprehensive Mill Test Certificates (MTCs). This removed the ambiguity and allowed their engineering team to proceed with confidence. This section will go beyond just providing a conversion chart. We will explore the critical concept of manufacturing tolerances and make the case for why specifying in millimeters from the outset is the superior approach in today's global marketplace.
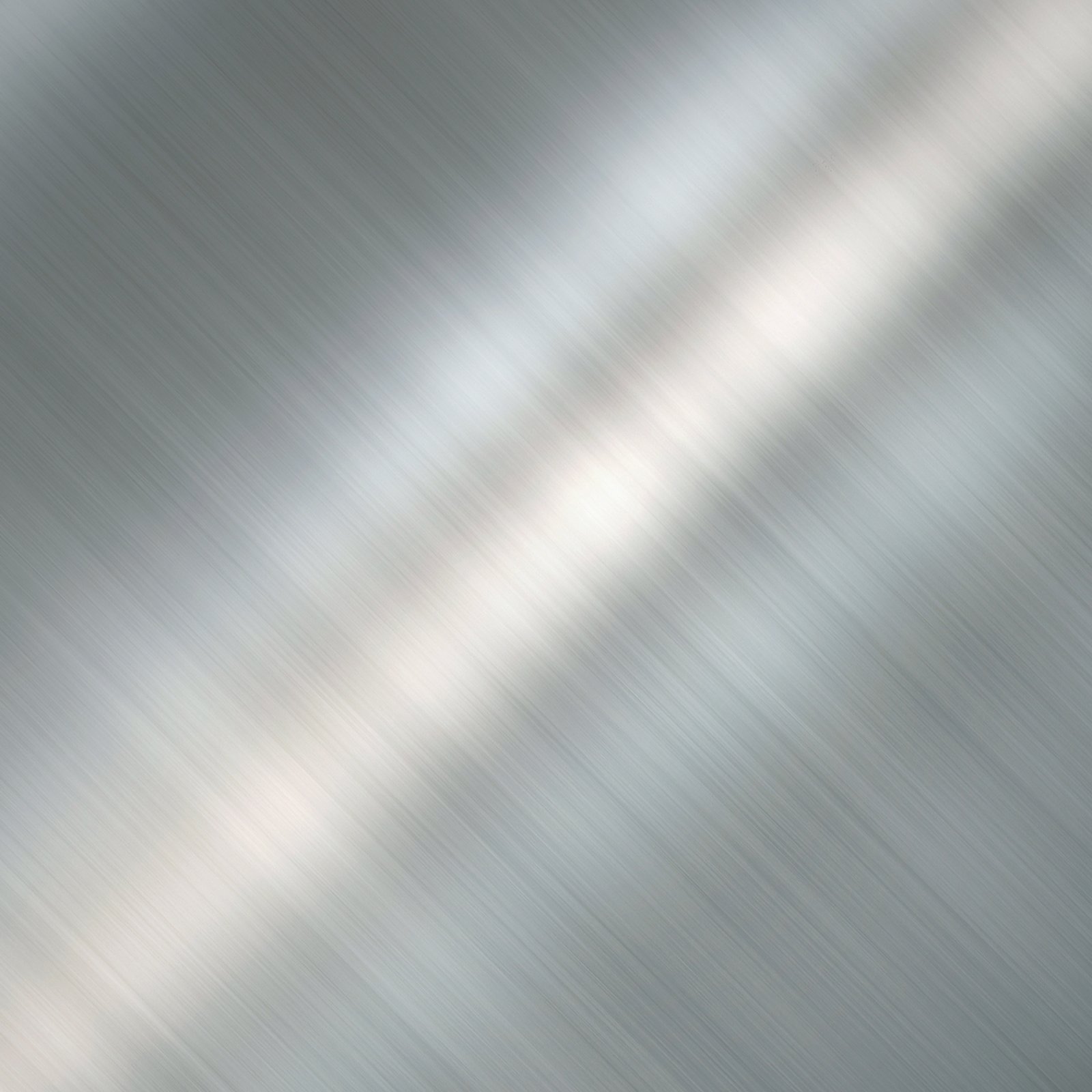
While a conversion chart is the primary tool for this task, a deeper understanding of the context surrounding these numbers is what separates amateurs from professionals. The specified thickness of a sheet is not a single, absolute value but a nominal target within an acceptable range. This concept of tolerance, combined with the push for universal standards in international trade, makes a compelling case for moving beyond gauge entirely and embracing the clarity of metric units. This shift in perspective is fundamental to achieving true precision and efficiency in any sophisticated manufacturing or construction endeavor.
Using a Standard Gauge to MM Conversion Chart
The most direct way to convert gauge to millimeters is by using a standard conversion chart for the specific material you are working with. For stainless steel, the Manufacturers' Standard Gauge (MSG) is the most widely used reference in many parts of the world. It's essential to use the correct chart, as a chart for carbon steel or aluminum will yield different and incorrect values for stainless steel due to differences in density and industry standards. Below is a partial conversion chart for common stainless steel gauges according to the MSG standard.
It is crucial to treat this chart as the definitive source. Unlike unit conversions such as inches to millimeters, which are based on a mathematical constant, gauge conversions are based on an established industry standard. There is no formula to derive that 12 gauge is 2.78mm; it is a value set by the standard. Therefore, having a reliable and accurate chart from a trusted source, like a reputable supplier or an industry standards organization (e.g., ASTM), is paramount for any engineer or procurement specialist.
Understanding Thickness Tolerances
A critical concept that must be understood alongside any gauge conversion is that of manufacturing tolerances. The nominal thickness listed on a chart (e.g., 1.27mm for 18 gauge MSG2) is a target value, not an absolute guarantee for every square inch of the sheet. All rolled steel products are manufactured to a specific thickness tolerance, which is the permissible deviation from the nominal thickness. These tolerances are defined by standards such as ASTM A480/A480M for flat-rolled stainless and heat-resisting steel plate, sheet, and strip.
For example, a 1.27mm sheet might have a thickness tolerance of ±0.10mm. This means the actual thickness at any point on the sheet could range from 1.17mm to 1.37mm. For many general applications, this range is perfectly acceptable. However, for high-precision applications, such as in the aerospace industry or for medical devices, this variance could be critical. In such cases, buyers may need to specify restricted thickness tolerances, a service that specialized producers like MFY can often provide. A construction contractor we work with in the UAE, who specializes in high-end architectural facades, relies on our ability to supply sheets with tight tolerances. For their projects, visual consistency is key, and even minor thickness variations can create visible "waviness" or alignment issues across large surfaces. Understanding and specifying the required tolerance is just as important as specifying the nominal thickness itself.
Why Direct Millimeter Specification is King in Global Trade
Given the potential for confusion between different gauge systems and the reality of manufacturing tolerances, the most effective and professional approach in a globalized market is to bypass gauges altogether. Specifying the required thickness directly in millimeters (or inches, though metric is the global engineering standard) is the undisputed king of clarity. This practice eliminates any ambiguity related to which gauge standard is being used and puts the focus squarely on the actual, measurable property that matters to the design and function of the product.
When you send a purchase order to a global supplier like MFY that specifies "304L Stainless Steel Sheet, 1.5mm thickness (tolerance ±0.1mm)," there is no room for interpretation. It is a universal language that the engineer in Germany, the procurement manager in India, and the mill operator in China can all understand perfectly. This aligns directly with our mission at MFY to streamline the global stainless steel supply chain. By championing the use of clear, metric specifications, we reduce friction, minimize errors, and accelerate the process of getting our clients the exact materials they need. For any company engaged in international trade, adopting a "millimeters-first" policy for specifications is a simple but powerful step towards greater efficiency and risk reduction.
Gauge to mm requires specific chartsTrue
There's no mathematical formula - gauge conversions rely on standardized charts like MSG for stainless steel.
All gauge charts are identicalFalse
Different materials (stainless vs aluminum) have unique gauge charts due to density and industry standards.
How to calculate the weight of a stainless steel sheet in kilograms?
Trying to plan your logistics and budget your material costs? Simply guessing the weight of your stainless steel order is a surefire way to face unexpected freight charges and mismanage your inventory. These inaccuracies can quickly erode your project's profitability.
To calculate the weight of a stainless steel sheet in kilograms, you use the formula: Weight (kg) = Length (m) × Width (m) × Thickness (mm) × Density. The density factor for most common austenitic stainless steels (like 304 and 316) is approximately 8.0.
This formula is more than just a piece of math; it's a fundamental tool for operational efficiency. At MFY, where we coordinate large-scale exports to markets across Asia and the Middle East, every single kilogram matters. Accurate weight calculations are the bedrock of our logistics planning. I worked with a distributor client in Southeast Asia who initially struggled with optimizing their container shipments. By adopting this precise weight calculation formula, they transformed their procurement strategy. They could calculate the exact tonnage to maximize each container's capacity, significantly reducing their per-unit freight costs and improving their inventory turnover. This simple, effective calculation gave them a real competitive edge. In this section, we will dissect this formula, ensuring you understand each component. We'll provide practical examples and explain the subtle but important role that material density3 plays, empowering you to achieve the same level of logistical and financial control in your own operations.
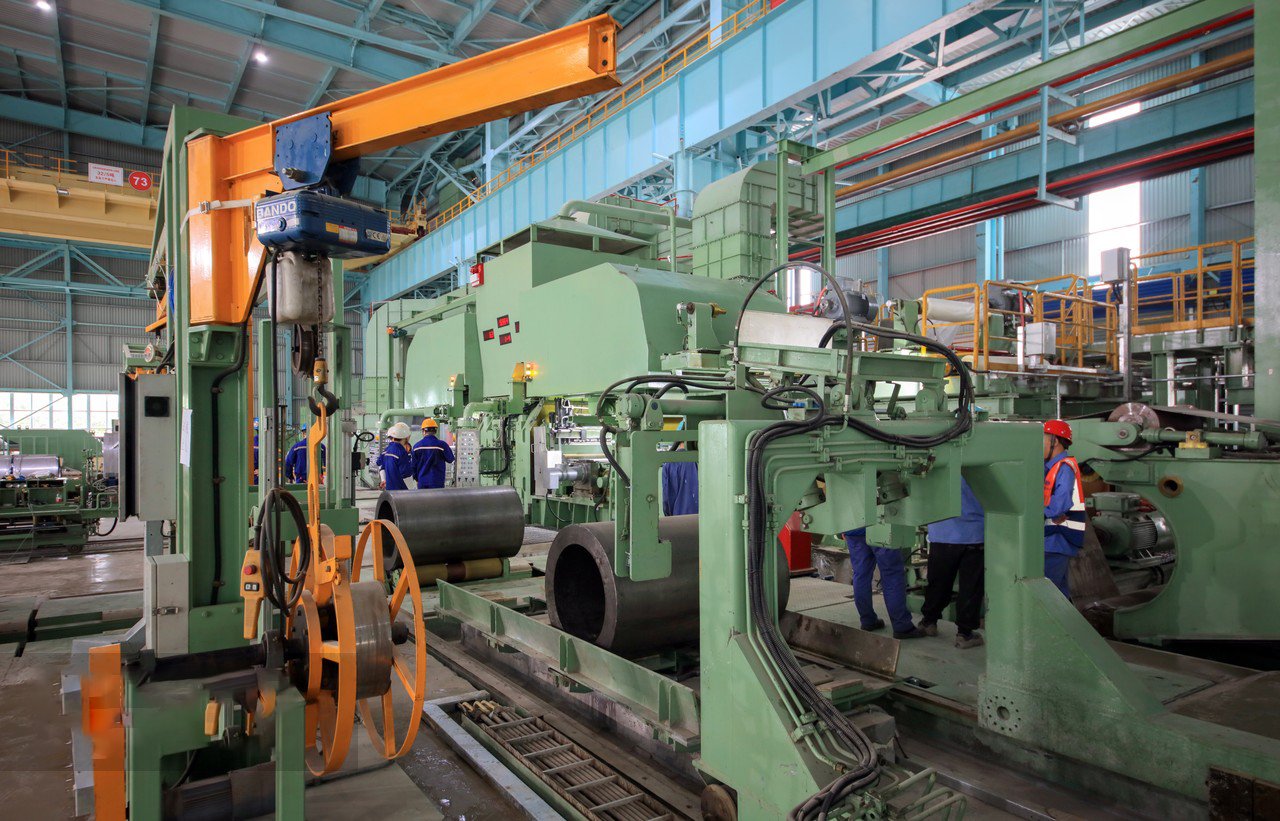
Mastering this calculation is a fundamental skill for anyone managing steel inventory or project costs. It transforms logistics from a guessing game into a precise science. But the formula itself is only half the story. The accuracy of your result depends entirely on the accuracy of your inputs, particularly the density value, which can vary between different grades of stainless steel. A thorough understanding of these variables is essential for turning a good estimate into a bankable number, ensuring your projects remain on budget and your shipments are optimized for maximum efficiency.
The Core Formula and Its Components Explained
The formula for calculating the weight of a stainless steel sheet is straightforward, but its power lies in its precision. Let's break down each component to ensure there's no ambiguity:
Weight (kg) = Length (m) × Width (m) × Thickness (mm) × Density
- Length (m): This is the length of the sheet measured in meters. It's critical to convert any measurements from feet, inches, or millimeters into meters for the formula to work correctly. For example, a sheet that is 2,500mm long would be entered as 2.5m.
- Width (m): Similarly, this is the width of the sheet, also measured in meters. A sheet that is 1,250mm wide would be 1.25m.
- Thickness (mm): This is the nominal thickness of the sheet, measured in millimeters. This is the one unit that is not in meters, which is a common convention in the industry and is accounted for by the density factor's units.
- Density: This factor represents the density of the specific stainless steel alloy. For most common 300-series austenitic stainless steels like 304, 304L, 316, and 316L, the density is approximately 8,000 kg/m³. The formula simplifies this by using a factor of 8.0, whose units are effectively kg/m²/mm. For other grades, like the 400-series ferritic stainless steels4, this value will be slightly different (closer to 7.8). Using the correct density value is crucial for accuracy.
This formula provides the theoretical weight of the sheet, which is the standard used for quoting, selling, and logistics planning across the industry.
Step-by-Step Calculation with a Practical Example
Let's put the formula into practice with a real-world scenario. Imagine you need to calculate the weight of a single sheet of 304 grade stainless steel with the following dimensions:
- Length: 2.5 meters
- Width: 1.25 meters
- Thickness: 3.0 millimeters
Using the formula:
Weight (kg) = Length (m) × Width (m) × Thickness (mm) × Density
-
Insert the values:
Weight = 2.5 m × 1.25 m × 3.0 mm × 8.0 -
Perform the multiplication:
Weight = (2.5 × 1.25) × 3.0 × 8.0
Weight = 3.125 m² × 3.0 mm × 8.0
Weight = 9.375 × 8.0
Weight = 75 kg
So, one sheet of this size weighs approximately 75 kilograms. Now, imagine you need to order a full container load of 25 metric tons (25,000 kg). You can easily calculate how many sheets you can fit: 25,000 kg / 75 kg/sheet ≈ 333 sheets. This kind of precise calculation is exactly what an equipment integrator client of ours in Southeast Asia does. They construct large industrial storage tanks and use this formula, often powered by our online calculator, to plan their exact material requirements for massive projects. This meticulous planning prevents over-ordering, saves on material costs, and minimizes storage needs on a busy project site.
The Critical Role of Density: Comparing Different Stainless Steel Grades
While using 8.0 as the density factor is a reliable standard for the most common stainless steels, it's important to recognize that different grades have slightly different densities. This is due to the varying elemental compositions; for example, nickel-heavy alloys are denser than those with high chromium and low nickel content. While the differences may seem small, they can become significant when calculating the weight of a large order.
Here is a table illustrating the approximate density factors for a few different grades:
Stainless Steel Grade | Typical Density Factor (kg/m²/mm) |
---|---|
201 | 7.9 |
304 / 304L | 8.0 |
316 / 316L | 8.0 |
430 | 7.8 |
Let's recalculate our previous example using a sheet of 430 grade stainless steel instead of 304.
Weight = 2.5 m × 1.25 m × 3.0 mm × 7.8
Weight = 73.125 kg
The difference is almost 2 kg per sheet. If you were ordering 300 sheets, that's a difference of nearly 600 kg! This could impact shipping brackets, handling capacity, and final cost. This is why at MFY, our technical sales team always confirms the exact grade before finalizing a quote. This demonstrates a deep product knowledge that goes beyond just the dimensions, ensuring our clients' calculations are based on the specific properties of the material they are purchasing. It’s this attention to detail that builds trust and ensures the entire supply chain runs smoothly.
304 stainless steel density is 8.0True
The density factor for common 300-series stainless steels like 304 is approximately 8.0 kg/m²/mm.
Thickness is measured in metersFalse
Thickness in the formula is measured in millimeters, not meters, which is an industry standard convention.
How can you ensure accuracy in weight calculations?
You have the right formula, but are you still concerned about small errors creeping into your weight calculations and causing bigger problems down the line? You should be. Even minor inaccuracies can compound across large orders, leading to surprise freight costs, customs issues, and logistical friction.
To ensure accuracy in stainless steel weight calculations, you must use the correct density for specific grades of stainless steel, meticulously convert all dimensions to the proper units (meters and millimeters), and account for manufacturing tolerances by using the specified nominal thickness. Finally, always double-check your inputs.
Accuracy in our industry is not just a goal; it's a requirement. I've seen firsthand how a seemingly trivial miscalculation can disrupt an entire project. A client shipping to a major port once used a generic steel density for a specialty duplex stainless steel order. The actual weight of the shipment was significantly higher than the declared weight. This discrepancy resulted in the container being flagged, pulled for inspection, and ultimately delayed for weeks, incurring massive demurrage fees and jeopardizing the project timeline. This costly experience reinforced our commitment at MFY to a process built on verification and cross-checking. This section is about embedding that same discipline into your own workflow. We will cover the common pitfalls that go beyond simple arithmetic and provide you with a practical framework to ensure your numbers are not just close, but correct.
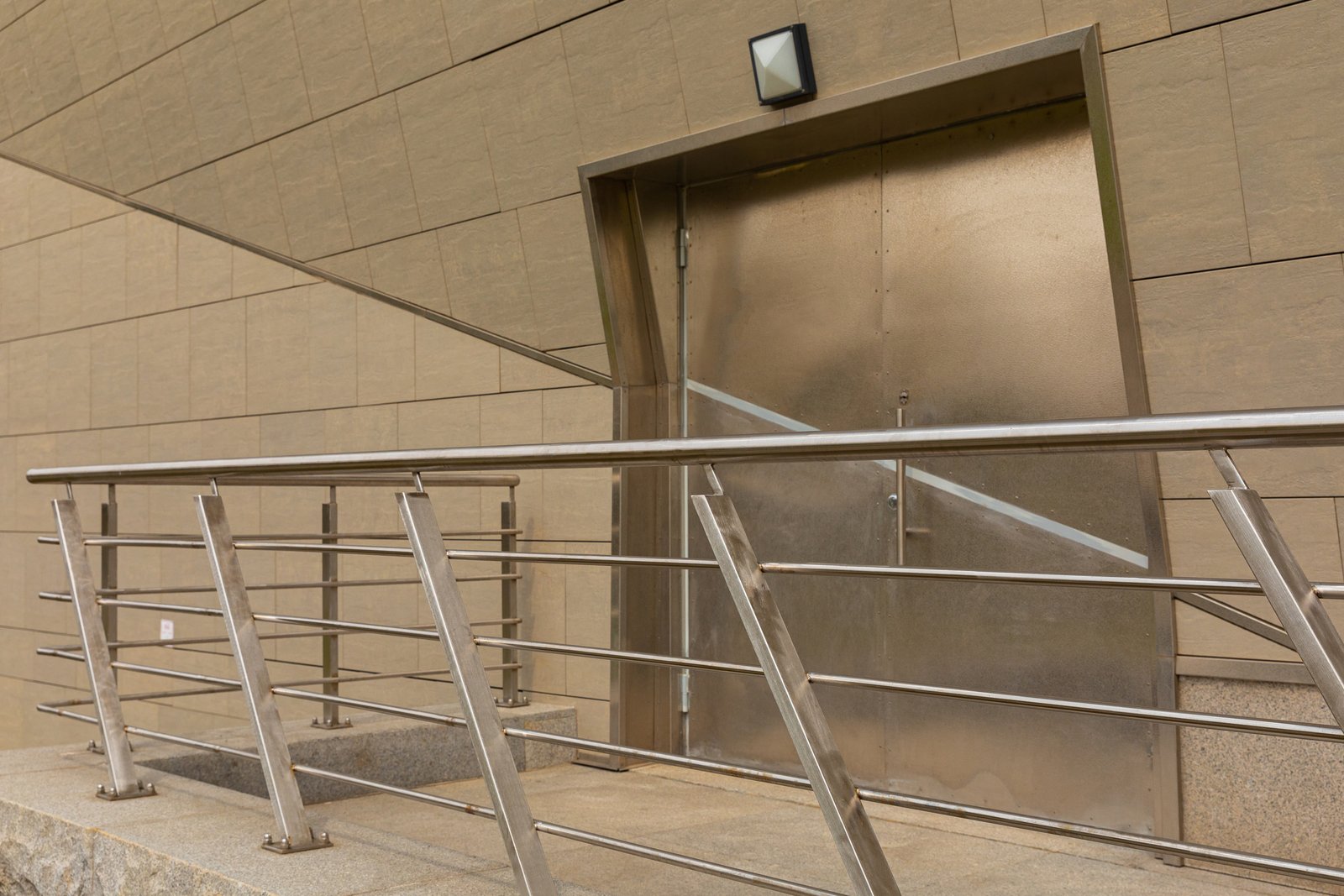
Achieving certifiable accuracy in weight calculations requires a disciplined approach that goes beyond the formula itself. It demands a rigorous verification of every input, from the material's fundamental properties to the consistency of the units used. By treating each component of the calculation with meticulous attention to detail, you can eliminate the common sources of error and build a reliable, trustworthy foundation for all your logistical and financial planning. This diligence is the hallmark of professional operations management in the steel industry.
Verifying the Material Density
The most common and impactful error in weight calculation, aside from a simple math mistake, is using the wrong density value. As we've discussed, not all stainless steel is created equal. The density of a 400-series ferritic steel is noticeably different from that of a 300-series austenitic steel. Using a default value of 8.0 kg/m²/mm for a grade like 430 (which has a density closer to 7.8) will result in an overestimation of the weight by over 2%. On a 25-tonne shipment, that's an error of 500 kg.
To prevent this, the first step is to always verify the exact grade of stainless steel you are ordering. Is it 304, 316, 430, or 201? Once confirmed, use the specific density associated with that grade. A reliable supplier like MFY will always make this information readily available on our technical data sheets or through our sales representatives. For our clients, we make it a point to include the material density on our quotes to ensure complete transparency and provide them with the right data for their own verification processes. This simple act of confirming the density is a crucial checkpoint for accuracy.
The Importance of Unit Consistency
A second classic source of error is inconsistent units. The standard weight formula for steel5 (L(m) × W(m) × T(mm) × Density
) is designed to work with a specific combination of units: meters for length and width, and millimeters for thickness. If your initial measurements are in inches, feet, or centimeters, you must convert them correctly before plugging them into the formula. Mixing units is a guaranteed path to a wildly incorrect result.
Consider an engineering firm we worked with that was designing a complex chemical processing plant. Their project involved teams from different countries, and the drawings they received were a mix of imperial (inches) and metric (millimeters) units. This created significant confusion and led to several near-misses in their initial material quantity take-offs. The solution was to implement a strict project-wide policy to standardize the entire Bill of Materials (BoM) to metric units before any procurement calculations were made. This is a best practice we recommend to all our clients, especially those involved in large, collaborative projects. Enforcing unit consistency eliminates a major variable and a common source of human error, making the entire process more robust.
Accounting for Manufacturing Tolerances and Coatings
Finally, for applications where weight is absolutely critical (such as aerospace, high-performance automotive, or mobile structures), it's important to understand the role of manufacturing tolerances. As previously noted, the actual thickness of a sheet can vary slightly from the nominal thickness within a defined tolerance range (e.g., per ASTM A480/A480M). The weight calculated using the nominal thickness[^3] is the theoretical weight, which is the standard for commercial transactions. However, the actual weight of the shipment may vary slightly.
For most commercial purposes, this variance is negligible and accepted. But if you are loading a vehicle right up to its maximum legal weight limit, this slight difference could matter. In these hyper-critical scenarios, engineers might calculate a "worst-case" weight using the upper bound of the thickness tolerance. Furthermore, one must consider if the sheet has any additional coatings or surface treatments that could add weight. A thick protective film or a special coating, while often light, can add up over thousands of square meters. At MFY, our quality control process ensures that our products adhere strictly to the promised nominal thickness and tolerances. This provides our clients with a reliable and consistent baseline, giving them the confidence that the theoretical weight they calculate will be a true and accurate representation of the material they receive.
Material density affects weight calculationsTrue
Different stainless steel grades have varying densities, and using the wrong density value can lead to significant calculation errors.
Unit consistency is unimportant in calculationsFalse
Mixing units (e.g., inches and meters) in weight calculations will lead to incorrect results; consistent units are essential for accuracy.
What tools or calculators help simplify these conversions?
Are you tired of manually looking up conversion charts and punching numbers into a calculator for every single sheet specification? This process isn't just time-consuming; it's a repetitive task that is highly susceptible to human error, introducing risk into your workflow.
Online stainless steel weight calculators are the most efficient tools for simplifying these conversions. These digital platforms, often provided by suppliers like MFY, allow you to simply input the dimensions and grade, and they instantly and automatically execute the gauge-to-mm conversion and final weight calculation.
In today's fast-moving global market, operational efficiency is a key differentiator. While it's essential to understand the manual calculations for context, leveraging technology is what truly gives your business a competitive advantage. This philosophy is at the heart of MFY's commitment to digital innovation6. We developed our own online stainless steel calculator for one simple reason: we saw our clients—from busy distributors managing thousands of SKUs to on-site contractors needing quick answers—spending too much valuable time on manual calculations. Our objective was to create a tool that was not only fast and reliable but also accessible from any device, anywhere in the world. This section will explore the landscape of these digital aids, from simple web-based calculators to more sophisticated, integrated software solutions. We will guide you on how to best leverage these tools to dramatically streamline your workflow, virtually eliminate calculation errors, and empower your team to focus on more strategic, value-added activities.
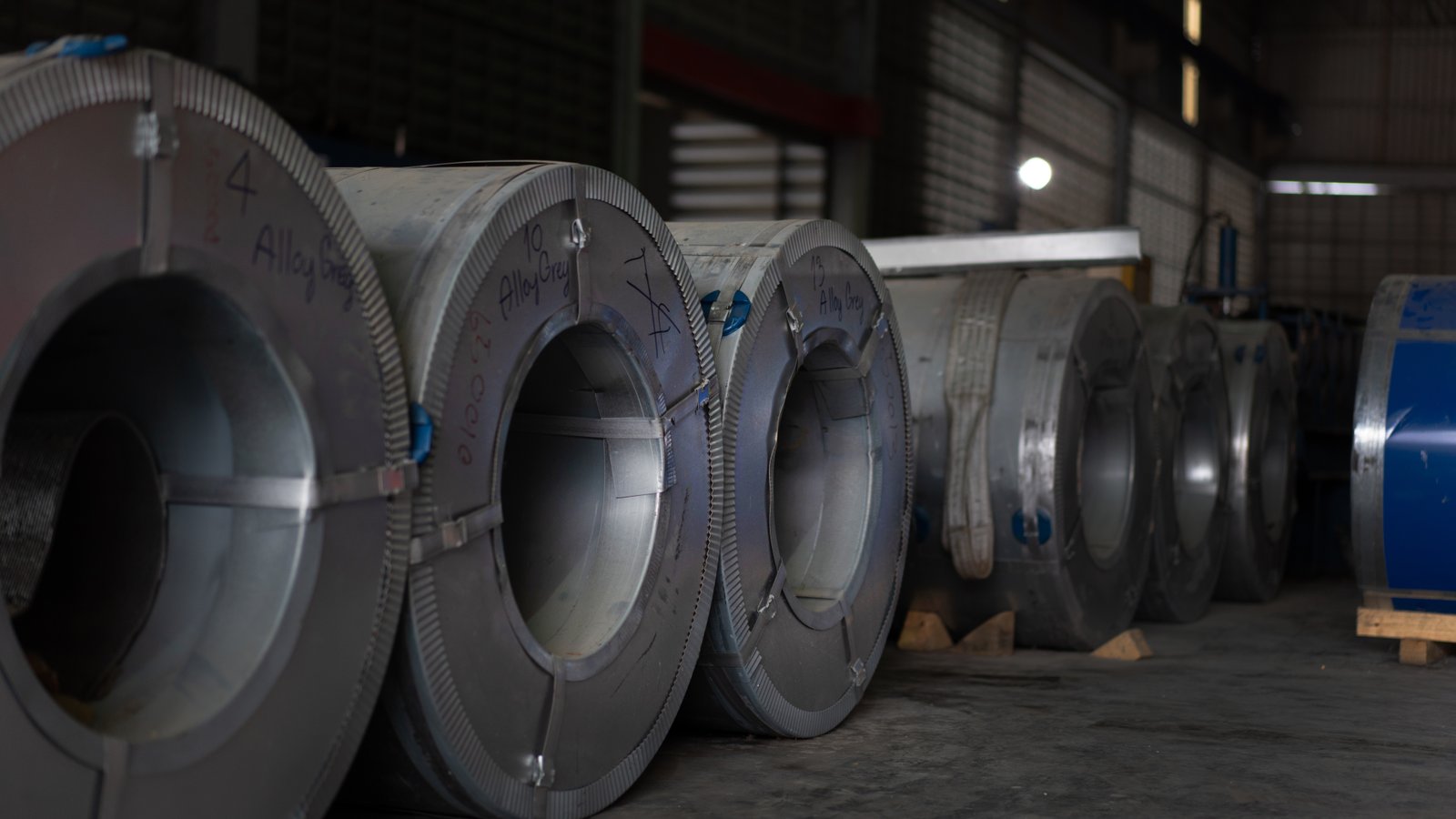
The digital transformation of the steel industry is empowering businesses to work smarter, not harder. Leveraging specialized digital tools is no longer a luxury but a necessity for maintaining a competitive edge. These instruments replace manual, error-prone tasks with automated precision, integrating seamlessly into modern workflows to enhance efficiency from the initial quote to the final delivery. Understanding and adopting these tools is a critical step for any company looking to optimize its procurement and project management processes.
The Rise of Online Steel Weight Calculators
The most accessible and widely used digital tool for this purpose is the online steel weight calculator7. These are typically web-based applications that require no installation and can be used on a desktop or mobile device. The benefits are immediate and obvious:
- Speed: They provide instantaneous results, turning a multi-step manual process into a matter of seconds.
- Accuracy: By automating the process, they eliminate the risk of human error in math or in looking up the wrong value on a chart. They are programmed with the correct densities for various grades and the official gauge-to-mm conversion tables.
- Convenience: They are available 24/7 from anywhere with an internet connection, making them invaluable for teams working across different time zones or for personnel on a project site.
When evaluating an online calculator, look for key features that enhance its utility. A good calculator, like the one on the MFY website, should offer a dropdown menu to select the specific stainless steel grade (e.g., 304, 316, 430), options for different material forms (e.g., sheet, pipe, bar), and the flexibility to input dimensions in various units. This functionality makes it a versatile, one-stop tool for most common calculation needs. We proudly feature our calculator as a prime example of our client-centric approach, providing value beyond the physical product.
Integrating Calculators into Your Workflow
The true power of these tools is realized when they are integrated into your daily business processes. Their application spans multiple departments and stages of a project lifecycle.
- For Estimators and Sales Teams: When preparing a quote for a customer, speed and accuracy are paramount. An online calculator allows them to rapidly determine the material weight, which is a key component of the total cost (material + freight), enabling them to deliver competitive and accurate quotes faster.
- For Engineers and Designers: During the design phase, engineers can use calculators to quickly estimate the weight implications of different design choices or material thicknesses, aiding in optimizing the design for both performance and cost.
- For Procurement and Logistics Managers: This is where calculators are most heavily used. They are essential for planning purchase orders, calculating the total tonnage for a project, and optimizing container or truck loads to minimize shipping costs. A logistics manager can quickly determine if they can add more material to a shipment without exceeding weight limits, thereby maximizing freight efficiency.
We worked with a large manufacturing client who made it standard practice for their procurement team to attach a screenshot of the calculator results to every purchase order. This simple step created an extra layer of verification, ensuring that both their team and our team at MFY were aligned on the theoretical weight of the order, preventing any downstream discrepancies.
Beyond Simple Calculators: The Role of ERP and MRO Software
For larger organizations, the next level of integration involves moving beyond standalone web calculators and incorporating these calculations into their core business software. Enterprise Resource Planning (ERP) and Maintenance, Repair, and Operations (MRO) systems often have built-in modules for material management and procurement that can perform these weight calculations automatically.
For instance, when an engineer adds a list of materials to a project's Bill of Materials (BoM) within the ERP system, the software can automatically calculate the weight of each line item based on the dimensions and material grade stored in its database. This creates a seamless, end-to-end workflow from design to procurement, with weight data automatically populating purchase orders, shipping manifests, and inventory records. Some advanced systems can even connect directly to supplier databases via an API (Application Programming Interface) to pull real-time pricing and stock levels. This level of digital integration represents the future of the industry. At MFY, we understand this evolving tech landscape. Our commitment to digital innovation means we are not only providing easy-to-use tools like our online calculator but also ensuring we can provide the data and support our clients need to integrate our supply chain into their own sophisticated digital ecosystems.
Online calculators reduce human errorTrue
Automated calculations eliminate manual lookup and math mistakes that occur in traditional methods.
ERP systems cannot calculate material weightsFalse
Advanced ERP systems automatically calculate weights when materials are added to a Bill of Materials.
Conclusion
Mastering stainless steel sheet calculations is essential for operational excellence. By understanding gauge systems, accurately converting to millimeters, applying the correct weight formula, and leveraging modern digital tools, you can eliminate costly errors, optimize logistics, and execute your projects with greater precision and confidence.
-
Learn how slight thickness variations affect high-precision engineering projects and product success. ↩
-
Discover established tolerance ranges for stainless steel sheets to ensure accurate engineering results. ↩
-
Understand the impact of material density on precise weight estimation ↩
-
Learn about the specific characteristics of 400-series stainless steel ↩
-
Learn unit conversion best practices to avoid errors in weight calculations. ↩
-
Understand how digital innovation influences the steel industry's efficiency ↩
-
Discover how these tools enhance accuracy and convenience in measurements ↩
Have Questions or Need More Information?
Get in touch with us for personalized assistance and expert advice.